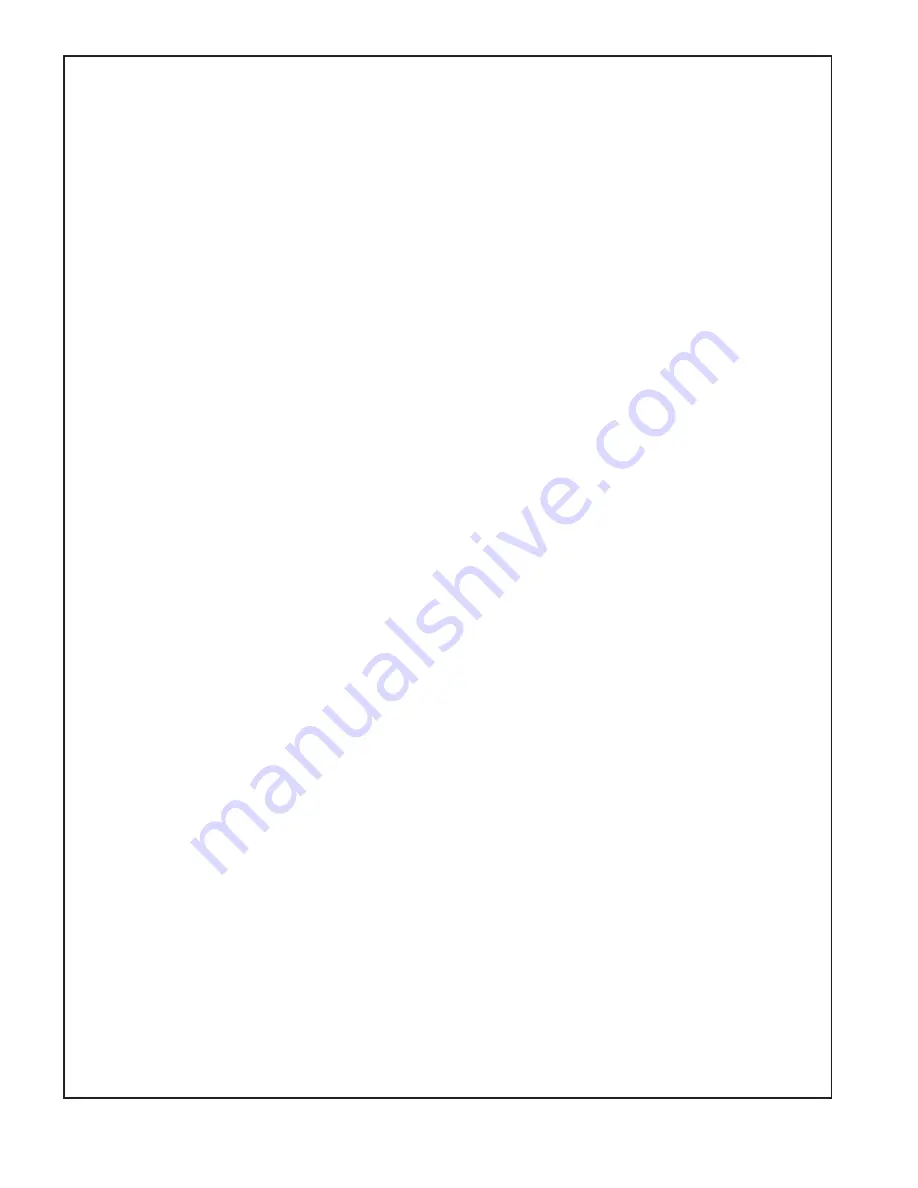
8
B.
STORAGE
1.
If moved to storage, the Equipment should be located in a dry area, preferably inside. Outside
storage will require adequate protection from the weather.
2.
The inlet and outlet of this Equipment should be securely covered to protect the interior while in
storage. For prolonged storage, an anti-rust compound should be applied to all interior surfaces.
See actuator and electrical component instructions for storage recommendations for these items.
3.
After prolonged storage and prior to start-up, the Double Flapgate Valve and its actuator(s) should be
inspected and cleaned by qualified personnel. Contact Wm. W. Meyer & Sons, Inc. if any assistance
is required.
4.
In the event this Equipment is to be stored for an extended period, the following Long Term Storage
procedures are recommended:
a. The Double Flapgate Airlock Valves and any ancillary Equipment supplied (e.g. solenoid valves,
limit switches, regulators, gauges, etc.) should be stored unpacked in a dry, humidity-controlled,
adequately ventilated, indoor area not subject to extreme temperature changes.
b. Flapgates should be stored in an upright position.
c. The interior of the valve should be sprayed with a rust preventative coating
d. All exterior exposed machined surfaces should be sprayed with a rust preventative.
e. All openings must be sealed using pipe caps, plugs or metallic or wooden flange covers. Attach
flange covers using a full flange gasket or weather-proof seal and a minimum of four mounting
bolts.
f. Keep covers on until unit is installed for service.
g. These Equipment storage procedures are the minimum that should be performed. Other special
requirements may supplement this list, as recommended by specific component vendors,
environmental (e.g. corrosive environment) and other factors.
SECTION III
PRODUCT DESCRIPTION
The Double Flapgate Airlock Valve is specifically designed to control the rate of material flow through a
system, while at the same time preventing air leakage by isolating the processing system pressures
from one material handling point to another.
•
HPSC & HPTC (High Pressure)
o
Differential pressure up to 20 PSIG and temperatures up to1650˚F.
•
LPTF (Low Pressure)
o
Differential pressure lower than 1 PSIG and temperatures up to 250˚F.
9
Double Flapgate Airlock Valves are also suitable for conveying material that tends to bridge and
material that is: abrasive, chunky, friable, or difficult to handle.
The application conditions define the materials of construction of the basic valve housing and
components, depending mainly on process temperature, corrosiveness and potential wear. The seals,
bearings, gaskets and use of special features, such as air purge systems, are determined from
operating pressure, temperature, internal gas composition and other factors.
Double Flapgate Airlock Valves consist of two actuated gates that open and close against stationary
mating seats to fill and empty the chambers on top of the upper and lower gates.
The actuating method of the gate will be one of the following:
•
Pneumatic operation
o
One actuator per gate.
Depending on process conditions only one actuator is employed.
o
Two actuators per gate. (HPSC & HPTC only)
Over a certain process pressure, the force required to actuate a gate may require the
use of two pneumatic cylinders, one mounted on each side of each valve.
•
Electro-mechanically motor-driven cam operation with
counterweights
•
Gravity actuated with counterweights
The high-pressure product comes in two basic configurations, HPSC (High Pressure Short) and HPTC
(High Pressure Tall) valves. The short version is most commonly used in applications where height is
limited. The tall version allows for higher volumetric flow rates. A spool piece or “Dutchman” can be
included between the gates to increase the internal volume.
The low-pressure units are only available in specific heights and are not available with different spool
pieces.
The standard materials of construction:
•
HSPC & HPTC are made from mild steel, hi-chrome, stainless steel and Incoloy® depending on
application and temperature.
•
Bearings, seals and gaskets are specific to the application.
•
LPTF is fabricated from mild steel or stainless steel materials with the appropriate bearings,
seals and gaskets.
All the assemblies are comprised of housing, door(s), seat, gate, shaft, gate lever arm, and cylinder
lever arms.
• Seats are mounted in the housing by supporting bolts.
• Gates (also referred to as flaps) are connected to the shaft through the gate lever arm.
• Shafts are supported on two flange bearings mounted on the housing.
Summary of Contents for C Series
Page 16: ......