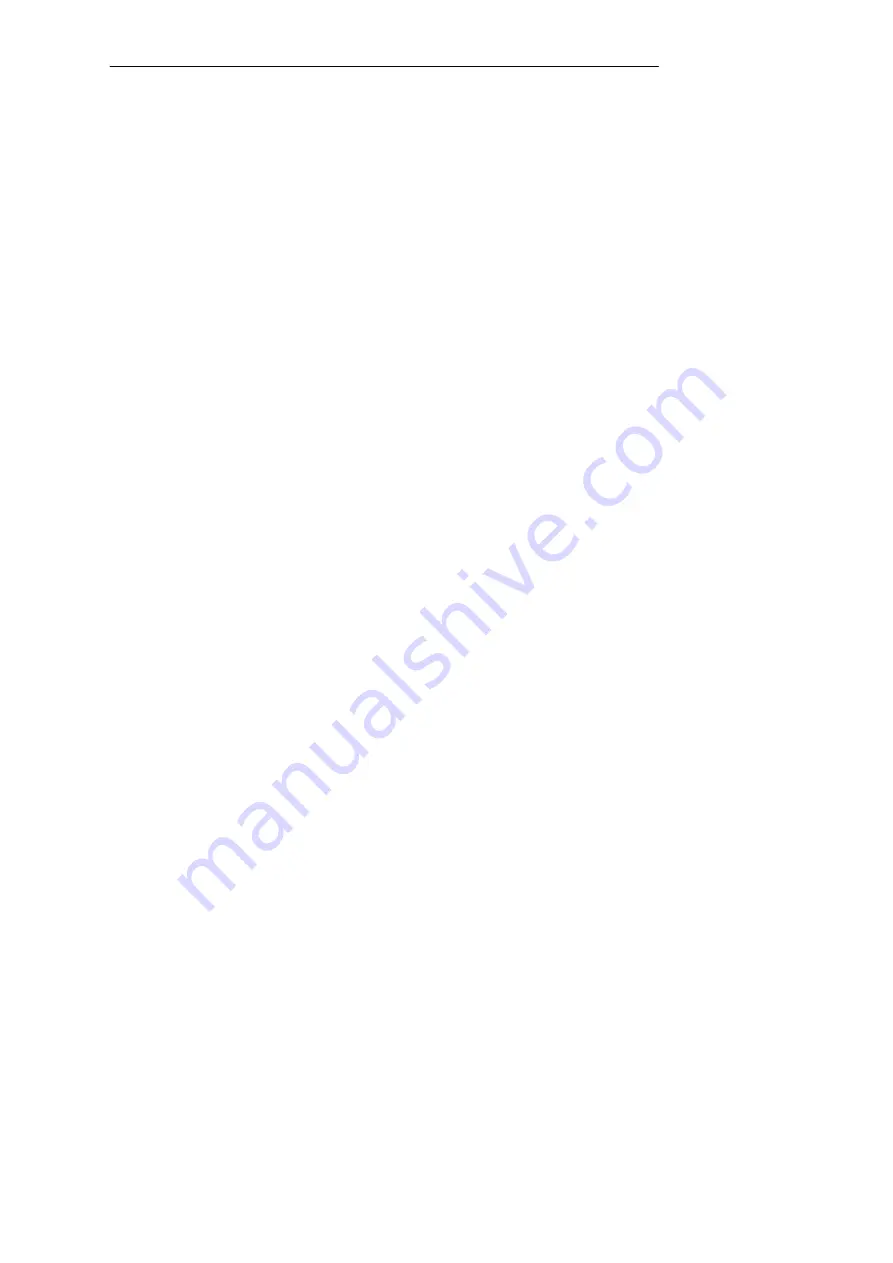
MESA Automation GmbH
MQC 05 V 3 EM
5
3.1 Subprint OPT E Limit switch
By connection of GND (OPT E -) or 24 V signal (OPT E +) to the terminals for negative and positive direction
the limit switch can be deactivated. If the limit switch is active, the motor will stop in these direction. The limit
switch logic level (OPT E += positive, OPT E (-)= negative logic) is set by factory. R 111 must be removed,
otherwise option B;C and E will not work.
3.2 Subprint MSM-OPT
Other Options are available by using MSM-OPT Subprint- please ask for more information.
- external current limiting, positive and negative Output current separate (Opt.A)
- Speed controlled current limiting (Opt. L)
- programmable Limit-Switch (Opt. KE)
- Ramp generator (Opt. B )
- Limit switch (Opt. C) only available with negative logic
4 POWER SUPPLY
4.1 Electronic supply
±±±±
15 V
Electronic (+/-15V) of the amplifier is supplied from power voltage.
4.2 Power transformer
Transformers with galvanic separated primary an secondary winding are used for adjustment of supply
voltage to the existing net. The Transformers have to correspond to VDE 0550. One and three phase
transformers can be used.
If the transformer used has a star point in its secondary winding then this should be isolated and NOT
connected to earth.
A three phase transformer is recommended for current higher than 10 A continuos overall.
The factory or your dealer should be consulted to specify the proper size and secondary voltage.
5 Setting up the amplifier
The adjustment of Tacho, output current, Irms is made by factory. An adjustment of an amplifier for another
motor is possible
In order to achieve best performance for the system motor/amplifier, optimisation of speed circuit is
necessary. The following components are used:
•
P 2 /R21:
P- Gain
•
C2:
I - Gain
•
P3/R31:
tachometer
signal
•
5.1 Tacho adjustment: P3
As a general rule, amplifiers driving servo motors are designed such that the continuously rated speed of the
motor corresponds to an input command to the amplifier of 10 V.
•
apply a 10 V signal to the command input and measure the motor speed. The Tacho pot. P3 can now be
adjusted until the correct maximum speed is reached. If unable to obtain the speed over range of P3, then
consult factory for modifications.
Standard-range:
Left side:
5 V Tacho input voltage correspond to 10 V Set value
Right side:
60 V Tacho input voltage correspond to 10 V Set value
adjustment of the standard range with R31
Components can be adjusted in factory or by service.
5.2 Offset: P1
If an input of exactly 0 V is applied to the command input then the motor shaft should be stationary. Any
creep may be eliminated with P 1.
Summary of Contents for MQC 0506
Page 1: ...PWM SERVO CONTROLLERS SERIES MQC Operating Manual Issue September 05...
Page 6: ...MESA Automation GmbH MQC 05 V 3 EM 4 3 Block diagram...
Page 16: ...MESA Automation GmbH MQC 05 V 3 EM 14 10 3 Components location...
Page 17: ...MESA Automation GmbH MQC 05 V 3 EM 15 10 4 Mechanical style...