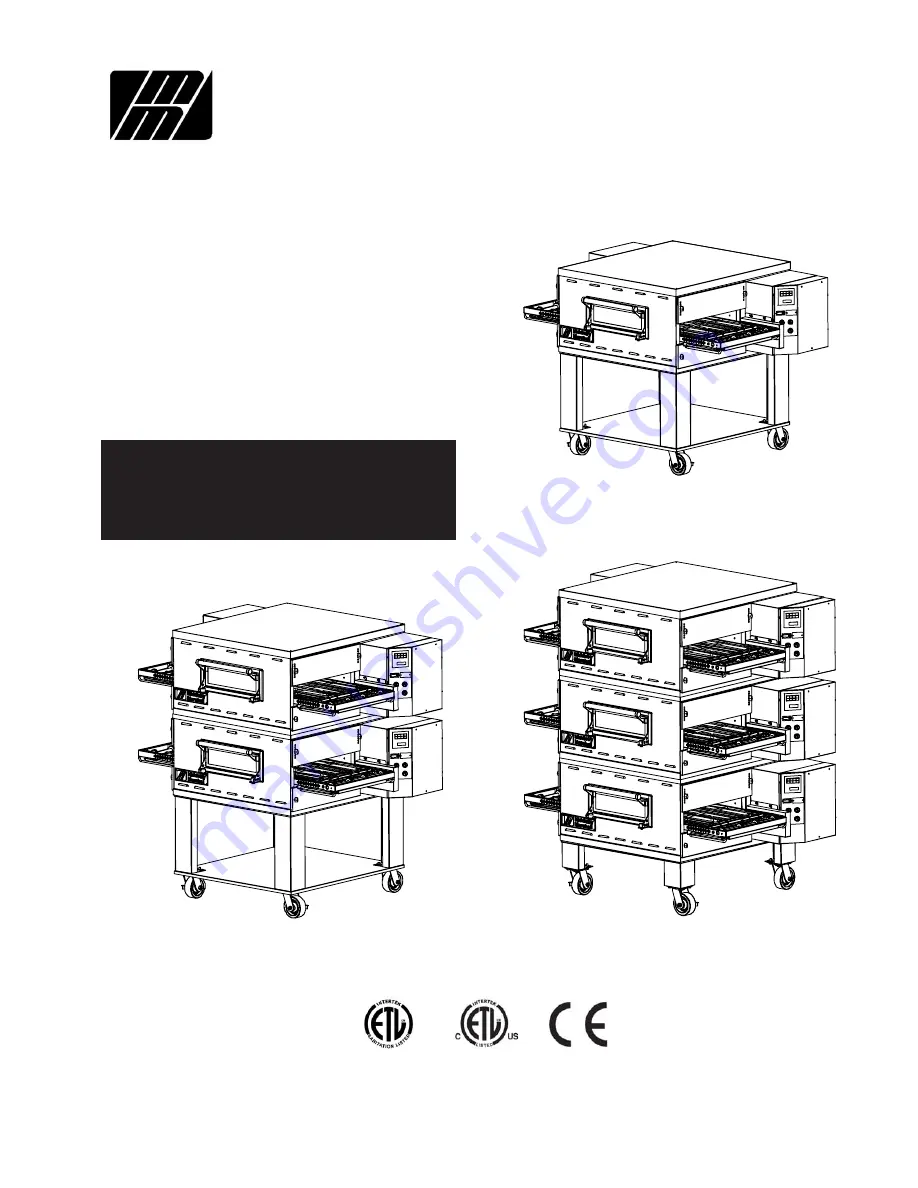
©2005 Middleby Marshall
Inc.
Middleby
Middleby
Middleby
Middleby
Middleby
Marshall
Marshall
Marshall
Marshall
Marshall
A MIDDLEBY COMPANY
PS536-Series Electric Ovens: English
owner's
operating
& installation
manual
PS536-Series OVENS
Model PS536ES
PS536ES (Triple)
PS536ES (Double)
Part No. 58367
Price $30.00
P: 08/08 Rev. B
®
PS536ES (Single)
Summary of Contents for PS536-Series
Page 11: ...SECTION 1 DESCRIPTION 7 Figure 1 8 Cooling Fan...
Page 50: ...SECTION 5 TROUBLESHOOTING 46 NOTES...
Page 51: ...47 ENGLISH SECTION 6 PARTS LIST SECTION 6 PARTS LIST...
Page 52: ...48 ENGLISH SECTION 6 PARTS LIST...
Page 54: ...50 ENGLISH SECTION 6 PARTS LIST...
Page 56: ...52 ENGLISH SECTION 6 PARTS LIST...
Page 58: ...54 ENGLISH SECTION 6 PARTS LIST...
Page 60: ...56 ENGLISH SECTION 6 PARTS LIST...
Page 62: ...58 ENGLISH SECTION 6 PARTS LIST ELEMENT...