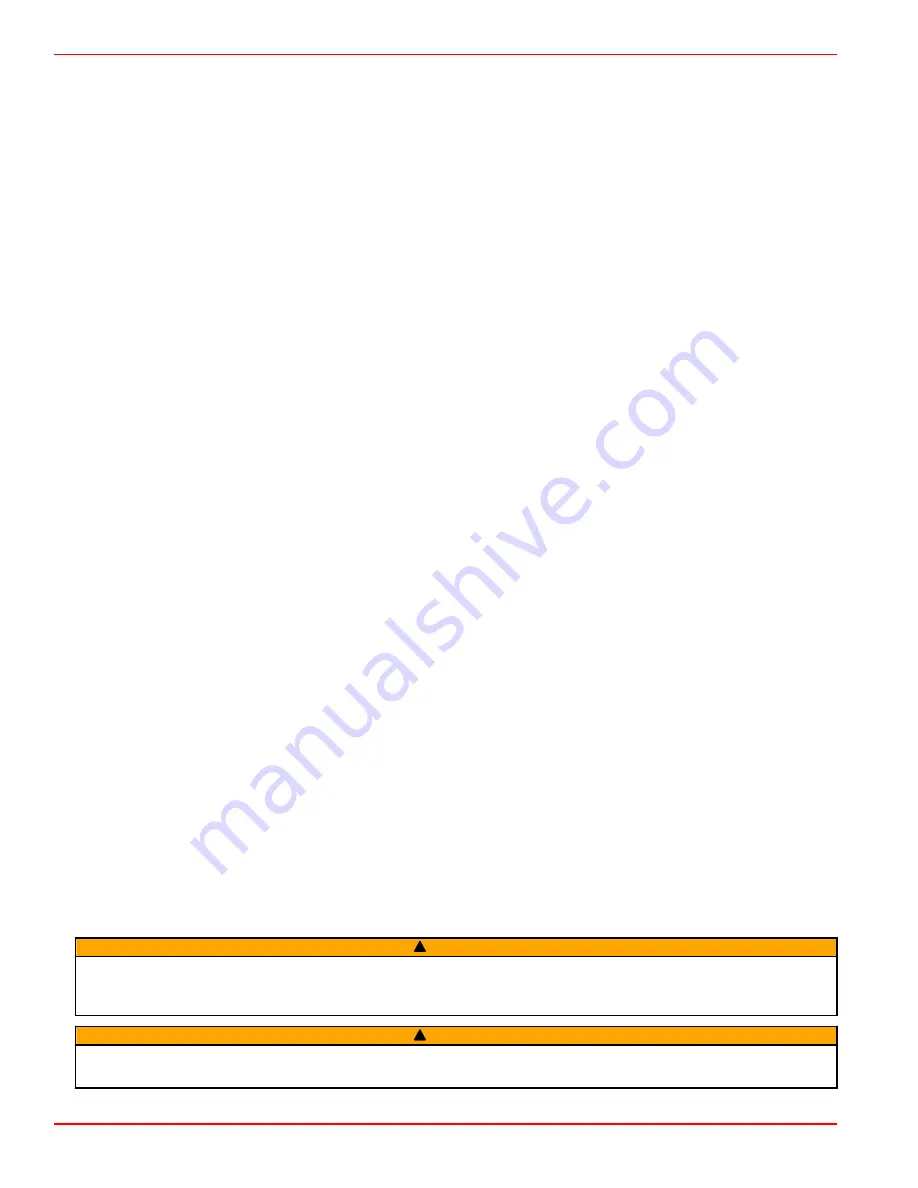
Section 4 - Maintenance
Page 32
90-8M0133679
eng
JUNE 2017
Owner and Operator Responsibilities
It is the operator's responsibility to perform all safety checks, to ensure that all lubrication and maintenance instructions are
complied with for safe operation, and to return the unit to a Mercury Diesel authorized repair facility for a periodic checkup.
