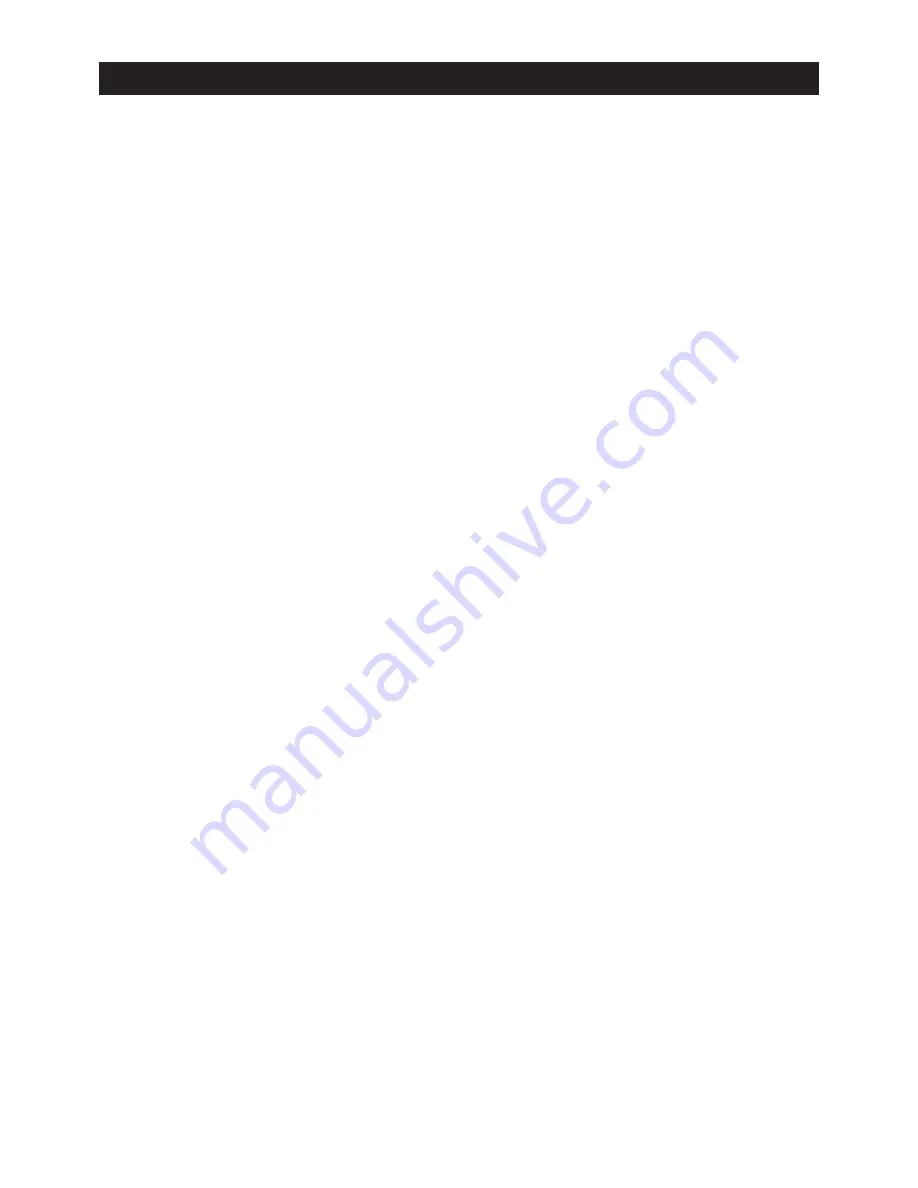
MICRON
turn will emit a heavy white smoke, resulting in a dry joint or damage to the PCB. When the tip working
temperature is within the correct parameters suited to the particular solder being used, a good joint is assured.
The most common solder alloy used in the electronics industry is 60% tin, 40% lead (60/40). The tip working
temperature of solder is detailed below and can vary slightly from manufacturer to manufacturer.
Melting point ......................................................215°C (419°F)
Normal operation ................................................320°C (608°F)
Production line operation ....................................380°C (716°F)
Desoldering operation for small joint ..................320°C (608°F)
Desoldering operation for larger joint ..................400°C (752°F)
To meet RoHS (European requirement for lead free solder), the 60/40 solder alloys are not allowed in the
production process. The RoHS lead free solder alloys require a working temperature of about 30°C (54°F )
higher than typical 60/40 lead/tin soldering.
The lead free solder working temperature is detailed below and can vary from manufacturer to manufacturer.
Melting point ..........................................220°C (428°F)
Normal operation......................300-360°C (572-680°F)
Production line operation..........360-410°C (680-770°F)
IMPORTANT:
The temperature above 410°C (770°F) is not recommended for normal soldering functions, but
can be used for short periods of time when high temperatures are required.
Please note
that the lead free
solder alloys require a higher soldering temperature which shortens tip life.
COMMON CAUSES OF TIP UNWETTING (solder not taking)
1. Tip temperature higher than 410°C (770°F).
2. The tip working surfaces are not well tinned while the iron is idling.
3. Lack of flux in soldering, wicking, repairing, and touch-up, etc operation.
4. Wiping tip on a high sulphur content sponge, dirty or dry sponge, and/or rag.
5. Contact with organic materials such as plastic resins, silicone grease and other chemicals.
6. Impurities in solder and low tin content.
TIP REPLACEMENT AND CARE OF TIPS
Caution:
The soldering iron can be very hot. Be sure to turn the unit off prior to carrying out any maintenance
or trouble shooting steps listed below.
IMPORTANT
Remove and clean the tip daily. Tips can be changed or replaced simply by unscrewing the
knurled nut barrel assembly. The station must be switched off and allowed to cool before this operation as
damage may result if the system is left on without the tip inserted.
If a new tip is installed, or to maintain the current tip, remove any loose build up in the barrel assembly,
otherwise the tip may fuse to the heating element or retaining barrel. After removing the tip, blow out any oxide
dust that may have formed in the tip retaining area of the barrel. Be careful to avoid getting dust in your eyes.
Replace the tip and screw back the knurled nut barrel assembly using only firm hand pressure to tighten. Pliers
4