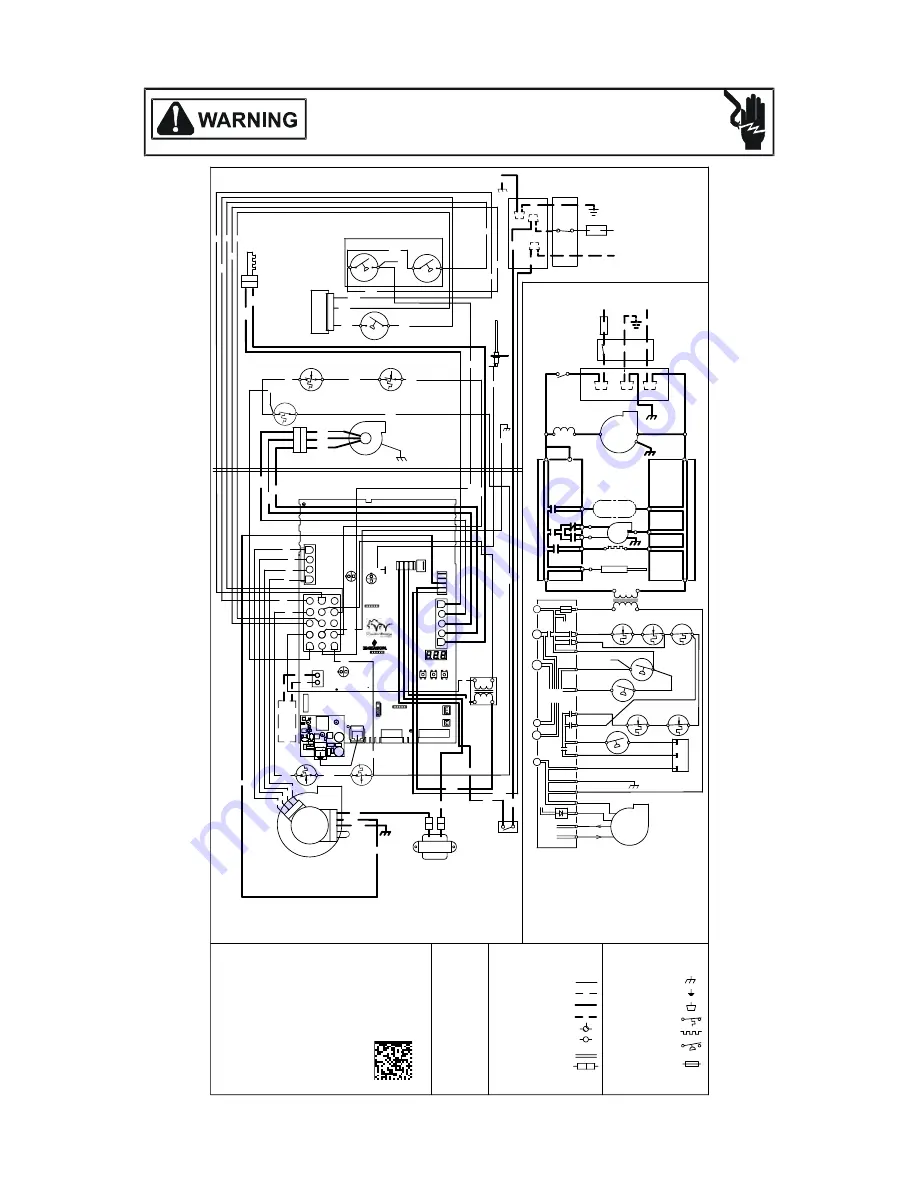
54
w
IrIng
D
IagraMs
Wiring is subject to change. Always refer to the wiring diagram on the unit for the most up-to-date wiring.
HIGH VOLTAGE!
D
ISCONNECT
ALL
POWER
BEFORE
SERVICING
OR
INSTALLING
THIS
UNIT
.
M
ULTIPLE
POWER
SOURCES
MAY
BE
PRESENT
. F
AILURE
TO
DO
SO
MAY
CAUSE
PROPERTY
DAMAGE
,
PERSONAL
INJURY
OR
DEATH
.
0140F02453-A
FRONT COVER
PRESSURE SWITCH
NO
C
FUSE 3 A
MICRO
TO
PS2 (12)
TR (11)
G
HI
C
TH (4)
24V THERM
OSTAT CON
NECTIONS
VALVE
GAS
TRANSFORMER
HLI (1)
Y
HLO (10)
GND (5)
MVL (13)
NO
W
C
R
CONTROLS
AUTO RESET AUXILIARY LIMIT
LIMIT CONTROLS
MANUAL RESET ROLLOUT
PRESS. SWITCH
HIGH FIRE
C
PSO (7)
SWITCH
LOW FIRE PRESS.
MVH (14)
DEHUM
GND
PS1 (2)
LIMIT CONTROL
AUTO RESET PRIMARY
24 VAC
NO
PM
MVC (8)
INTEGRATED CONTROL MODULE
C
BLWR
AIR
INDOOR
CIRCULATOR
TX (3)
RX (2)
+ VDC (1)
GND (4)
R
TO
MICRO
TO
TO +VDC
EAC
ID
NEUTRAL
WIRING TO UNIT
L
INTEGRATE
D CONTROL
MODULE
HOT SURFACE
INDUCTOR COIL
GND
BLWR
NEUTRAL
WARNING:
GROUNDED.