Normal maintenance service and replacement parts are the responsibility of the owner or operator and, as such, are not
considered defects in workmanship or material within the terms of the warranty. Individual operating habits and usage
contribute to the need for maintenance service.
Proper maintenance and care of your power package will ensure optimum performance and dependability and will keep your
overall operating expenses at a minimum. See your Mercury Diesel authorized repair facility for service aids.
Dealer Responsibilities
It is the dealer's responsibility to provide predelivery inspection and preparation:
•
Before delivery, making certain that the Mercury power package is in proper operating condition.
•
Making all necessary adjustments for maximum efficiency.
•
Explaining and demonstrating the operation of the power package and the boat.
•
Providing a copy of the Predelivery Inspection Checklist.
•
Completing the warranty registration and immediately submitting it to Mercury Marine via MercNET, e‑mail, or mail. All
power packages must be registered for warranty purposes.
Cleaning Care Recommendation
Do Not Use Caustic Cleaning Chemicals
IMPORTANT: Do not use caustic cleaning chemicals on any part of the MerCruiser power package. Some cleaning products
contain strong caustic agents. For example, some hull cleaners contain hydrochloric acid. These cleaners can degrade some of
the components they contact, including critical steering fasteners.
Damage to steering fasteners may not be obvious during visual inspection, and this damage may lead to catastrophic failure.
Some caustic cleaning chemicals may cause or accelerate corrosion. Exercise caution when using cleaning chemicals around
the power package, and follow the recommendations on the packaging of the cleaning product.
Cleaning Gauges
IMPORTANT: Never use high‑pressure water to clean gauges.
Routine cleaning of the gauges is recommended to prevent a buildup of salt and other environmental debris. Crystalized salt
can scratch the gauge display lens when using a dry or damp cloth. Ensure that the cloth has a sufficient amount of fresh water
to dissolve and remove salt or mineral deposits. Do not apply aggressive pressure on the display lens while cleaning.
When water marks cannot be removed with a damp cloth, mix a 50/50 solution of warm water and isopropyl alcohol to clean the
display lens.
Do not use
acetone, mineral spirits, turpentine type solvents, or ammonia based cleaning products. The use of
strong solvents or detergents may damage the coating, the plastics, or the rubber keys on the gauges. If the gauge has a sun
cover available, it is recommended that the cover be installed when the unit is not in use to prevent UV damage to the plastic
bezels and rubber keys.
Cleaning Remote Controls
IMPORTANT: Never use high‑pressure water to clean remote controls.
Routine cleaning of the remote control external surfaces is recommended to prevent a buildup of salt and other environmental
debris. Use a cloth towel which has a sufficient amount of fresh water to dissolve and remove salt or mineral deposits.
When water marks cannot be removed with a damp cloth, mix a 50/50 solution of warm water and isopropyl alcohol to clean the
remote control.
Do not use
acetone, mineral spirits, turpentine type solvents, or ammonia based cleaning products. The use of
strong solvents or detergents may damage the coating, the plastics, or the rubber components on the remote control.
Maintenance
!
WARNING
Performing service or maintenance without first disconnecting the battery can cause product damage, personal injury, or
death due to fire, explosion, electrical shock, or unexpected engine starting. Always disconnect the battery cables from the
battery before maintaining, servicing, installing, or removing engine or drive components.
!
WARNING
Fuel vapors trapped in the engine compartment may be an irritant, cause difficulty breathing, or may ignite resulting in a fire
or explosion. Always ventilate the engine compartment before servicing the power package.
Summary of Contents for MerCruiser Diesel Inboard 2.8L
Page 1: ...2 8L and 4 2L Diesel Inboard Models OPERATION MAINTENANCE MANUAL ...
Page 2: ......
Page 8: ...Page iv 90 8M0133679 eng JUNE 2017 ...
Page 20: ...Section 1 Getting to Know Your Power Package Notes Page 12 90 8M0133679 eng JUNE 2017 ...
Page 38: ...Section 3 Specifications Notes Page 30 90 8M0133679 eng JUNE 2017 ...
Page 92: ......