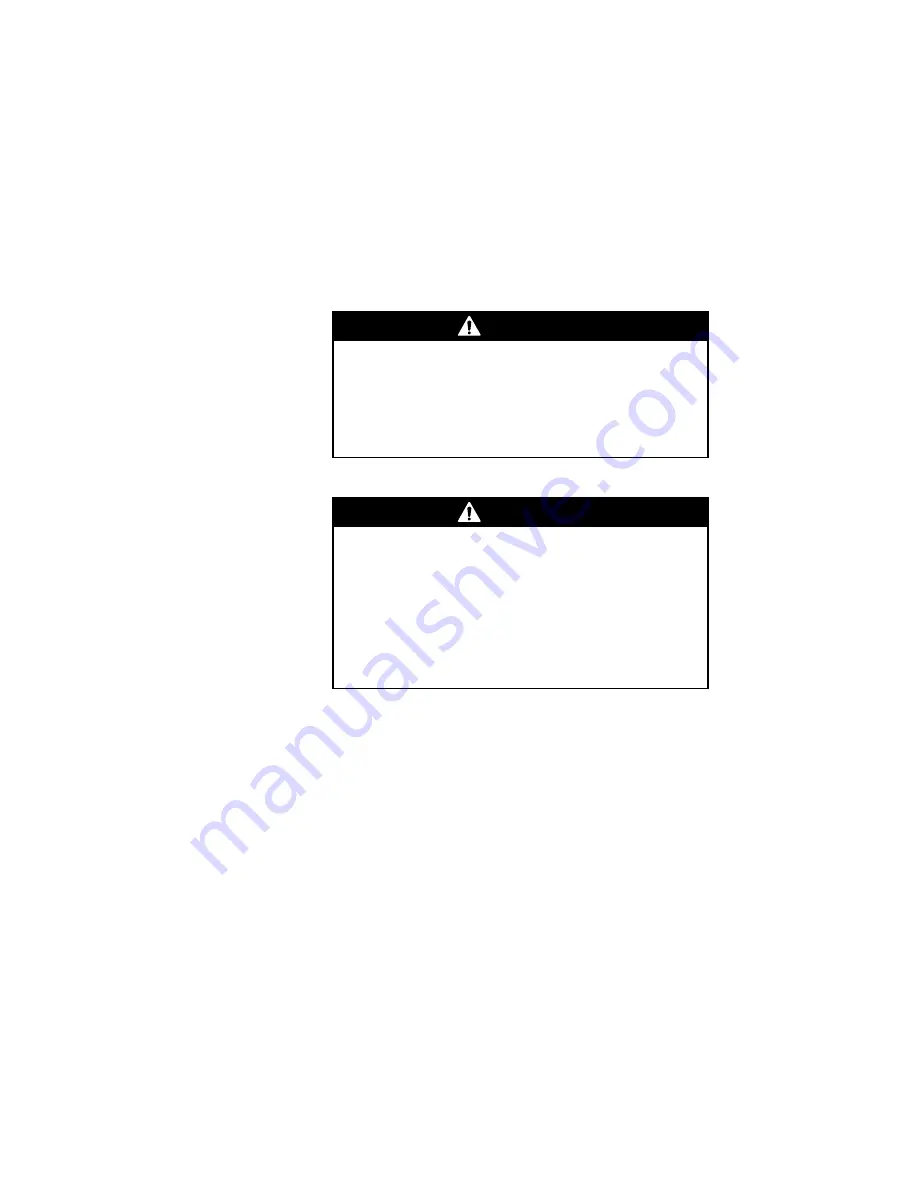
22
RFT9739 Rack-Mount Transmitter Instruction Manual
Power-Supply and Sensor Wiring
continued
4.4
Sensor wiring
The instructions in this section explain how to connect a fully prepared
Micro Motion flowmeter cable to the RFT9739 and a sensor. The sensor
can be a Micro Motion ELITE, F-Series, Model D, DL, or DT sensor.
• The procedure for preparing Micro Motion flowmeter cable and cable
glands is described in the instructions that are shipped with the cable.
• Install cable and wiring to meet local code requirements.
• Use Micro Motion color-coded cable.
• Total length of cable from the sensor to the transmitter must not exceed
1000 feet (300 meters).
Cable connections to
sensor and transmitter
The wiring procedure is the same for the sensor and transmitter. Refer to
the wiring diagrams on pages 23 through 24, and follow these steps:
1. Insert the stripped ends of the individual wires into the terminal
blocks. No bare wires should remain exposed.
• At the sensor, connect wiring inside the sensor junction box.
• At the transmitter, connect wiring to the transmitter's intrinsically
safe sensor terminals for sensor wiring, as numbered in Table 4-2,
page 23. The transmitter terminal block can be unplugged for easier
connection of wiring.
2. Locate the wires by color as indicated in Table 4-2, page 23.
3. Tighten the screws to hold the wires in place.
4. Tightly close the sensor junction-box cover. On an ELITE sensor
junction box, tighten all four cover screws.
CAUTION
Improper installation of cable or conduit could cause
inaccurate measurements or flowmeter failure.
Keep cable away from devices such as transformers,
motors, and power lines, which produce large magnetic
fields.
CAUTION
Failure to seal sensor junction box could cause a
short circuit, which would result in measurement error
or flowmeter failure.
To reduce risk of condensation or excessive moisture in
the sensor junction box:
• Seal all conduit openings.
• Install drip legs in conduit or cable.
• Fully tighten junction box cover.
Summary of Contents for Fisher Rosemount RFT9739
Page 1: ...Model RFT9739 Rack Mount Transmitter Instruction Manual Version 3 Transmitters February 2000 ...
Page 2: ......
Page 4: ......
Page 20: ...10 RFT9739 Rack Mount Transmitter Instruction Manual ...
Page 26: ...16 RFT9739 Rack Mount Transmitter Instruction Manual ...
Page 92: ...82 RFT9739 Rack Mount Transmitter Instruction Manual ...
Page 100: ...90 RFT9739 Rack Mount Transmitter Instruction Manual ...
Page 110: ...100 RFT9739 Rack Mount Transmitter Instruction Manual ...
Page 112: ...102 RFT9739 Rack Mount Transmitter Instruction Manual ...
Page 120: ...110 RFT9739 Rack Mount Transmitter Instruction Manual ...
Page 122: ...112 RFT9739 Rack Mount Transmitter Instruction Manual ...
Page 129: ......