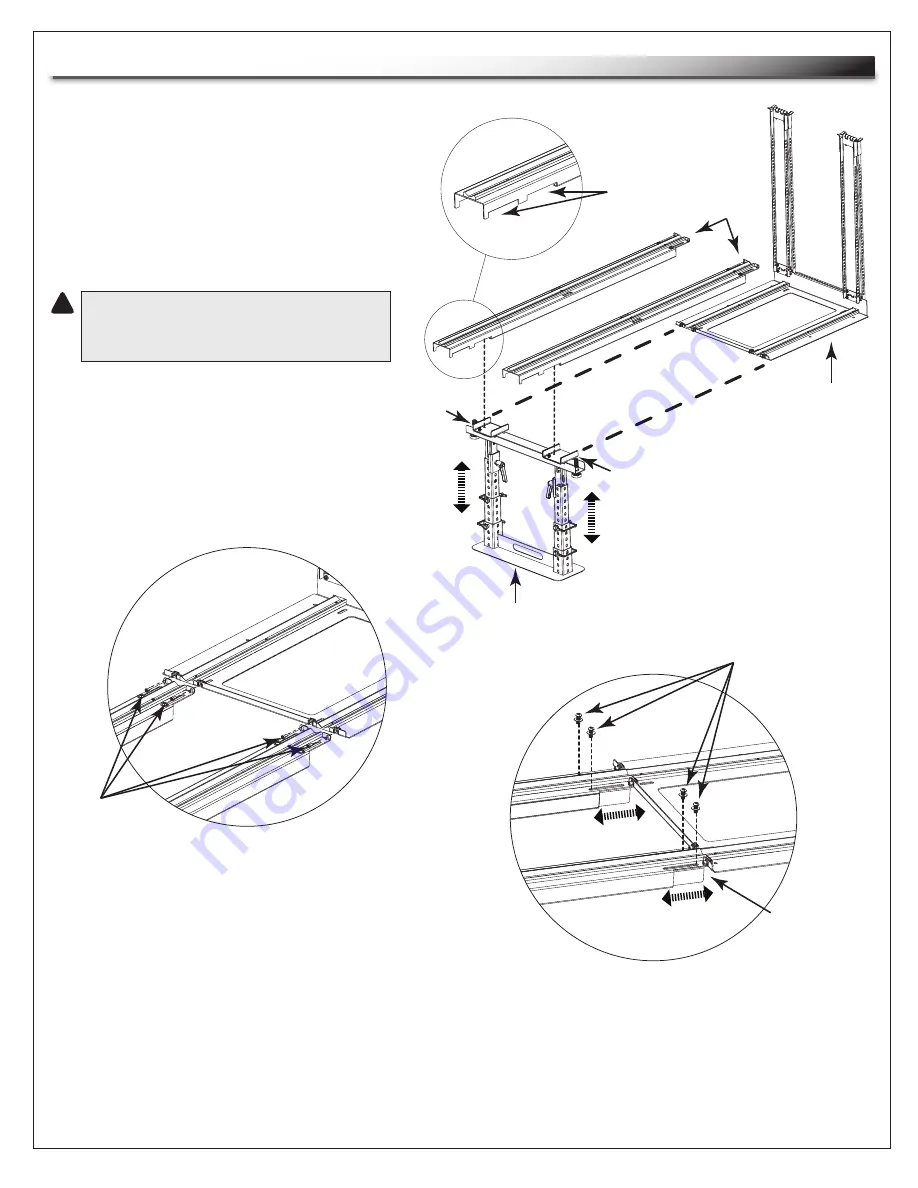
Hex Head
Screws
(2 Per Track)
10-32
Slide Support Screws
(2 Per Track)
SERVICE STAND / SERVICE TRACK ASSEMBLY
Page 12
1) Assemble service stand as per instructions
included with unit.
2) Adjust stand to approximate height of
rough-in pan.
(FIGURE H)
3) Position notched end of each service track on
service stand saddles.
(FIGURE H)
CAUTION!
Be sure notched ends are
fully seated in service stand saddles
to prevent tracks from falling out.
4) Position opposite end of each service
track on millwork.
(FIGURE H)
5) Secure each service track to rough-in
pan using (2) 10-32 hex head
screws (included in service
track hardware kit).
(FIGURE I)
Notches
Saddle
Service
Stand
Service
Tracks
Saddle
Rough-in
Pan
FIGURE H
6) Fine adjust the service stand with
the aid of the level installed in the
service tracks.
7) Extend slide supports on each service
track to meet millwork using slide
support screws (2 per service track).
(FIGURE J)
NOTE:
This adjustment strengthens track when extending heavy equipment for servicing.
FIGURE I
FIGURE J
Slide
Support
!