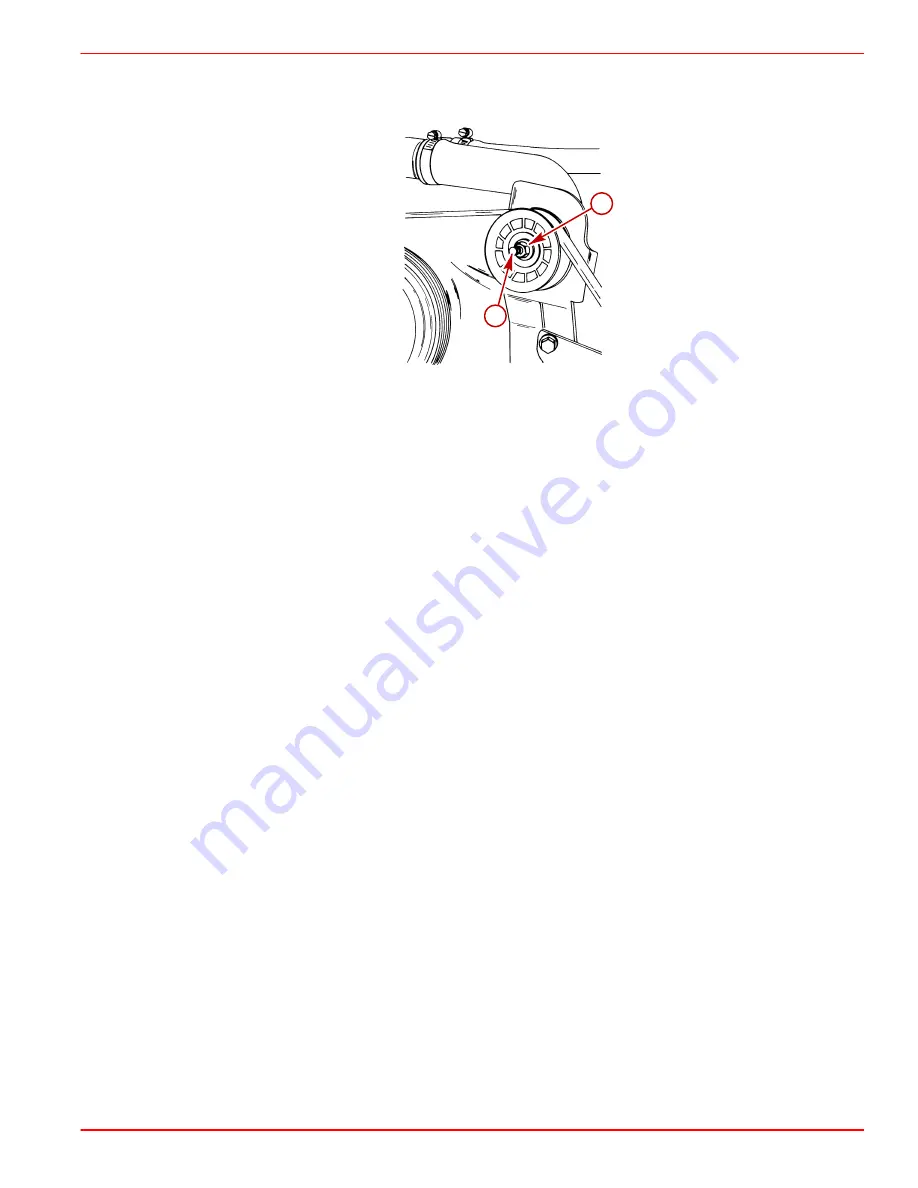
MAINTENANCE
SERVICE MANUAL NUMBER 25
90-861328--1 NOVEMBER 1999
Page 1B-27
7. While holding adjustment stud at the correct belt tension, tighten 5/8 in. locking nut.
8. Run engine for a short period of time and recheck belt adjustment.
74908
a
b
a -
5/8 in. Locking Nut
b -
5/16 in. Adjusting Stud
Ignition Timing
Thunderbolt V Models
1. Connect timing light to number 1 spark plug wire.
2. Connect a shop tachometer to the engine.
IMPORTANT: Before starting the engine, connect a jumper wire from the ignition tim-
ing lead to a good ground. This has to be done before the ignition key is turned ON
to lock the ignition module into Base Timing Mode.
3. Before starting the engine, connect jumper wire from timing lead to a good ground.
NOTE: The PUR/WHT timing lead is located towards the front of the engine near the fuel
line or near the distributor, as equipped for your model.
4. Start engine and run at 1300 rpm until it reaches normal operating temperature.
5. Disconnect throttle cable from the carburetor.
6. With engine at idle rpm, adjust the carburetor idle rpm screw to the specified engine idle
rpm.
7. With the engine still at idle rpm, check the ignition timing. If incorrect, rotate the
distributor until timing is correct. Torque clamping screw to 18 lb-ft (25 Nm).
8. Adjust the idle mixture screw. Inward is LEAN, outward is RICH.
9. Recheck ignition timing.
10. Stop engine. Remove timing light, jumper wire and shop tachometer.
IMPORTANT: Timing jumper wire has to be removed or the ignition module will stay
locked in the Base Timing Mode and it will not be able to advance the ignition timing
correctly when the engine rpm is increased.
11. Adjust and reinstall throttle cable. Open and close remote control throttle lever. Ensure
that the carburetor throttle lever is contacting the idle rpm adjusting screw every time.
12. Restart the engine, increase rpm to 1300 then return to idle position slowly and shut the
engine off. Ensure that the carburetor throttle lever is contacting the idle rpm screw.
13. Shut engine off.