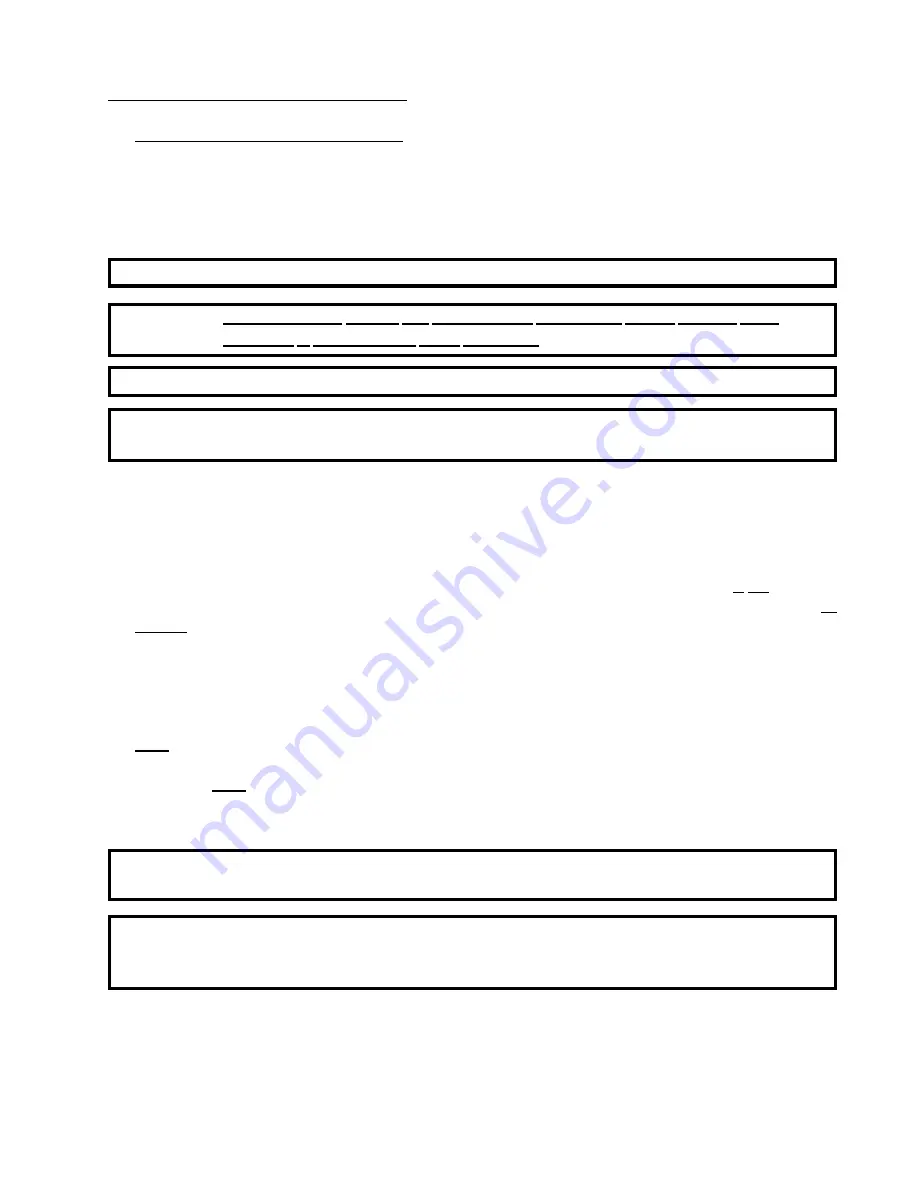
15
E. EXHAUST REQUIREMENTS
1. General Exhaust Duct Work Information
Exhaust duct work
should be
designed and installed by a qualified professional. Improperly sized duct work
will create excessive back pressure which results in slow drying, increased use of energy, overheating of the
dryer, and shutdown of the burner by the airflow (sail) switches, burner hi-limits, or tumbler (basket) hi-heat
thermostats.
CAUTION
: DRYER
MUST BE
EXHAUSTED TO THE OUTDOORS.
CAUTION
:
IMPROPERLY
SIZED
OR
INSTALLED
EXHAUST
DUCT
WORK
CAN
CREATE
A
POTENTIAL
FIRE
HAZARD.
NOTE
: When a dryer is exhausted separately, it is recommended that a back draft damper be installed.
NOTE
: When dryers are exhausted into a multiple (common) exhaust line, each dryer
must be
supplied
with a back draft damper.
The exhaust duct work
should be
laid out in such a way that the duct work travels as directly as possible to
the outdoors with as few turns as possible. Single or independent dryer venting is recommended.
When single dryer venting is used, the duct work from the dryer to the outside exhaust outlet
should not
exceed
twenty (20) feet. In the case of multiple (common) dryer venting, the distance from the last dryer to
the outside exhaust outlet
should not exceed
twenty (20) feet. The shape of the duct work is not critical so
long as the minimum cross section area is provided. It is suggested that the use of 90º turns in ducting be
avoided; use 30º and/or 45º angles instead. The radius of the elbows
should preferably be
1-1/2 times the
diameter of the duct. Excluding basket/dryer elbow connections or elbows used for outside protection from
the weather, no more than two (2) elbows
should be
used in the exhaust duct run. If more than two (2)
elbows are used, the cross section area of the duct work
must be
increased in proportion to number of
elbows added.
ALL
duct work
should be
smooth inside with no projections from sheet metal screws or other obstructions
which will collect lint. When adding ducts, the ducts to be added should overlap the duct to which it is
connected.
ALL
duct work joints
must be
taped to prevent moisture and lint from escaping into the building.
Additionally, inspection doors
should be
installed at strategic points in the exhaust duct work for periodic
inspection and clean-out of lint from the duct work.
IMPORTANT
: Exhaust back pressure measured by a manometer at the dryer exhaust duct area
must
not exceed
0.3 inches of water column.
NOTE
: Where the exhaust duct work passes through a wall, ceiling, or roof made of combustible
materials, the opening
must be
2-inches larger (all the way around) than the duct. The duct
must be
centered within this opening.
Summary of Contents for MD-170
Page 24: ...20...