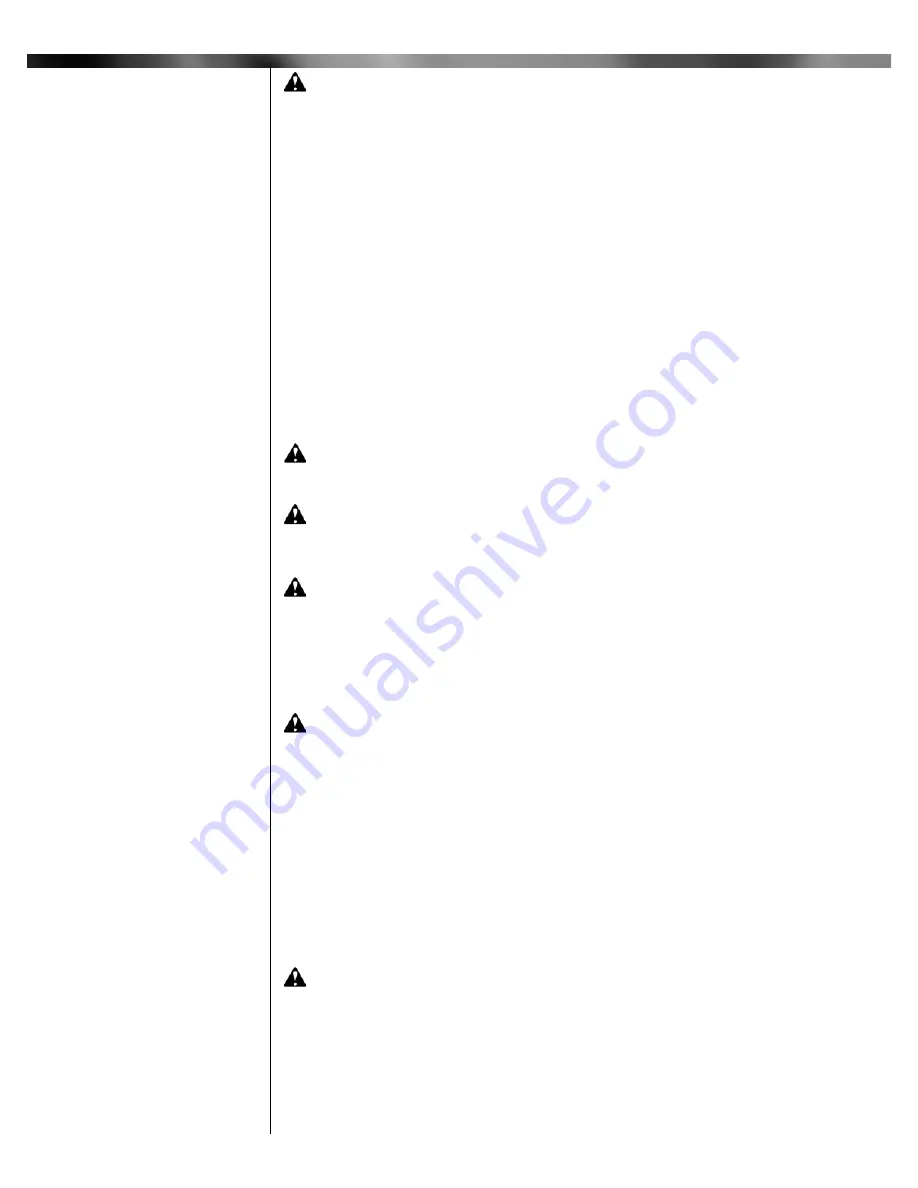
CAUTION: High gas pressure supply lines require the proper pressure
reducing regulators. Install a high pressure regulator of the Tight Shut-Off type
upstream of the low pressure regulator. Sized for main gas input, and suitable for
the minimum flow regulating capacity of the pilot.
The high pressure regulator must be adjustable to 14" W.C. outlet pressure.
