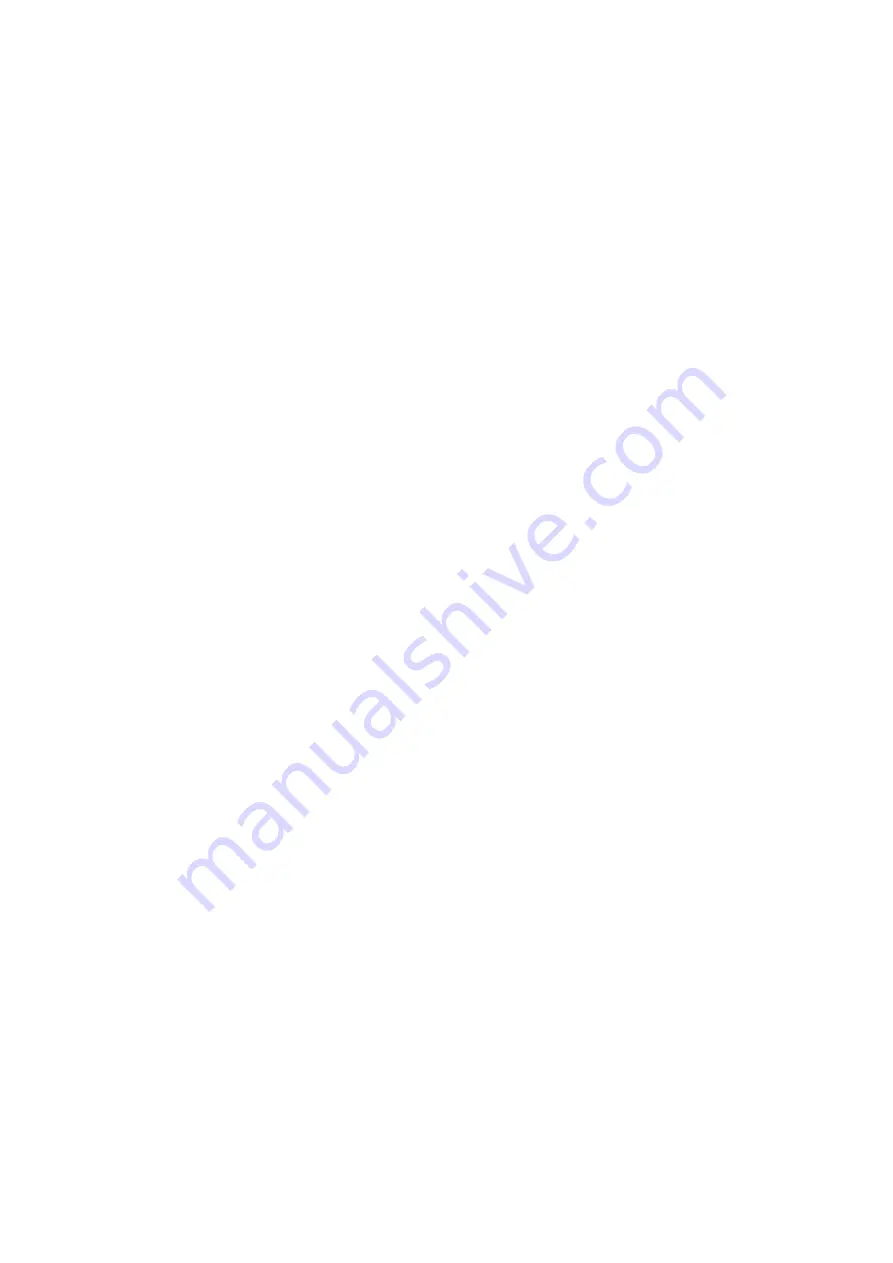
9
.
Your
wet
plate
can
now
be
placed
in
your
etching
machine,
which
should
use
Ferric
Chloride
Solution
with
a
S.G.
of
1.38
‐
1.42
for
ferrous
metals
and
a
S.G.
of
1.3
–
1.34
for
non
‐
ferrous
metals
(N.B.
Non
‐
ferrous
metals
can
also
be
etched
in
the
higher
S.G
ferric
without
any
problems).
Also
please
ensure
that
the
S.G
of
the
solution
does
not
exceed
1.45,
if
this
happens
dilute
it
down
to
1.42
with
water.
To
check
the
S.G.
use
our
hydrometer
set
(Mega
Part
No:
500
‐
174
‐
11)
In
Spray
Etchers
always
run
the
pump
for
3
‐
4
minutes
before
doing
checks
for
both
S.G.
and
acidity
(see
below)
It
is
also
important
to
keep
the
acidity
of
the
solution.
This
can
be
checked
from
time
to
time
by
taking
5
‐
10ml
of
solution
and
adding
it
to
50
times
the
amount
of
water
in
a
clear
jug
or
beaker.
The
ferric
should
look
a
clear
to
green
colour,
however
if
it
appears
to
be
cloudy
with
particles
floating
in
it
then
add
1%
by
volume
36%
Hydrochloric
Acid.
MOST
IMPORTANT:
PLEASE
ENSURE
THAT
IF
YOU
NEED
TO
DO
MORE
THAN
ONE
PASS
THROUGH
THE
ETCHING
CHAMBER,
DO
NOT
RINSE
IT
BETWEEN
PASSES
AS
THIS
CAUSES
THE
DRY
FILM
TO
SHRINK
AND
STEPS
IN
THE
ETCHING.
As
a
general
point
–
Fresh
etchant
will
etch
stainless
steel
at
about
12
microns
a
minute
and
brass
and
copper
at
about
30
microns
a
minute.
Obviously
this
will
slow
down
as
the
etchant
becomes
more
saturated
with
metal.
Normally
when
the
etch
time
is
double
the
time
to
get
the
same
depth,
you
need
to
replace
the
etchant.
For
the
disposal
of
spent
chemicals,
please
contact:
Richard
Spreadbury
of
J&G
Environmental
Ltd.
Telephone:
07970
204845/
email:
sales@jg
‐
environmental.com
and
let
them
know
that
you
are
our
customer.
10
.
Remove
the
plate
from
the
etching
machine
and
wash.
11.
STRIPPING
Using
our
stripper,
diluted
4
parts
water
with
1
part
stripper,
place
the
plate
in
the
stripper
either
in
a
tray,
dip
tank
or
spray
process
and
leave
until
all
the
dry
film
resist
has
been
removed.
If
the
stripper
is
heated
to
45°C
it
will
work
much
more
quickly.
12.
Remove
the
plate
from
the
stripper
and
then
wash
and
dry
it.
Your
plate
is
now
ready
to
be
filled,
cut
etc.
DRY
FILM
STORAGE
CONDITIONS
Store
between
15°C
–
20°C
with
a
relative
humidity
of
40
‐
60%
Page 14