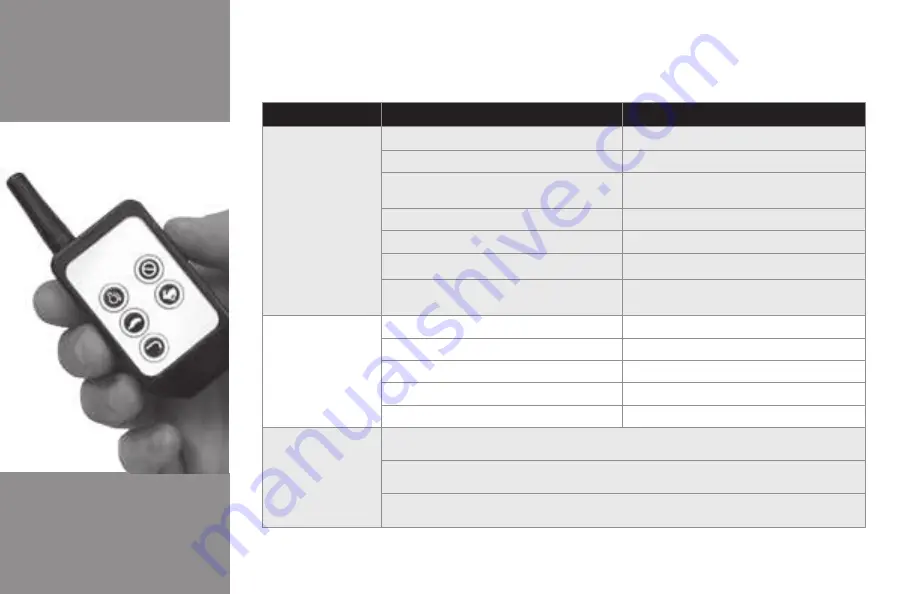
66
67
Troubleshooting Guide
Wireless Controller
Troubleshooting
Condition
Possible Cause
Correction
Transmitter does not
function
Transmitter is not programmed to the receiver
See programming instructions
Transmitter battery is dead or not installed correctly See transmitter battery replacement instructions
Distance between transmitter and receiver is
greater than
( m)
Reduce distance between transmitter and receiver
Transmitter signal is being obstructed
Move transmitter to a different location
Receiver is defective
See receiver troubleshooting
Transmitter buttons are not being fully depressed
Fully depress transmitter buttons
Multiple transmitters are being operated in the
same area
Transmitters can only be operated one at a time
within the same area
Receiver does not
function
Transmitter is defective
See transmitter troubleshooting
Transmitter is not programmed to the receiver
See programming instructions
Receiver is defective
Replace receiver
Receiver has no power
See receiver has no power troubleshooting
Corresponding spreader component is defective
Replace corresponding spreader component
Wireless Controller
Notes
If red D inside of receiver fails to light when the AR button is depressed, receiver has failed and will need to
be replaced.
Multiple transmitters may be programmed to one receiver, but only one transmitter can be operated within the
same air space at one time.
The wireless controller is a rugged unit. Generally any issue can be resolved simply by reprogramming the transmitter
to the receiver. A WA S attempt to reprogram the wireless controller before replacing any components.
Variable Speed Controller
Troubleshooting
Condition
Possible Cause
Correction
Controller has no power
Controller not turned ON
Move on/off switch to on
Power supply harness connections loose or corroded
Clean and tighten power supply harness connections
Controller internal fuse blown
Replace internal fuse
Controller has power
but conveyor does not
operate
Conveyor harness is not connected to controller
Connect conveyor harness to controller
Conveyor harness connection at rear bumper is
loose or corroded
Clean and reconnect conveyor harness connection
Conveyor harness connections at electric motor
are loose or corroded
Clean and tighten conveyor harness connections
Conveyor speed setting is set too low
Ad ust conveyor speed to a higher setting
Controller internal fuse blown
Replace fuse
Conveyor harness damaged
Replace conveyor harness
Controller has power
but spinner does not
operate
Spinner harness is not connected to controller
Connect spinner harness to controller
Spinner harness connection at rear bumper is
loose or corroded
Clean and reconnect spinner harness connection
Spinner harness connections at electric motor are
loose or corroded
Tighten or replace spinner harness wire nuts
Spinner speed setting is set too low
Ad ust Spinner speed to a higher setting
Controller internal fuse blown
Replace fuse
Spinner harness damaged
Replace spinner harness
Conveyor operates
erratically
Loose or corroded conveyor harness connections
Clean and tighten harness connections
Conveyor speed setting is set too low
Ad ust conveyor speed to a higher setting
Defective electric motor
Replace electric motor
Conveyor harness damaged
Replace conveyor harness
Troubleshooting Guide
Summary of Contents for LPV 3
Page 14: ...14 1 2 3 4 5 6 7 8 9 10 11 12 13 14 15 LPV Component Identification GASOLINE ENGINE...
Page 16: ...16 ELECTRIC LPV Component Identification 1 2 3 4 5 6 7 8 9 10 11 12 13 14 15...
Page 20: ...20 PV Spreader Component Identification ELECTRIC 1 2 3 4 5 6 7 8 9 10 11 12 13 14 15 16 17 18...
Page 26: ...26 ELECTRIC Polyhawk Component Identification 1 2 3 4 5 6 8 9 10 11 12 7 13 14 15 16 17 18 19...
Page 71: ...71 Notes...
Page 72: ...72...