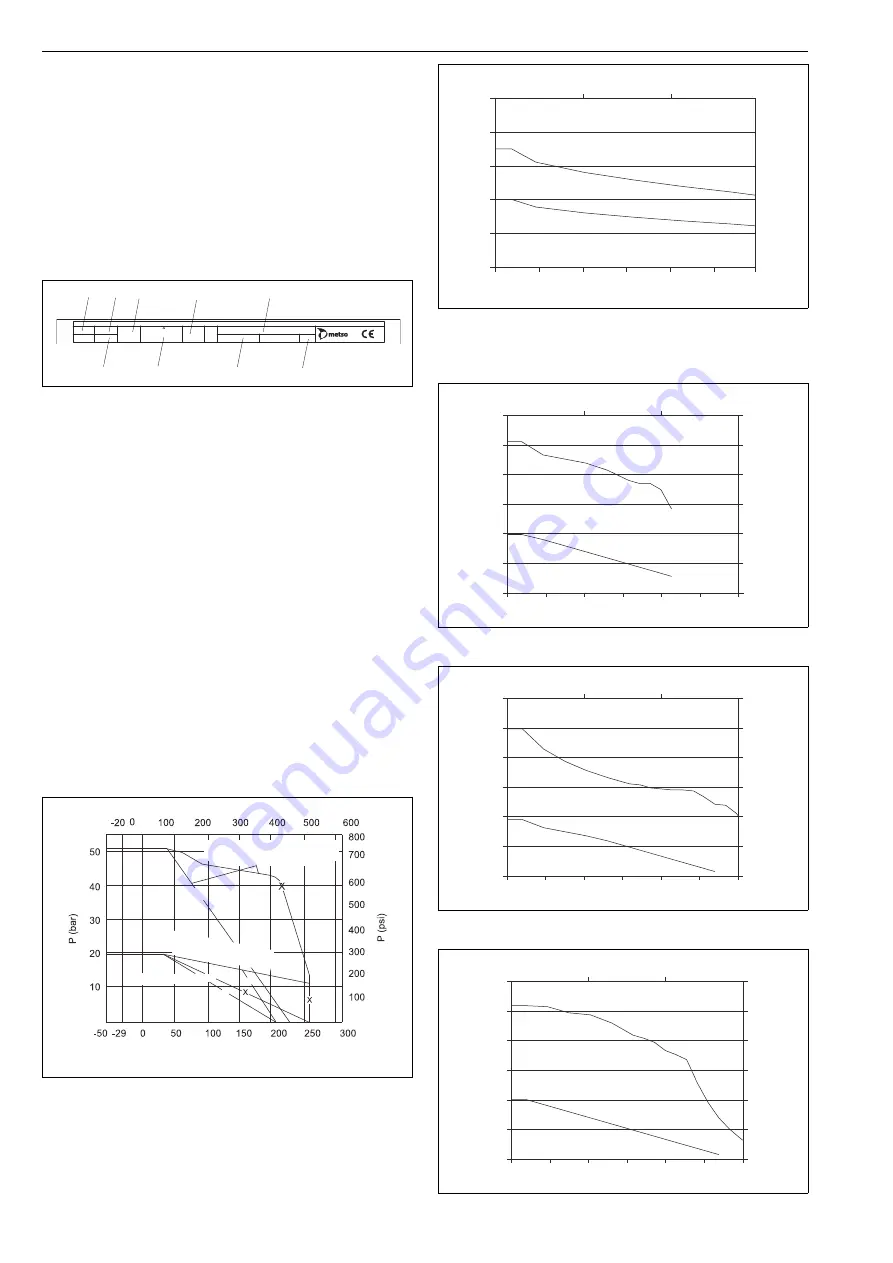
4
1 X 78 en
Identification plates have the following markings:
1.
Body material
2.
Shaft material
3.
Trim material
4.
Seat material
5.
Maximum and minimum operating temperatures
6.
Maximum shut-off pressure differential/temperature
7.
Pressure class
8.
Type code
9.
Number of the list of valve manufacturing parts
10.
Model
1.4
Technical specifications
Face-to-face length:
XT/XA:
ASME B.16.10
XB/XC:
ASME B.16.10 short pattern
Body rating:
ASME Class 150, 300
Max pressure differential:
see Figs. 6 and 7
Temperature range:
see Figs. 8, 9 and 10
Flow direction:
seats S, K, X and T:
free
Seats H and G:
see Figs. 1, 2 and 3
The arrow indicates the
recommended flow direction
Leakage rates:
metal seated
ISO 5208, leakage rate C
soft seated
ISO 5208, leakage rate A
Dimensions:
see Section 11
Weight:
see Section 11
Fig. 5
Identification plate
Fig. 6
Valve seat rating, soft seats
BODY
TRIM
SHAFT
SEAT
T max
T min
MAX. OPER. ps
at
RATING
TYPE
No.
MOD
ATTENTION : READ INSTRUCTIONS BEFORE INSTALLATION OR SERVICING. CONTACT METSO FIELD SYSTEMS FOR COPY.
MADE BY METSO AUTOMATION
XXXX
(1) (2)
(5)
(7)
(8)
(3) (4)
(6)
(9)
(10)
1" – 4" / DN 25 – 100, full bore
3" – 6" / DN 80 – 150, reduced bore
6" / DN 150, full bor
e
8" / DN 200, reduced bor
e
8" / DN 200, full bore
T*
T*
T*
T (°F)
T (°C)
T* = available only on request
Fig. 7
Maximum operational pressure differential, metal-
seated ASME Class 300 valves. Smaller sizes and ASME
Class 150 valves are full rated.
Fig. 8
Body pressure/temperature rating, WCB
Fig. 9
Body pressure/temperature rating, CF8M
Fig. 10
Body pressure/temperature rating, C5
50
750
600
450
300
150
0
40
30
20
10
0
100
T (°C)
P (psi)
°F)
(
T
P
(bar)
0
300
200
6" full bore
8" reduced bore
8" full bore
400
500
600
750
400
NOTE! All sizes withstand full design shut off pressure
(50 bar/750 psi) at ambient temperature
ASME 150
ASME 300
60
p (bar)
p (psi)
50
40
30
20
10
0
100
T (°C)
T (°F)
0
300
200
400
500
600
0
150
300
450
600
900
750
400
750
60
p (bar)
p (psi)
50
40
30
20
10
0
100
T (°C)
T (°F)
0
300
200
400
500
600
0
150
300
450
600
900
750
400
750
ASME 150
ASME 300
60
p (bar)
p (psi)
50
40
30
20
10
0
100
T (°C)
T (°F)
0
300
200
400
500
600
0
150
300
450
600
900
750
400
750
ASME 150
ASME 300
Summary of Contents for XB/XC Series
Page 23: ...1 X 78 en 23 ...