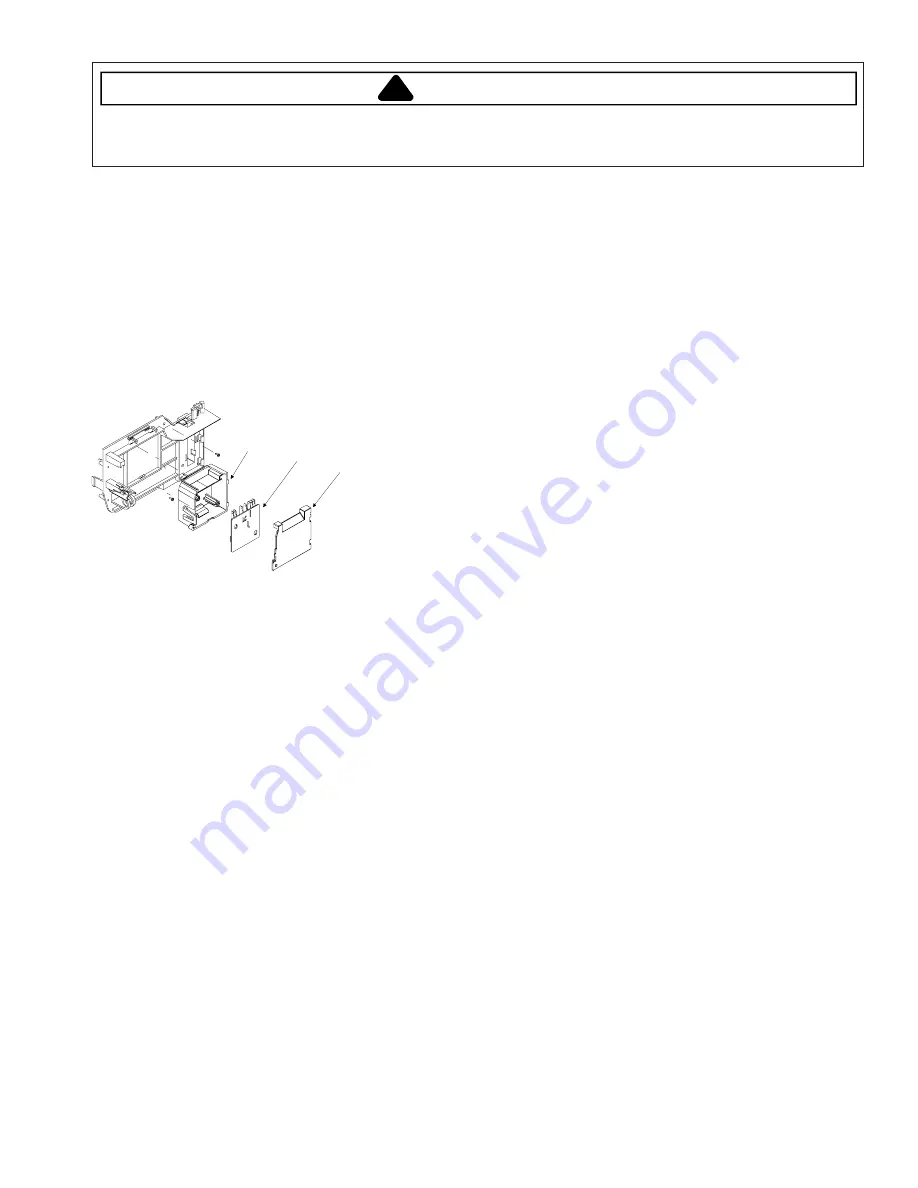
Disassembly Procedures
!
WARNING
To avoid risk of electrical shock, personal injury, or death, disconnect electrical power source to unit, unless test
procedures require power to be connected. Discharge capacitor through a resistor before attempting to service.
Ensure all ground wires are connected before certifying unit as repaired and/or operational.
©2005 Maytag Services
16025628
31
Adaptive Defrost Control (ADC) (some models)
1. Remove cold control and fresh food control knobs.
2. Remove screw just between knobs and on right side
of control cover.
3. Remove cover by pulling cover to the right and forward
off liner.
4. Release front left tab to remove ADC cover.
5. Remove ADC board from locating tabs.
6. Disconnect harness from ADC board.
7. Reverse procedure to reassemble.
ADC BOARD
ADC HOUSING
ADC COVER
ADC CONTROL HOUSING
Damper Control (some models)
1. Remove cold control and fresh food control knobs.
2. Remove screw just between knobs and on right side
of control cover.
3. Remove cover by pulling cover to the right and
forward off tabs.
4. Slide off styrafoam block. Retain for future use.
5. Pull shaft extension free of control.
NOTE: Observe wide and narrow clip leg orientation of
shaft and damper cover.
6. Release side tabs holding damper control to
assembly.
7. Lift damper control off of assembly
NOTE: Retain damper gasket for future use.
8. Reverse procedure to reassemble.
Electronically Controled Damper
1. Remove damper cover by removing hex head screw
and lifting off of damper.
2. Remove foam insert by pulling it off of damper control.
3. Depress two clips that hold front of damper in place to
release damper from assembly, lift damper out.
4. Disconnect wires from damper and remove damper.
5. Reverse procedure to reassemble.
Fresh Food Thermistor
1. Remove damper cover by removing hex head screw to
expose thermistor.
2. Unclip thermistor from assembly.
3. Cut wires at thermistor to remove.
Water Filter Assembly (some models)
1. Remove filter cover opening cover and pulling rear left
side of cover to the left to release cover from holding
pin.
2. Filter head can be released from holding bracket by
opening tabs on left side filter head and pulling
downward and to your left to release filter head.
3. Tubing needs to be disconnected from water valves
in the machine compartment. (see water valve
removal)
4. After tubing is loose from water valves pull the filter
head and tubing out the front of unit.
5. Reverse procedure to reassemble.
NOTE: Make sure to note tubing end colors when
reinstalling new head and tubing assembly.
Water Tank Assembly (some models)
1. Remove crisper drawers from fresh food compartment.
2. Remove hex screw holding water tank to rear
bulkhead.
3. On rear of cabinent remove hex screws holding water
valve cover plate.
4. Remove plate and tubing away from cabinet to expose
water valves and tubing.
5. Disconnect water tube from secondary valve coming
from water tank, remove compression nut from tubing.
6. On front of unit remove toe grill and disconnect water
coupler going to water dispenser
7. Remove compression nut from water tubing on cabinet
side of connection.
8. From rear of cabinet pull water tube out of conduit
going to dispenser.
9. From inside of fresh food compartment pull tubing up
and out of cabinet to complete removal of water tank.
10. Reverse procedure to reassemble.
Crisper Light Cover and Socket
1. Push down and forward on light cover and lift off tabs.
2. Remove light bulb and pry socket with taped putty
knife to release socket from liner.
3. Disconnect wires from socket.
4. Reverse procedure to reassemble.
Freezer Compartment
Freezer Light socket
1. Remove auger ice bucket.
2. Remove auger motor assembly. (see auger motor
assembly removal.
3. Remove light bulbs.
4. Disconnect wiring from light sockets.
5. Squeeze retaining tab to release sockets
6. Reverse procedure to reassemble.