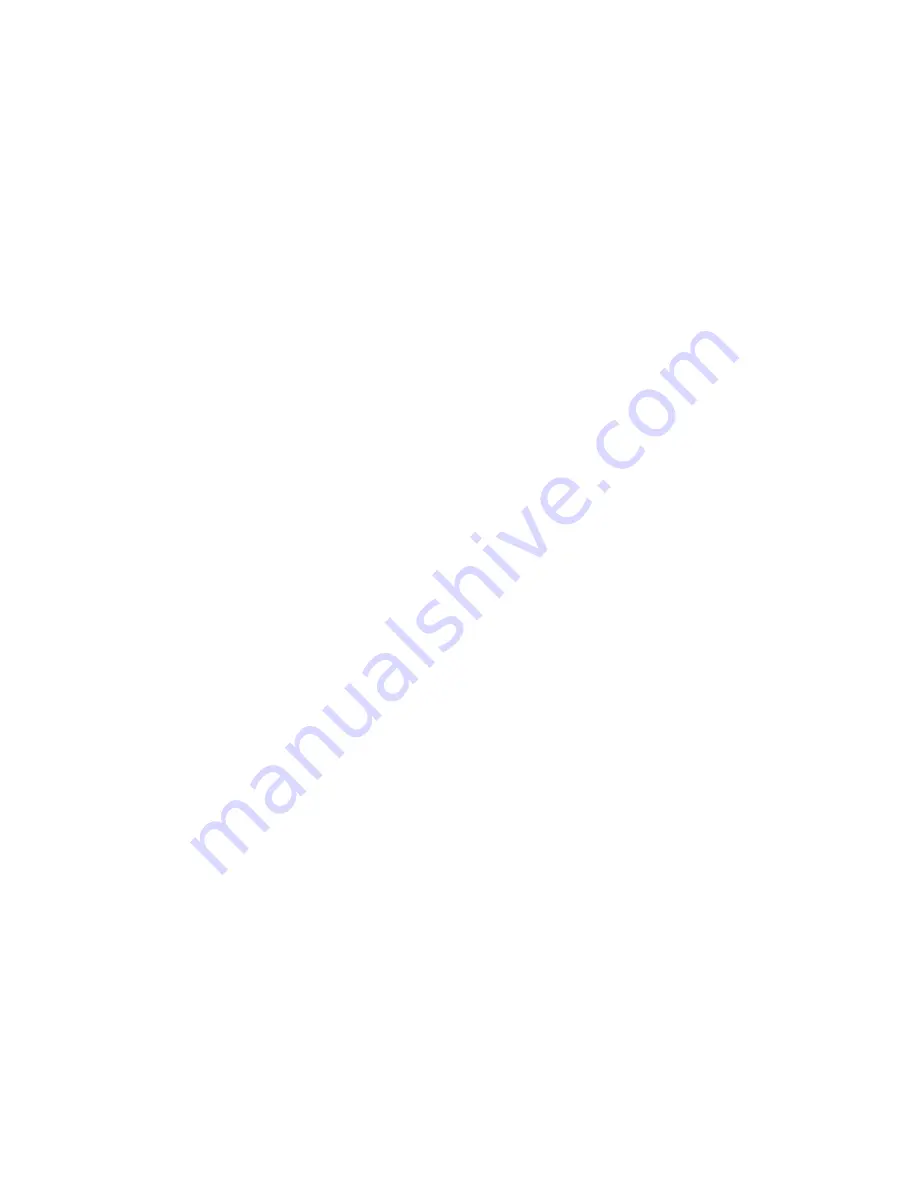
SYSTEM OPERATION
46
DIAGNOSTICS
Accessing the furnace’s diagnostic menu provides access to
the last six faults detected by the furnace. Faults are stored
most recent to least recent, Any consecutively repeated fault is
stored a maximum of three times. Example: A clogged return
air filter causes the furnace limit to trip repeatedly. The control
will only store this fault the first three consecutive times the
fault occurs. Navigate to the diagnostics menu as described
above in the thermostat installation manual.
