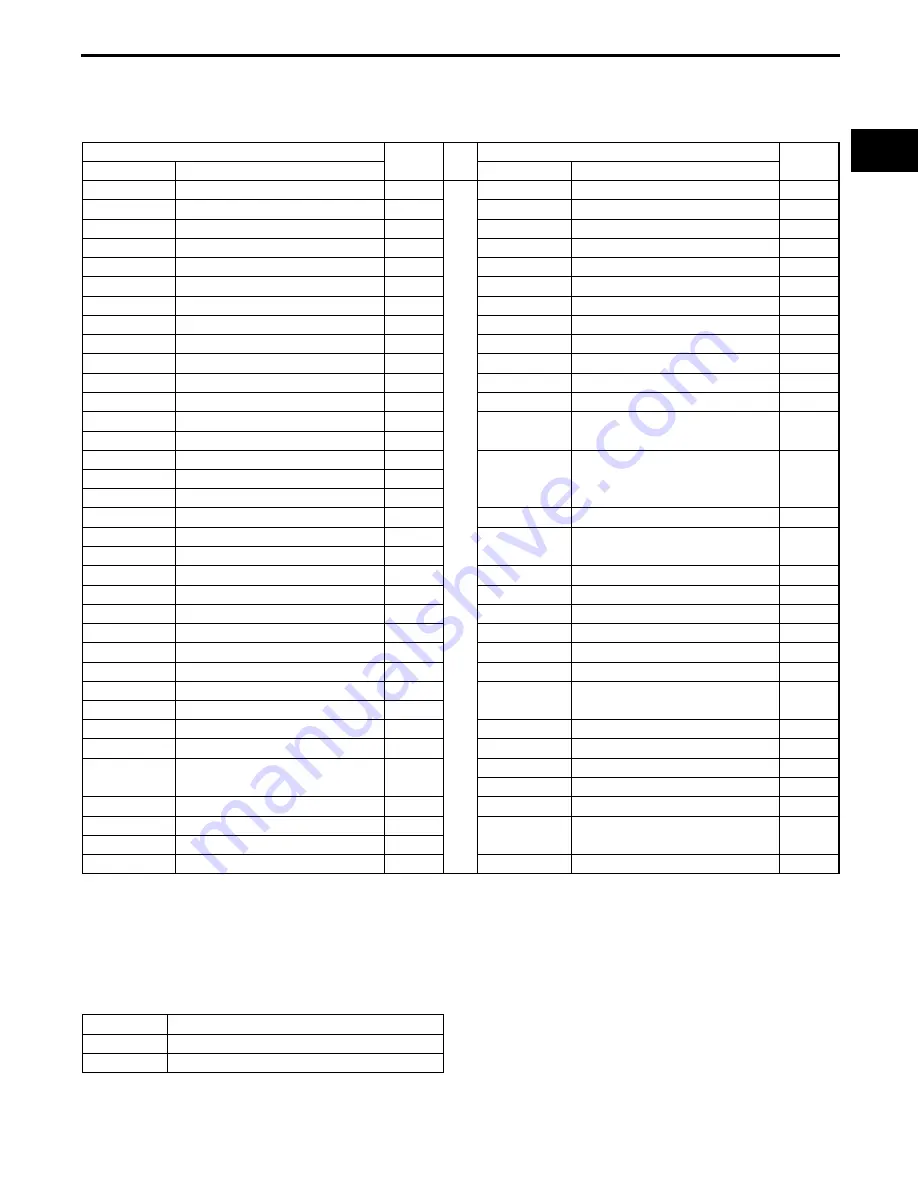
GENERAL INFORMATION
00–00–11
00–00
Engine Workshop Manual 13B-MSP (Multi Side Port) (1773–1U–03C)
SAE STANDARDS
CHU000000003E02
•
In accordance with new regulations, SAE (Society of Automotive Engineers) standard names and abbreviations
are now used in this manual. The table below lists the names and abbreviations that have been used in Mazda
manuals up to now and their SAE equivalents.
#1 : Diagnostic trouble codes depend on the diagnostic test mode.
#2 : Controlled by the PCM
#3 : Device that controls engine and powertrain
#4 : Directly connected to exhaust manifold
End Of Sie
ABBREVIATIONS
CHU000000011E01
End Of Sie
SAE Standard
Remark
SAE Standard
Remark
Abbreviation
Name
Abbreviation
Name
AP
Accelerator Pedal
MAP
Manifold Absolute Pressure
APP
Accelerator Pedal Position
MAF
Mass Air Flow
ACL
Air Cleaner
MAF sensor
Mass Air Flow Sensor
A/C
Air Conditioning
MFL
Multiport Fuel Injection
A/F
Air Fuel Ratio
OBD
On-board Diagnostic System
BARO
Barometric Pressure
OL
Open Loop
B+
Battery Positive Voltage
OC
Oxidation Catalytic Converter
CMP sensor
Camshaft Position Sensor
O2S
Oxygen Sensor
LOAD
Calculated Load Value
PNP
Park/Neutral Position
CAC
Charge Air Cooler
PID
Parameter Identification
CLS
Closed Loop System
PSP
Power Steering Pressure
CTP
Closed Throttle Position
PCM
Powertrain Control Module
#3
CPP
Clutch Pedal Position
PAIR
Pulsed Secondary Air Injection
Pulsed
injection
CIS
Continuous Fuel Injection System
CKP sensor
Crankshaft Position Sensor
AIR
Secondary Air Injection
Injection
with air
pump
DLC
Data Link Connector
DTM
Diagnostic Test Mode
#1
DTC
Diagnostic Test Code(s)
SAPV
Secondary Air Pulse Valve
DI
Distributor Ignition
SFI
Sequential Multiport Fuel
Injection
DLI
Distributorless Ignition
EI
Electronic Ignition
#2
3GR
Third Gear
ECT
Engine Coolant Temperature
TWC
Three Way Catalytic Converter
EM
Engine Modification
TB
Throttle Body
EVAP
Evaporative Emission
TP
Throttle Position
EGR
Exhaust Gas Recirculation
TP sensor
Throttle Position Sensor
FC
Fan Control
TCC
Torque Converter Clutch
FF
Flexible Fuel
TCM
Transmission (Transaxle) Control
Module
4GR
Fourth Gear
GEN
Generator
TR
Transmission (Transaxle) Range
GND
Ground
TC
Turbocharger
HO2S
Heated Oxygen Sensor
With
heater
VSS
Vehicle Speed Sensor
VR
Voltage Regulator
IAC
Idle Air Control
VAF sensor
Volume Air Flow Sensor
IAT
Intake Air Temperature
WU-TWC
Warm Up Three Way Catalytic
Converter
#4
KS
Knock Sensor
MIL
Malfunction Indicator Lamp
WOP
Wide Open Throttle
AT
Automatic Transmission
MT
Manual Transmission
SST
Special Service Tool
Summary of Contents for 13B-MSP
Page 71: ......