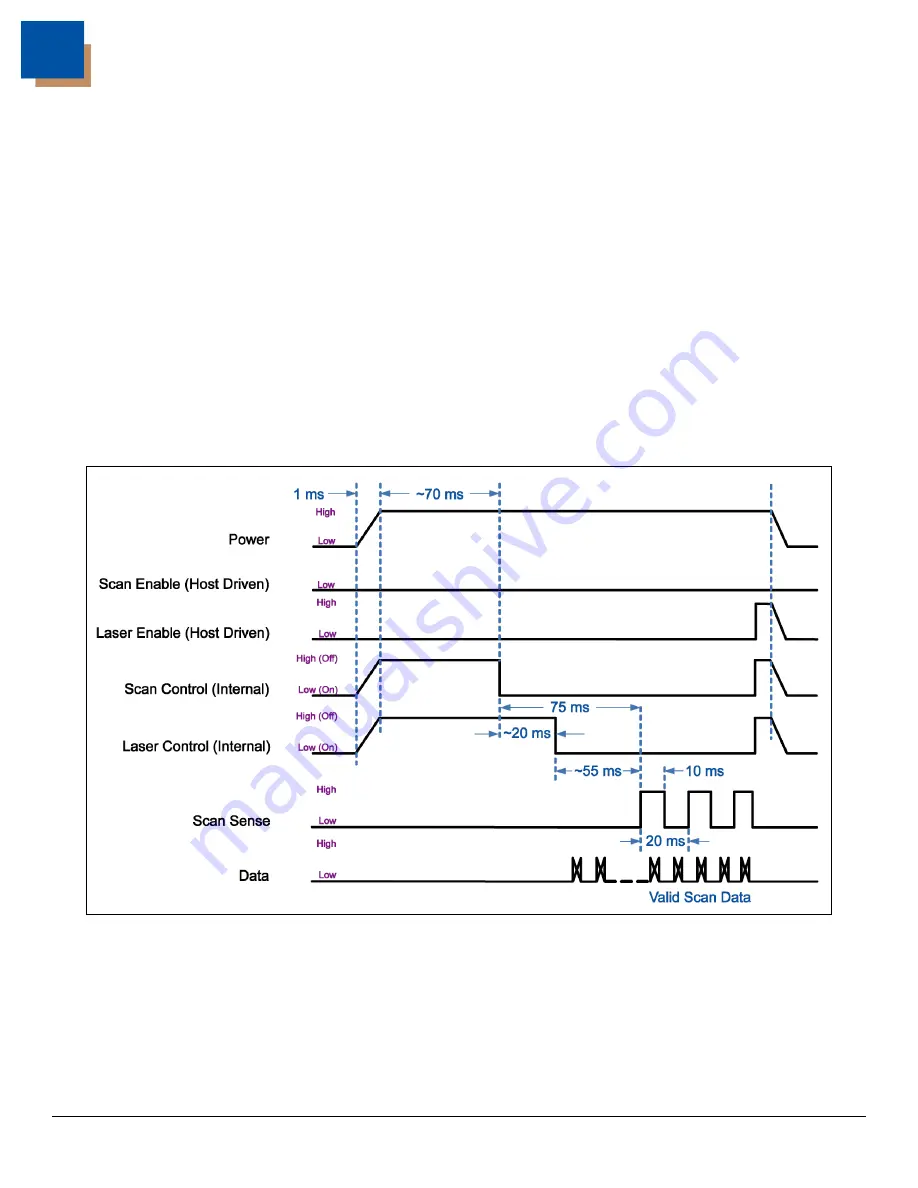
30
Timing Diagrams
Startup Condition Timing Diagram
The timing diagram below illustrates the correct power up procedure for the IS4813 and IS4815 engines.
Scan Enable and Laser Enable are host driven signals. The Scan Enable and Laser Enable signals should be
kept LOW (ON) at power up. Scan Control and Laser Control are engine driven signals.
The engine's onboard microcontroller drives the Scan Control and Laser Control signals so the engine's laser
will not turn ON before the scan mirror starts moving. This allows the onboard microcontroller to sense
immediately any malfunction with the engine's scan mirror, turning OFF the laser automatically regardless of
the state of Laser Enable signal being received from the Host.
To ensure scan data integrity the Scan Sense pulses are delayed for approximately 55 ms after the Laser
Enable signal goes LOW (ON). To save power, turn OFF power to the engine after the scan is complete or
when the engine is not scanning. To turn the engine's power OFF, the Laser Enable signal from the host
should be held HIGH (OFF) before turning OFF power to the engine.
Figure 22. IS4813/IS4815 Timing Diagram, Startup Condition