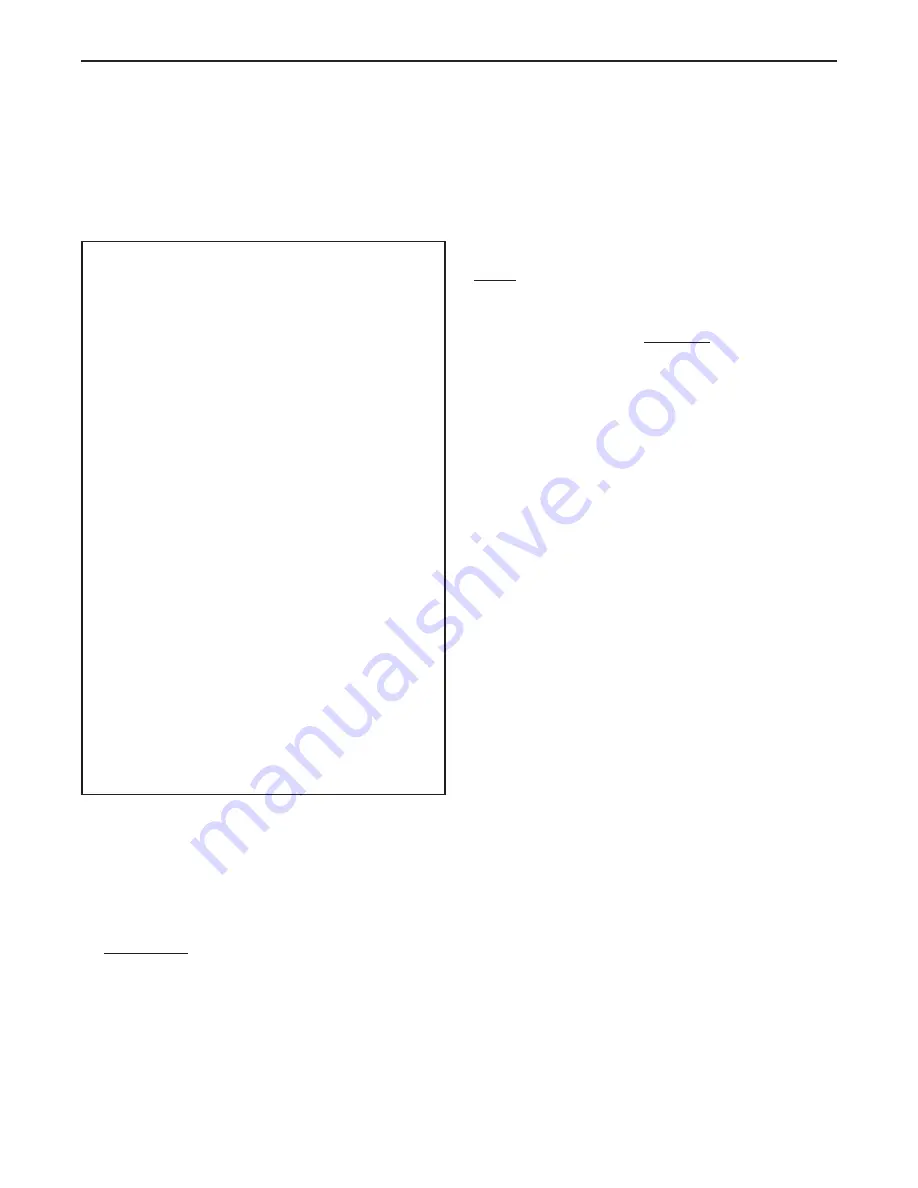
IMO-270EN
3
1
GENERAL
This instruction manual contains important information
regarding the installation, maintenance, and trou-
bleshooting of
Jamesbury
Series 7000 8" (DN 200) Class
150 Standard Bore, Series 9000 2" – 6" (DN 50 – 150) Class
150 and 2" – 4" (DN 50 – 100) Class 300 Full Bore Valves.
Please read the instructions carefully and save them for
future reference.
2
INSTALLATION
1. Place the valve in the open position.
2. Flow through a
Jamesbury
valve can be in either
direction. It is recommended, however, that the valve
be installed with the insert facing upstream.
3. IMPORTANT: Tighten the valve between flanges
using gaskets and fasteners appropriate for the serv-
ice and in compliance with applicable piping codes
and standards.