OVERCURRENT PROTECTION DEVICE
MUST BE PROPERLY
SWITCH
NEUTRAL
ELECTRONIC
AIR
(ON SOME MODELS)
IGN
IND HI
DISCONNECT
FS
POLARIZED AND
LINE
NEUTRAL
JUNCTION BOX
BLWR
IND LO
N
INDOOR
AIR CLEANER
DOOR
NEUTRAL
INTEGRATE
D CONTROL
MODULE
TO 115VAC/ 1
Ø /60 HZ POWER SUPPLY WITH
115 VAC
IGNITER
CIRCULATOR
BEFORE SERVICING.
FLAME SENSOR
DISCONNECT POWER
LINE
GND
OR
BR
BK
WH
WH
PU
GY
YL
OR
BR
PK
RD
WH
BK
GY
GN
OR
RD
BK
GY
BL
NO
2
1. SET HEAT ANTICIPATOR ON ROOM THERMOSTAT AT 0.7 AMPS.
PK
WARNING:DISCONNECT
TRANSFOR
MER
40 V
A
PU
GY
N
NO
3
BR
4. UNIT MUST BE PERMANENTLY GROUNDED AND CONFORM TO N.E.C. AND LOCAL CODES.
COLOR CODES:
1
SWITCH
PRESSURE
LOW FIRE
SENSOR
FLAME
GN GREEN
GR
PRESSURE SWITCH
FRONT COVER
C
VAC
TO UNIT MUST BE
1
BL
RD
AND GROUNDED.
1
115
WH
SWITCH (PRESS.)
FIELD SPLICE
FIELD GND
LOW VOLTAGE FIELD
GN
BL
BR
WH
NO
LIMIT CONTROL
AUTO RESET PRIMARY
WH
1
OR
RD RED
GY GRAY
40 kBTU)
CONTROLS (SINGLE CONTROL ON
MANUAL RESET ROLLOUT LIMIT
WH
L
PU
NOTES:
GY
PK
BK
5
SWITCH ASSEMBLY
ID BLOWER TWO-STAGE PRESSURE
OR
WH
SERVICING. WIRING
EQUIPMENT GND
(ON SOME MODELS)
INTERNAL TO
SWITCH
PRESSURE
HIGH FIRE
PROT. DEVICE
INTEGRATED CONTROL
PK
C. USE COPPER CONDUCTORS ONLY.
$
AT LEAST 105
IT MUST BE REPLACED WITH WIRING MATERIAL HAVING A TEMPERATURE RATING OF
3. IF ANY OF THE ORIGINAL WIRE AS SUPPLIED WITH THE FURNACE MUST BE REPLACED,
PU
PLUG CONNECTION
2
4
BK
C
DOOR OPEN)
(OPEN WHEN
DOOR SWITCH
COMPARTMENT
BLOWER
SWITCH (TEMP.)
GND
BLOWER
CIRCULATOR
PU PURPLE
JUNCTION
OR
40 VA
PK PINK
Ø /60 HZ
DISCONNECT
(WHITE-RODGERS)
GAS VALVE
TWO STAGE
2. MANUFACTURER'S SPECIFIED REPLACEMENT PARTS MUST BE USED WHEN SERVICING.
OVERCURRENT
HI VOLTAGE (115V)
CONNECTOR
2 CIRCUIT
LOW VOLTAGE (24V)
YL
GND
VAC
CHASSIS GROUND
2
3
4
IGNITER
SURFACE
HOT
2
GND
BK BLACK
YL
PU
C
INDUCTOR COIL
BL BLUE
C
BLOWER
DRAFT
INDUCED
WH WHITE
PM
BK
24
115 VAC/ 1
OVERCURRENT
BK
BR BROWN
YL YELLOW
3
HI VOLTAGE FIELD
OR ORANGE
HI
TERMINAL
OR
POWER BEFORE
IGNITER
RD
BK
TO
POWER SUPPLY WITH
BURNER COMPARTMENT
PROTECTION DEVICE
PROPERLY POLARIZED
WH
BK
JUNCTION BO
X
GN
GND
GND
PU
BL
HLI (3)
HLI (6)
10
6
3
13
4
5
2
7
14
11
15
1
12
8
9
FUSE 3A
CENTER
RIGHT
LEFT
C
RAT
GND
GND
SAT
IGN
IND-HI
IND-LO
IND-N
IGN-N
LI
NE
NEUT
RA
L
DE
Y
G
W
C
R
R
1
2
NA
HUM
CONDEN -SAT
E
EC
M
6
1
6
1
6
1
FS
EAC
1
2
4
2
3
1
3
5
1
4
BL
BK
RD
GY
BK
BL
PU
IN
OUT
CONDENSAT
E
SW
ITCH
(OPTIONA
L)
LIMIT
CONTROL
AUXILIARY
AUTO RESET
BLOWER COMPARTMENT
HARNESS
ECM MTR
BLUETOOTH
BOARD
OPT. HUM.
BR
OPT. HUM.