When the gas supply line is about to be put into service it must be tested to insure that it
is gas tight. Use air or inert gas under pressure and test with soap and water to locate leaks.
Before gas is turned onto the system, a check must be made to see that there are no open
fittings and to make sure the burner main and pilot manual valves are closed.
After checking for leaks, purge the gas line up to the burner inlet. Purging the air from the
gas supply line at this step will expedite the first light-off.
NOTE:
If there is more than 1.0" W.C. differential in the inlet pressure to the burner
compared to when all other gas utilization equipment are off, refer to Section VI.
____________________________________________
Burners are approved for use with NATURAL gas or PROPANE gas and should be used only
with the gas specified on the rating plate.
The gas input should be set at the heating rate determined by the building heat loss and/or
heating plant survey, but not exceeding the rated maximum input of the gas utilization
equipment or Economite burner.
For orifice selections and gas pressure settings refer to Table 3
____________________________________________
WARNING: Ignition is automatic. Make spark observations into combustion
chamber only with Main and Pilot Manual Shut-Off Valves closed. Confirm that gas
utilization equipment does not contain any accumulated gases. Purge as described in
step 3 below.
CAUTION: Cover plates, guards, and enclosures must be maintained in place
at all times except during maintenance and service.
1.
Check the burner piping and valves for gas leaks by applying a weak liquid soap
solution to unions and joints with the gas supply on. Leakage will be indicated by the
appearance of soap bubbles. Locate and correct all gas leaks before proceeding.
WARNING: DO NOT USE OPEN FLAME.
2.
Purging the air from the gas supply line at this step will expedite first light-off.
IMPORTANT:
Purge outside the building. Do not purge into the gas utilization
equipment.
3.
To purge the gas utilization equipment and chimney of any accumulated gases, turn
main Manual Gas Cock
OFF
, close Pilot Manual Shut-Off Valve, turn burner power on,
and set operating control to
ON
or thermostat to call for heat. Let the blower run long
enough to accomplish four combustion chamber volume air changes, but not less than
five minutes.
CAUTION:Make sure that the capacity range of the burner, manifold pressure,
and the combustion air shutter setting are suitable for capacity rating of the gas
utilization equipment. Refer to Section VIII and Table 3.
4.
RESET
the 24 volt ignition Control Module by setting the operating control to
OFF
or the
thermostat below room temperature for at least 30 seconds.
RESET
the 120 volt
RM7895 control by pushing its reset button. See Section XII.
5.
Confirm that Main and Pilot Manual Shut-Off Valves are open. Turn main Manual Gas
Cock
ON
.
6.
Turn operating control to
ON
or set thermostat above room temperature. After the pre-
purge is complete, the pilot should ignite. Whenever the burner pilot fails to light during
the ignition trial, or if the flame is lost during the burner run and is not reestablished
within 15 seconds after the pre-purge, the ignition system will shut off the Automatic
Safety Shut-off Valves and
LOCK OUT. RESET
the 24 volt ignition Control Module by
setting the operating control to
OFF
or the thermostat below room temperature for at
least 30 seconds.
RESET
the 120 volt RM7895 control by pushing its reset button. If
burner still fails to light, turn it off and repeat from step 4 above. Then if necessary, refer
to the
TROUBLE CHART
to isolate the problem.
WARNING: Repeated unsuccessful attempts to light will result in accumulated
gases in gas utilization equipment and chimney. To prevent these gases from
reaching an explosive level, periodically purge the gas utilization equipment and
chimney as described in step 3 above.
7.
To make a preliminary setting of the burner input, determine the manifold gas pressure
required from Table 3 and adjust the Main Gas Pressure Regulator accordingly. See
Section XI.
Part 1 Installation
9
Part 1
Installation
Continued
VII
Main Gas
Input Selection
VIII
Initial Start-
up /Adjustment
VI
Piping
Continued