4. If there is weepage past the packing upon installation,
the valve may have been subjected to wide tempera-
ture variations in shipment. “Leak-tight” performance
will be restored by a packing adjustment described in
the MAINTENANCE Section.
3
MAINTENANCE
General maintenance requires periodic observation to ensure
that the valve is functioning well. Routine maintenance
consists of tightening the bonnet stud nuts (18) periodically
to compensate for stem seal wear. This may be done by
tightening the bonnet stud nuts (18) until snug, than tighten
an additional 1/4 turn.
3.1 Disassembly
NOTE: If complete disassembly becomes necessary,
replacement of all seats, packing and bearings is recom-
mended. (Refer to Service Kits, Table 2.)
1. Follow the steps in the WARNING Section before per-
forming any work on the valve.
2. Open and close the valve and leave in the closed posi-
tion.
3. Remove handle screw (35), handle (31), and retaining
ring (34) from the top of the stem.
4. Pull off the spring (33) and indicator stop (32).
5. Remove the bonnet stud nuts (18).
6. Remove stop bushings (50) and compression plate
(10).
7. Mark the body joint flanges to assure correct body (1)
and body cap (2) orientation during assembly. Remove
body stud nuts (16) and remove body cap (2). BE
CAREFUL NOT TO SCRATCH THE BALL.
8. Remove the body gasket (65) and the seat (7) from the
cap.
9. If the ball (3) does not swing free from the body, with
the ball in the fully closed position, use a piece of wood
or some other soft material to gently tap the ball (from
the end opposite the body cap). This should loosen the
ball so that it can be pivoted free of the stem (5).
10. Remove the second seat (7) from the body (1).
11. Press the stem (5) from the top into the valve body and
remove it through the end of the body.
12. Pry out from the inside the old thrust bearings (70),
secondary stem seal (71) and packing (69). BE CARE-
FUL NOT TO SCRATCH ANY SEALING SURFACES IN
THE BODY.
13. Remove the spring (36) from the bottom of the stem.
14. If the valve is to be grounded, clean packing bore with
crocus cloth or equivalent, to bare-metal surface.
1.1
Warning
FOR YOUR SAFETY AND PROTECTION, IT IS IMPORTANT THAT THE
FOLLOWING PRECAUTIONS BE TAKEN PRIOR TO REMOVING THE
VALVE FROM SERVICE OR BEFORE ANY DISASSEMBLY OF THE VALVE:
1.
AT ALL TIMES DURING THIS ENTIRE PROCEDURE, KEEP HANDS
OUT OF THE VALVE. A REMOTELY ACTUATED VALVE COULD CLOSE
AT ANY TIME AND RESULT IN SERIOUS INJURY.
2.
KNOW WHAT MEDIA IS IN THE LINE. IF THERE IS ANY DOUBT,
CHECK WITH THE PROPER AUTHORITY.
3.
WEAR ANY PROTECTIVE CLOTHING OR EQUIPMENT NORMALLY
REQUIRED WHEN WORKING WITH THE MEDIA INVOLVED.
4.
DEPRESSURIZE THE LINE AND VALVE AS FOLLOWS:
A.
OPEN THE VALVE AND DRAIN THE LINE.
B.
CLOSE AND OPEN THE VALVE TO RELIEVE ANY RESIDUAL
PRESSURE THAT MAY BE IN THE VALVE PRIOR TO REMOVING
THE VALVE FROM SERVICE. LEAVE THE VALVE IN THE OPEN
POSITION.
C.
AFTER REMOVAL AND PRIOR TO ANY DISASSEMBLY, DRAIN
ANY REMAINING MEDIA BY PLACING THE VALVE IN THE
VERTICAL POSITION AND CAREFULLY OPEN AND CLOSE THE
VALVE SEVERAL TIMES.
5.
SEAT AND BODY RATINGS – THE PRACTICAL AND SAFE USE OF
THIS PRODUCT IS DETERMINED BY BOTH THE SEAT AND BODY
RATINGS. READ THE NAME TAG AND CHECK BOTH RATINGS. THIS
PRODUCT IS AVAILABLE WITH A VARIETY OF SEAT MATERIALS.
SOME OF THE SEAT MATERIALS HAVE PRESSURE RATINGS THAT
ARE LESS THAN THE BODY RATINGS. ALL OF THE BODY AND SEAT
RATINGS ARE DEPENDENT ON VALVE TYPE AND SIZE, SEAT MATE-
RIAL, BOLTING MATERIAL, AND TEMPERATURE. DO NOT EXCEED
THESE RATINGS.