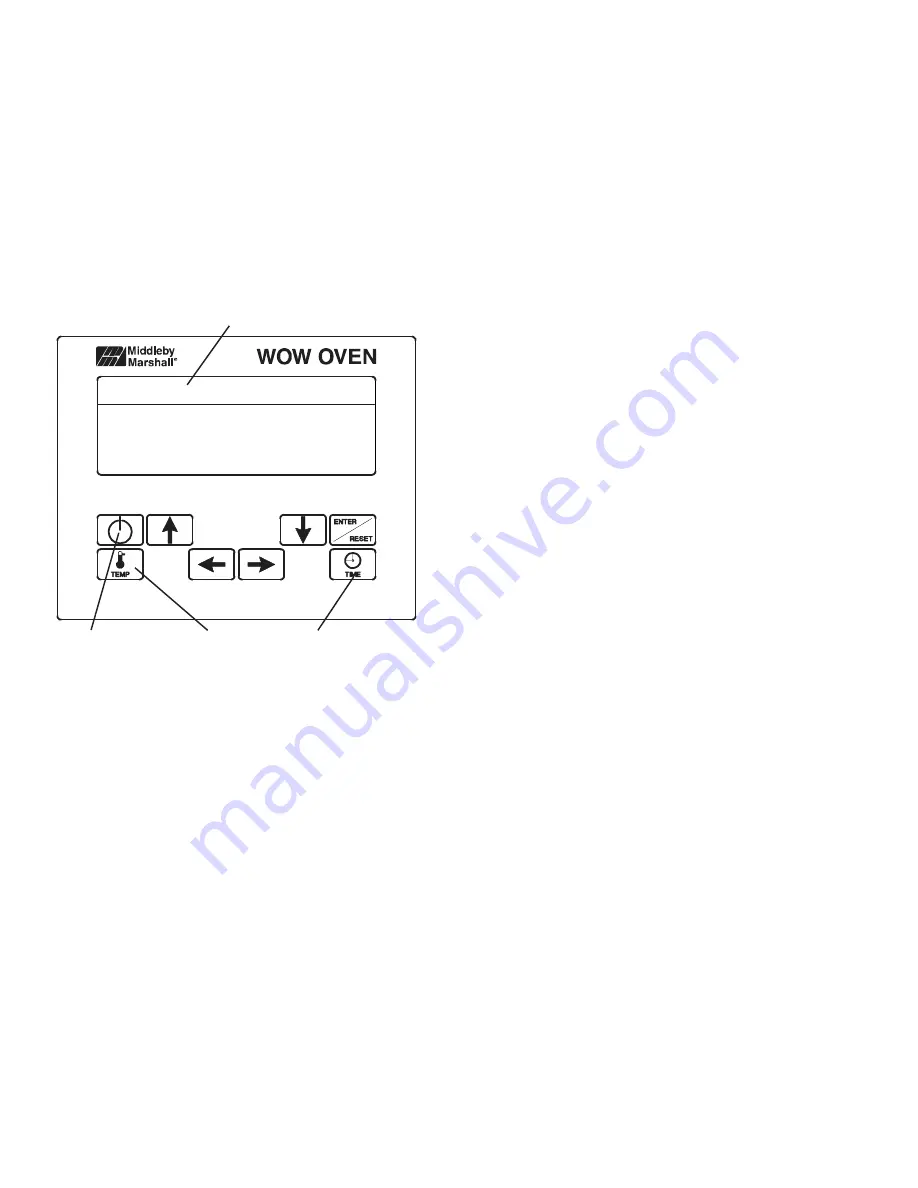
4.
To change the conveyor belt speed, push the “TIME”
button. The controller will display the screen, shown in
Figure 3-5. To change the minute setting, push the “
←
←
←
←
←
”
arrow button. Then push either the “
↑
” arrow or “
↓
” arrow
buttons to increase or decrease the time accordingly. To
change the second setting, push the “
→
” arrow button.
Then push either the “
↑
” arrow or “
↓
” arrow buttons to
increase or decrease the time accordingly. When the
proper times are entered, push the “ENTER/RESET” but-
ton. The controller will now show the display shown in
Figure 3-3.
B.
Daily Startup Procedure
1.
Check that the circuit breaker/fused disconnect is in the On
position. Check that the window is closed. The touch panel
display should be lit.
2.
Adjust the conveyor to the desired bake time.
3.
Press the temperature button to display the oven setting.
Set temperature as desired.
4.
Press the “ON” button to activate the oven. The conveyor
will not run, until the oven temperature has reached the
set points.
BELT 01 SPEED
LEFT FOR MINUTES - RIGHT FOR SECONDS
4m
.
30s
.
C.
Daily Shutdown Procedure
1.
Make certain there are no products left on the conveyor in
the oven.
2.
Press the “ON/OFF” button to turn the oven off.
3.
Open the window to allow the oven to cool faster.
4.
After the oven has cooled and the blowers have turned off, the
circuit breaker/fused disconnect may be turned off.
Quick Reference – Touch Screen Controller
A.
Main Screen
1.
ON/OFF button - Used to turn oven On and Off.
2.
TIME - See Separate Instructions.
3.
TEMP - See Separate Instructions.
4.
Energy level indicators - Indicators to either side of the
screen indicate the energy input to that side of the oven.
5.
Message bar - Indicates various messages pertaining to
current oven conditions.
B.
Oven Temperature/Set Point/Indicator Screen
1.
Actual temperature - Indicates current average tempera-
ture of the right side of the oven.
2.
Set point temperature - Pressing on this value allows the
user to adjust the set point of the oven.
3.
Exit - Returns to the main screen.
C.
Energy Modes
Energy Mode One - This mode is automatic, and starts (bake
time +1 minute) after the last product has entered
the oven. In this mode, the main oven blowers will lower to 1200
RPM, while the oven maintains temperature and belt speed.
Figure 3-5 Belt Speed Screen
ON/OFF button
TIME button
TEMP button
Message Bar
18
Summary of Contents for PS640G
Page 30: ...26 NOTES...
Page 31: ...27 NOTES...