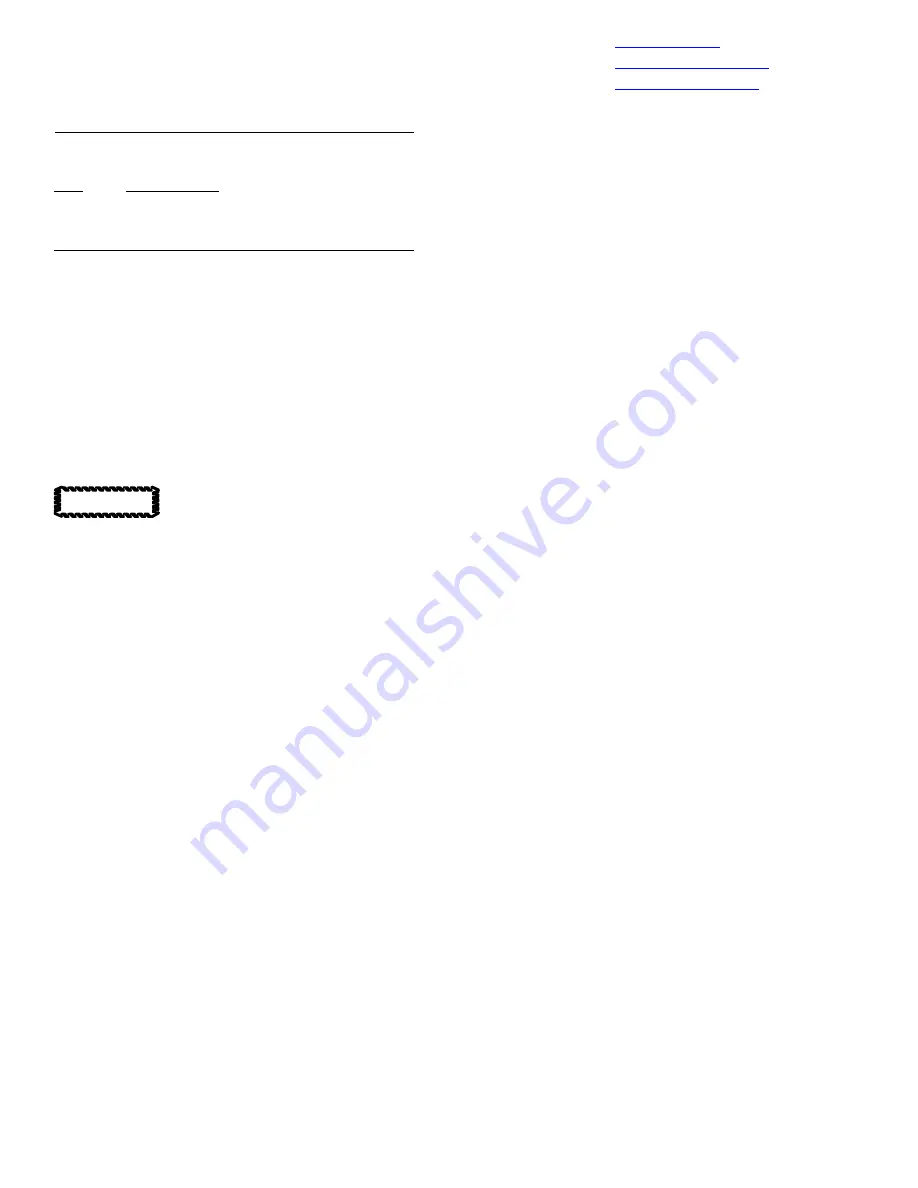
CSP-HMI-3
MD Helicopters, Inc
.
MAINTENANCE MANUAL
Page 212
TR16-001
96-10-00
The information disclosed herein is proprietary to MD Helicopters, Inc.
Neither this document nor any part hereof may be reproduced or transferred to
other documents or used or disclosed to others for manufacturing or any other
purpose except as specifically authorized in writing by MD Helicopters, Inc.
