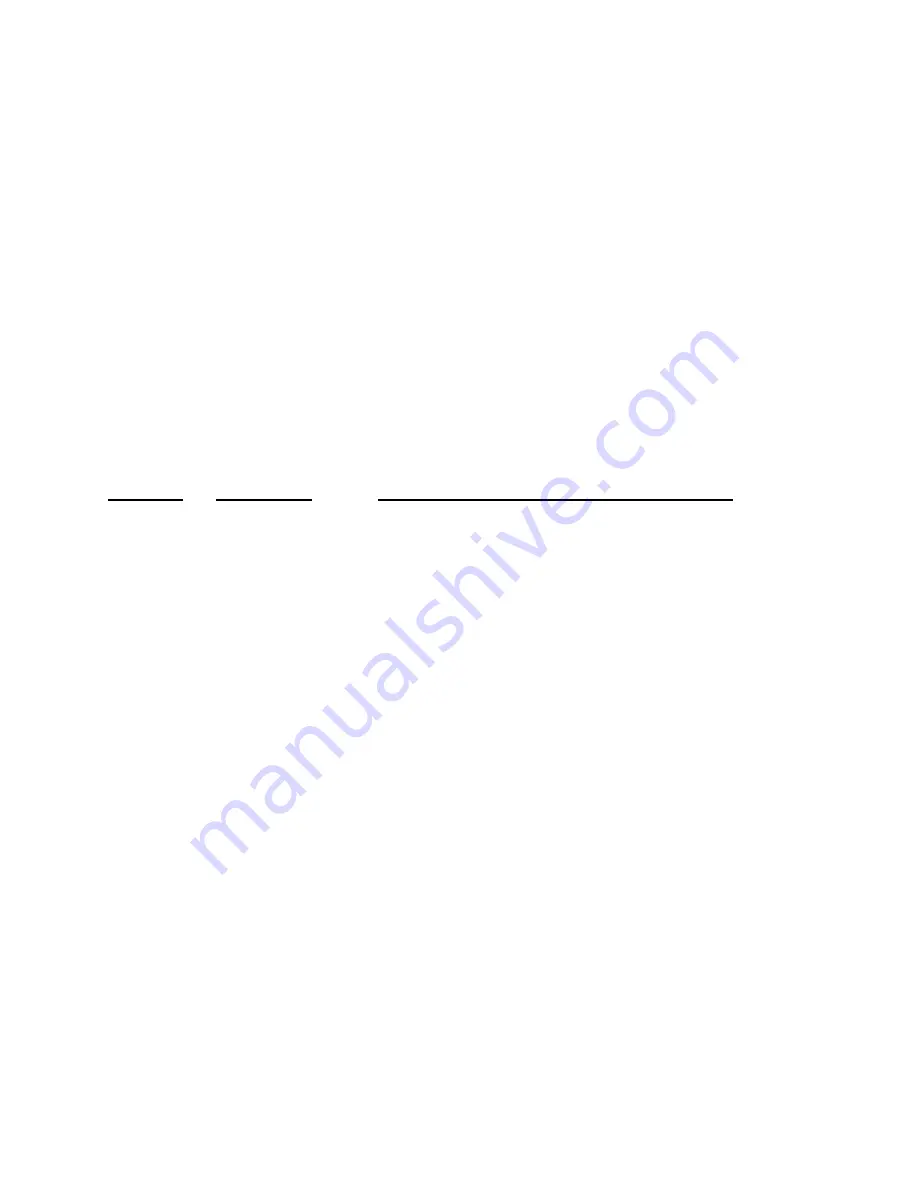
18
COMPUTER:
The bottling machine computer program is designed to perform the bottling process based on
certain events taking place in a certain fashion. Items of primary concern to the computer are the
detection of filled bottles and proper bottle pressures. When the computer detects a pressure or
fill problem it performs a predetermined response to identify the problem and stop the machine
safely. When the machine experiences no or low counter pressure, or it takes in excess of 40
seconds to fill a row of bottles, the machine performs a safe shut down routine. This means any
items which make pressure are shut off and the Snift valve opens to relieve pressure from the
bottles. During a safe shut down the filling heads will remain in the down position until the
machine is reset, at which time the fill heads will return to the up position. It should also be
noted that any time the machine is changed from running a program to a paused condition the
computer performs the safe shut down routine.
The following is a list of outputs to the computer. Pressure sensors are analog and do not show
on this list. Outputs are listed from left to right; the first module is 0-17 (12-17 are not used).
OUTPUT
FUNCTION
TUBING SIZE AND COLOR ON MACHINE
0
Speed valve
5/32” Yellow
1
Snift valve
5/32” Orange
2
CO
2
valve
5/32” Blue
3
CO
2
pulse
5/32” Red
4
Cap drop
1/4” Green
5
Bottle index
1/4” Blue
6
Fill head
1/4” Gray
7
Fill valve
1/4” Yellow
10
Crowner
3/8” Red
11
Educator
5/32” Natural
12
Tank Head space CO2 Valve mounted to right side of control panel
Product sensor
5/32” Natural
Bottle sensor
5/32” Blue
Temperature RTD, located in product manifold, uses wire connection.
The following are descriptions of possible problems with the pressure or fill detection and the
resulting actions by the computer. This section should be very useful for determining which
parameters need to be adjusted and for troubleshooting the machine when a part failure is
suspected. The description of the problem is given, then a possible resolution to the problem is
suggested.
1) Fill detection is not set sensitive enough to trip, indicating to the computer that the bottles are
not full. The machine starts normally by indexing bottles, indexing caps into the capping
head, capping head puts caps on bottles, the fill head stays down, and the fill valve remains
open until the computer times out (about 40 seconds). When time out occurs, the computer
performs a safe shut down and displays the “Filling Time Out” message.
Corrective Action:
Increase the sensitivity of the fill detector by decreasing its numeric value.