NOTE:
It is highly recommended that the fault history be
cleared when performing maintenance or servicing the furnace.
NORMAL SEQUENCE OF OPERATION
POWER UP
The normal power up sequence is as follows:
•
115 VAC power applied to furnace.
•
Integrated control module performs internal checks.
•
Integrated control module monitors safety circuits con
-
tinuously.
•
Furnace awaits call from thermostat. 7-segment LED’s
display
LDL
while awaiting call from thermostat.
HEATING MODE
NOTE: Upon power up, the gas valve stepper motor
may activate to change position. During this event, a
slight clicking sound from the stepper motor may be
heard. This clicking sound is inherent to the stepper
motor calibration and does not indicate a problem.
The normal operational sequence in heating mode is as
follows:
•
W thermostat contact closes, initiating a call for heat.
•
Integrated control module performs safety circuit
checks.
•
Induced draft blower is energized on high speed for a
15-second prepurge.
•
Induced draft blower steps to low speed following pre
-
purge. Low stage pressure switch contacts are closed.
Igniter warm up begins upon Inducer draft blower step
to low speed and presence of closed low stage pressure
switch contacts.
•
Gas valve opens at end of igniter warm up period,
delivering gas to burners and establishing flame.
•
Low stage gas flow on Modulating product is 50% flow
rate.
•
Integrated control module monitors flame presence.
Gas valve will remain open only if flame is detected.
•
Based on the furnace internal control algorithms the gas
valve and induced draft blower will modulate to provide
the correct gas input needed. After a power cycle, the
first gas heat call will result in high stage operation.
•
Circulator blower is energized on heat speed following
the selected blower on delay and will begin to ramp
up. Electronic air cleaner terminal is energized with
circulator blower.
•
Furnace is now operating on the specified stage deter
-
mined by the internal control algorithm.
•
Furnace runs, integrated control module monitors safety
circuits continuously.
•
The W terminal thermostat contacts open, which ends
the call for heat.
•
The gas valve closes, extinguishing the flame.
•
Induced draft blower is de-energized following a 15
second post purge.
•
Circulator blower continues running for the selected
heat off delay period.
•
Circulator blower and electronic air cleaner terminal
are de-energized.
•
Circulator blower shuts off after the heat off delay period
expires.
•
Furnace awaits next call from thermostat.
OPERATIONAL CHECKS
The burner flames should be inspected with the burner
compartment door installed. Flames should be stable, quiet,
soft, and blue (dust may cause orange tips but they must not
be yellow). Flames should extend directly outward from the
burners without curling, floating, or lifting off. Flames must
not impinge on the sides of the heat exchanger firing tubes.
SAFETY CIRCUIT DESCRIPTION
A number of safety circuits are employed to ensure safe and
proper furnace operation. These circuits serve to control any
potential safety hazards and serve as inputs in the monitoring
and diagnosis of abnormal function. These circuits are contin
-
uously monitored during furnace operation by the integrated
control module.
INTEGRATED CONTROL MODULE
The integrated control module is an electronic device which,
if a potential safety concern is detected, will take the neces
-
sary precautions and provide diagnostic information through
an LED.
PRIMARY LIMIT
T
he primary limit control is located on the partition panel and
monitors heat exchanger compartment temperatures. It is
a normally-closed (electrically), automatic reset, tempera
-
ture-activated sensor. The limit guards against overheating
as a result of insufficient conditioned air passing over the
heat exchanger.
AUXILIARY LIMIT
The auxiliary limit controls are located on or near the circula
-
tor blower and monitors blower compartment temperatures.
They are a normally-closed (electrically), manual-reset sen
-
sors. These limits guard against overheating as a result of
insufficient conditioned air passing over the heat exchanger.