Copyright
©
1999
−
2016 by MD Helicopters, Inc.
B. Starter/Generator Installation
Consumable Materials
(Ref. Section 91
−
00
−
00)
Item
Nomenclature
Grease, aircraft
Solvent, dry-cleaning
(1). Ensure that all electrical power is OFF.
(2). Remove protective cover from opening
in engine.
(3). Install mounting flange with four nuts
and washers. Torque nuts to
100 - 140
inch-pounds (11.29 - 15.81 Nm)
.
(4). Using a bottle brush and solvent
(CM234), clean the starter shaft and
mating engine splines.
Before installation, check condi
tion of seal in accessory drive
gearbox. For wet-splined starter/genera
tors, also insure integrity of packing on
starter/generator drive shaft.
(5). Lubricate starter/generator drive shaft
NOTE:
.Grease (CM111) dry spline starter/gen
erator drive shaft splines only.
(a). Install starter/generator with
V-clamp. Torque clamp nut to
50
inch-pounds (5.64 Nm)
.
(b). Tap around clamp with a rawhide
mallet to seat clamp on flange.
Retorque clamp nut to
50 inch-
pounds (5.64 Nm)
.
(c). Continue tapping around clamp and
retorquing clamp nut until nut no
longer turns when specified torque is
applied.
(6). Install electrical leads to properly
identified locations. Install and tighten
nuts and remove identifying tags.
11. Starter/Generator Inspection
(Ref. Figure 204) Before inspecting starter/
generator, remove lubricant from splines of
drive shaft. Clean vibration dampener. Remove
brush cover and fan cover. Clean brush dust
out of unit.
NOTE:
This inspection does not supersede nor
replace inspections required by manufactur
er of starter/generator (Ref. Sec. 01-00-00).
A. Starter/Generator
−
Exterior Inspection
NOTE:
Replacement of damper clutch or back
plate is required if it does not meet following
requirements.
(1). Ensure damper clutch exerts pressure
against dampener backplate; Weak
spring on clutch or gap between these
parts is not allowed.
(2). Inspect damper clutch for cracks,
warpage, loose rivets and excessive
wear on spring surface mating with
damper backplate; Minimum spring
thickness if 0.015 inch (0.381 mm).
(3). Inspect damper backplate for cracks
and bronze friction facing for wear;
Minimum facing thickness if 0.010 inch
(0.254 mm).
(4). Check splines on drive shaft for wear.
(5). Check fan for looseness on hub and for
cracked or bent condition.
(6). Inspect terminal block for cracks,
breaks, loose or damaged terminal
studs, and loose electrical connections.
(7). Inspect starter/generator housing for
any signs of damage, and inlet and
outlet blower screens for clogging.
(8). Inspect mounting clamp and mounting
flange attaching hardware for security.
B. Starter/Generator
−
Interior Inspection
(1). Inspect commutator for pitting, scoring
or burned areas.
(2). Check brushes for cracks, chips, frayed
leads and loose shunt connections.
Ensure brush leads lay over brush
spring clips. Replace brushes if remain
ing allowable wear is suspected before
next scheduled inspection (Ref.
Figure 205).
(3). Check brush holder and end bell for
cracks and warpage.
CAUTION
Summary of Contents for 369-500
Page 14: ......
Page 30: ......
Page 82: ......
Page 94: ......
Page 106: ......
Page 116: ......
Page 134: ......
Page 150: ......
Page 162: ......
Page 168: ......
Page 178: ......
Page 226: ......
Page 232: ......
Page 244: ......
Page 346: ......
Page 416: ......
Page 444: ......
Page 458: ......
Page 472: ......
Page 490: ......
Page 536: ......
Page 560: ......
Page 578: ......
Page 604: ......
Page 612: ......
Page 616: ......
Page 628: ......
Page 654: ......
Page 678: ......
Page 706: ......