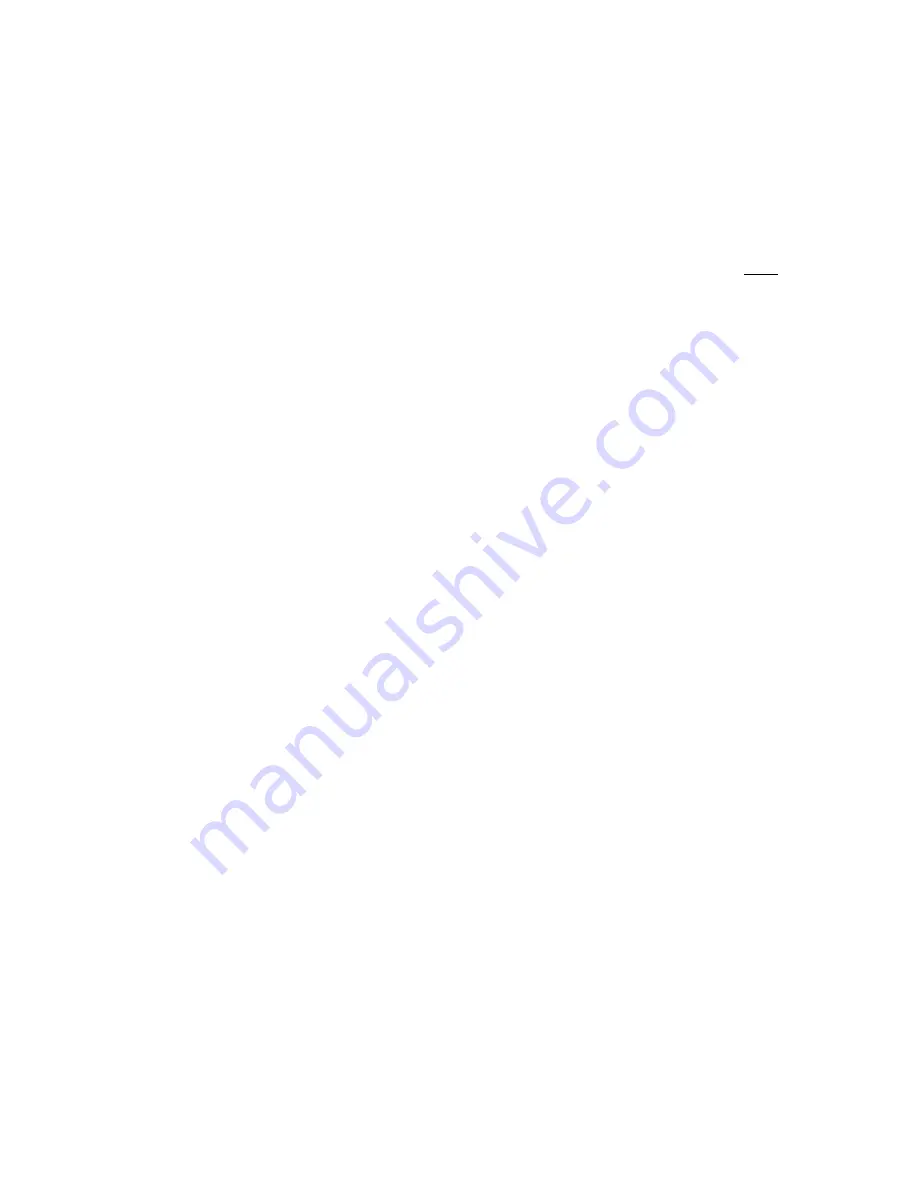
33
THE DATA LABEL
1.
MODEL NUMBER
The model number is a number, which describes the size of the dryer and the type of heat (i.e. gas).
2.
SERIAL NUMBER
The serial number allows the
Maytag Company
to gather information on your particular dryer.
3.
MANUFACTURING CODE NUMBER
The manufacturing code number is a number issued by the manufacturer which describes
ALL
possible
options on your particular model.
4.
TYPE OF HEAT
This describes the type of heat for your particular dryer: gas (either natural gas or liquid propane [L.P.]) or
steam.
5.
HEAT INPUT
(for GAS DRYERS)
This describes the heat input in British Thermal Units per Hour (BTUH).
6.
ORIFICE SIZE
(for GAS DRYERS)
Gives the number drill size used.
7.
ELECTRIC SERVICE
This describes the electric service for your particular model.
8.
MINIMUM GAS SUPPLY PRESSURE
Pressures shown are the range allowable for proper and safe operation.
9.
GAS MANIFOLD PRESSURE
(for GAS DRYERS)
This describes the manifold pressure taken at the gas valve tap in inches of water column.
10.
This section is for Canadian installation as noted.
11.
APPLICABLE APPROVAL SEALS
Canadian Standards Association International.