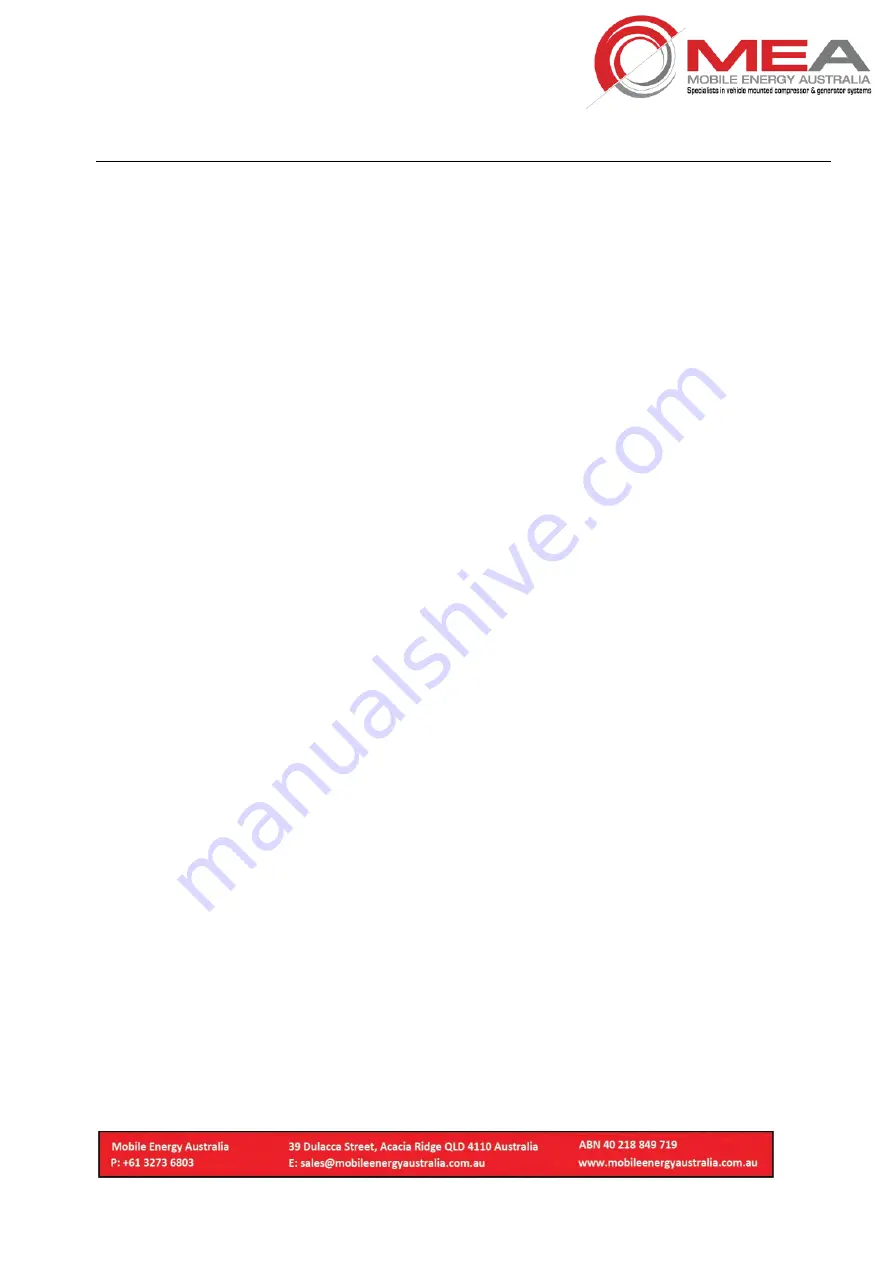
Document No 7209-D0002-01
18
INSTALLATION - continued
2.1
It is best to test the installation at the hottest expected ambient temperature.
2.2
Setup and run the system at 120 PSI. This can be done by installing a ball valve on the air
outlet pipe and adjusting the opening of the valve so that the compressor is running continuously at 120
PSI.
2.3
Record the engine, compressor, and current ambient temperature for future reference.
2.4
Run the system at full load for at least one hour or until the temperatures stabilizes.
Temperature stabilizing means there is no rise in temperature for 15 minutes when the compressor is
running at the rated load.
2.5
Record the engine and compressor temperatures every 10 minutes.
2.6
If the system over-heats, the ventilation is not sufficient, review the installation, make changes
as needed, and repeat the test.
3
Engine Exhaust consideration when installing Diesel Engine Driven Compressor Unit
In cases that the exhaust system needs to be ducted away from the engine assembly, the following are
a minimum that should be considered.
▪
The exhaust pipe needs to be adequate for the engine.
▪
There needs to be a flexible joint at the point where the extension is connected to the exhaust
system of the Diesel Engine Driven Compressor Unit.
▪
Ensure the exhaust pipe has suitable clearance and does not meet anything.
▪
Ensure that if the exhaust system has a method to prevent water from entering the exhaust
system.
▪
Ensure exhaust from the diesel engine is routed in a way to prevent recirculation back into the
unit.
4.
Securing the Diesel Engine Driven Compressor Unit to the body of the vehicle.
It is important to consider maintenance needs, (daily needs), service requirements, electrical
connections, air connections, location of control panel before the SMAC is secured to the body of the
vehicle.
▪
Locate a suitable mounting position for SMAC. Place the unit and check for clearances to any
other objects.
▪
There are four weld nuts located at the four corners of the bottom formed plate which can be
used as mounting bolt locations. Holes can also be drilled through the bottom of the formed
plate if alternate locations are required.
▪
Drill four holes in mounting surface and secure the SMAC to the truck. Use a minimum of 4
–
M12 bolts.
Summary of Contents for SMAC 35DWG 22HP
Page 2: ...Document No 7209 D0002 01 2 THIS PAGE IS LEFT BLANK INTENTIONALLY...
Page 25: ...Document No 7209 D0002 01 25 8 TROUBLESHOOTING...
Page 26: ...Document No 7209 D0002 01 26 TROUBLESHOOTING continued...
Page 27: ...Document No 7209 D0002 01 27 9 DRAWINGS ILLUSTRATIONS...
Page 28: ...Document No 7209 D0002 01 28 DRAWINGS ILLUSTRATIONS Parts list...
Page 29: ...Document No 7209 D0002 01 29 DRAWINGS ILLUSTRATIONS Parts list...
Page 30: ...Document No 7209 D0002 01 30 DRAWINGS ILLUSTRATIONS Parts list...
Page 31: ...Document No 7209 D0002 01 31 DRAWINGS ILLUSTRATIONS HYDRAULIC PNEUMATIC DIAGRAM...
Page 32: ...Document No 7209 D0002 01 32 DRAWINGS ILLUSTRATIONS SMAC WIRING DIAGRAM...
Page 33: ...Document No 7209 D0002 01 33 DRAWINGS ILLUSTRATIONS SMAC WIRING DIAGRAM MINE SPEC...
Page 34: ...Document No 7209 D0002 01 34 DRAWINGS ILLUSTRATIONS...
Page 35: ...Document No 7209 D0002 01 35 DRAWINGS ILLUSTRATIONS VRD Control Box...
Page 37: ...Document No 7209 D0002 01 37 DRAWINGS ILLUSTRATIONS 3 Phase Outlet Box Diagram...
Page 38: ...Document No 7209 D0002 01 38 DRAWINGS ILLUSTRATIONS...