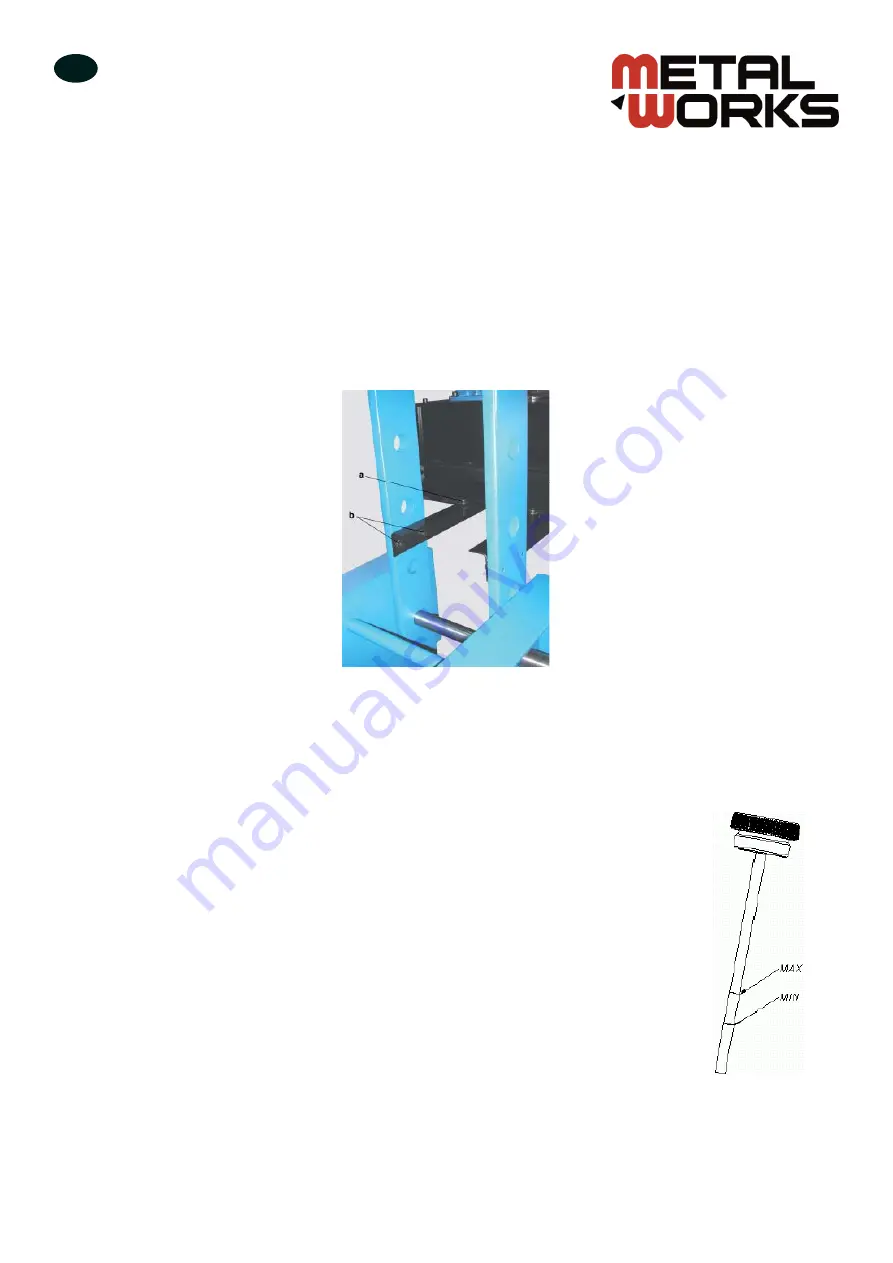
v1.0 22052012
9
GB
4 Before
fi
rst use
4.1 Mounting the oil tank
After placing the press in a suitable position, unscrew M10 bolts (a) and dismount the oil tank. Next, unscrew
the M10 bolts (b) from the two supporting brackets and move these brackets from the inner side to the outer
side of the machine frame. Re
fi
t the bolts and tighten them. Remove rubber stopper (60 T and 30 T only).
Remember to locate the brackets parallel to each other and perpendicular to the machine frame. Finally, mount
the oil tank on the brackets and tighten the four bolts (a).
Secure hydraulic hoses using two hose clamps on the upper lateral frame side.
4.2 Filling the oil tank
Remove the
fi
ller plug on the hydraulic tank cover. Pour in an appropriate volume of HL 46
or similar hydraulic oil that is unused and clean. It is important that the oil level reading
lies between the MIN and MAX marks. The
fi
lling operation must be performed when the
piston is in raised position. This corresponds to a proper position of the suction hose when
the piston is in its lowest position. Once the tank has been
fi
lled, replace the
fi
ller plug. A
drain plug is located at the bottom of the oil tank.
Take care to prevent dirt and water getting inside the oil tank.
copyrighted
document
- all
rights
reserved
by
FBC