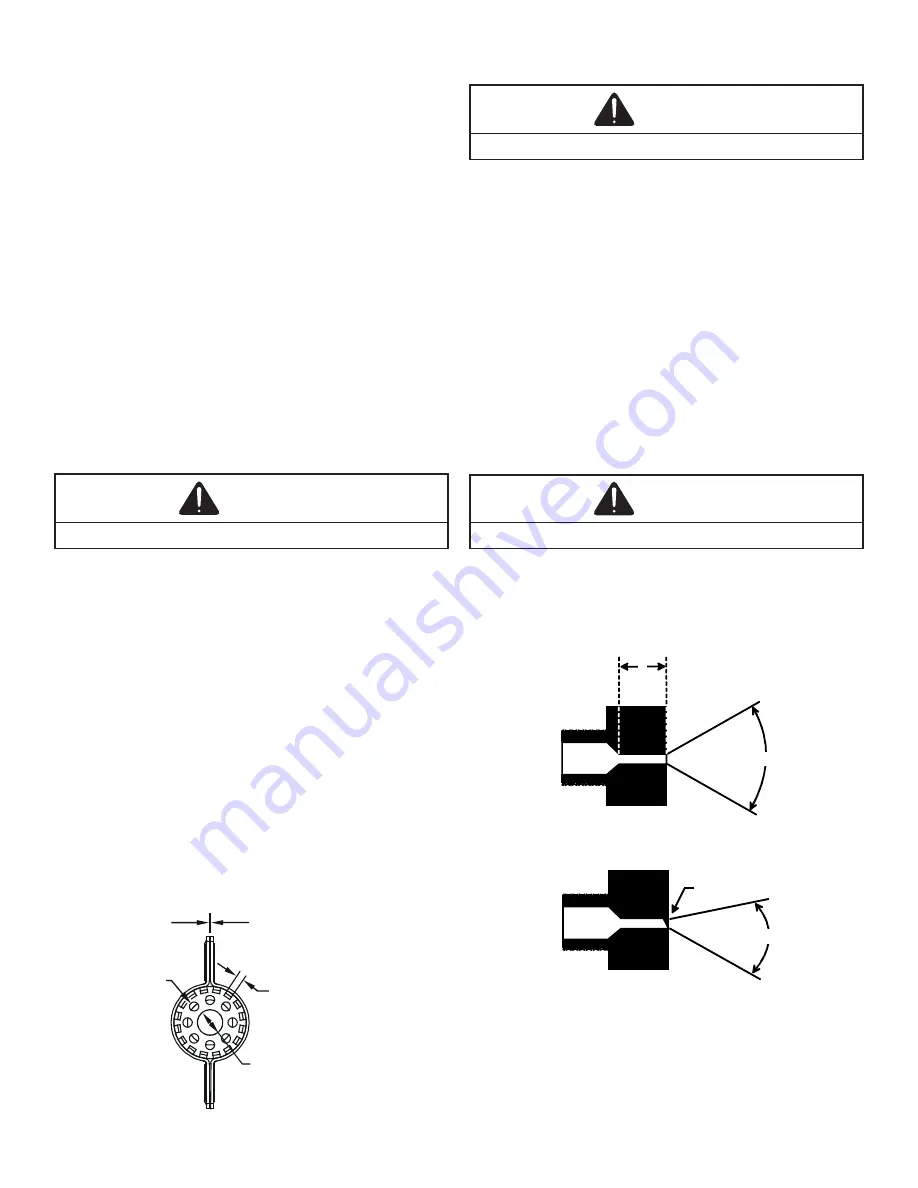
SERVICING
38
4. Touch one probe of the ohmmeter to the motor frame
(ground) and the other probe in turn to each lead. If
the windings do not test continuous or a reading is
obtained to ground, replace the motor.
5. If the windings have a continuity reading, reconnect
wires. Turn power on to the furnace and turn the ther-
mostat on in the heating mode. Check voltage for
115V at the induced draft motor terminals during the
trial for ignition. If you have 115V and the motor does
not run, replace the induced draft motor.
6. After completing check and/or replacement of induced
draft motor, reinstall burner compartment door.
7. Turn on electrical power and verify proper unit
operation.
CHECKING GAS VALVE (Redundant)
A combination redundant operator type gas valve which pro-
vides all manual and automatic control functions required for
gas fired heating equipment is used.
The valve provides control of main burner gas flow, pressure
regulation, and 100 percent safety shut-off.
WARNING
Disconnect ALL power before servicing.
Single stage gas valves should be tested on the furnace with
24 VAC connected to the gas valve and manometers read-
ing supply line and manifold pressures.
CHECKING MAIN BURNERS
The main burners are used to provide complete combustion
of various fuels in a limited space, and transfer this heat of
the burning process to the heat exchanger.
Proper ignition, combustion, and extinction are primarily due
to burner design, orifice sizing, gas pressure, primary and
secondary air, vent and proper seating of burners.
Burners have been redesigned for 34.5” chassis furnaces.
Overall length and width dimensions remain the same as
40” model burners. The burners used 34.5” models have
burner head insert with larger diameter center hole and a
larger number of surrounding holes.
.025 .002
(CARRYOVER SLOT WIDTH)
±
16X
.125 x .030 MIN SLOT
12X Ø.125
Ø.562
Beckett Burner
WARNING
Disconnect ALL Gas and Electrical Power Supply.
In checking main burners, look for signs of rust, oversized
and undersized carry over ports restricted with foreign ma-
terial, etc, refer to previous drawing. Burner cross-over slots
should not be altered in size.
CHECKING ORIFICES
Single stage furnaces are factory equipped with #45 gas
orifices.
Orifices should be treated with care in order to prevent dam
-
age. They should be removed and installed with a box-end
wrench in order to prevent distortion. In no instance should
an orifice be peened over and redrilled. This will change
the angle or deflection of the vacuum effect or entraining
of primary air, which will make it difficult to adjust the flame
properly.
WARNING
Disconnect ALL Gas and Electrical Power Supply.
1.
Check orifice visually for distortion and/or burrs.
2.
Check orifice size with orifice sizing drills.
3.
If resizing is required, a new orifice of the same physi
-
cal size and angle with proper drill size opening should
be installed.
A
GAS
STREAM B
The length of Dimension “A” determines the angle of Gas
Stream “B”.
DENT OR
BURR
GAS
STREAM B
A dent or burr will cause a severe deflection of the gas
stream.