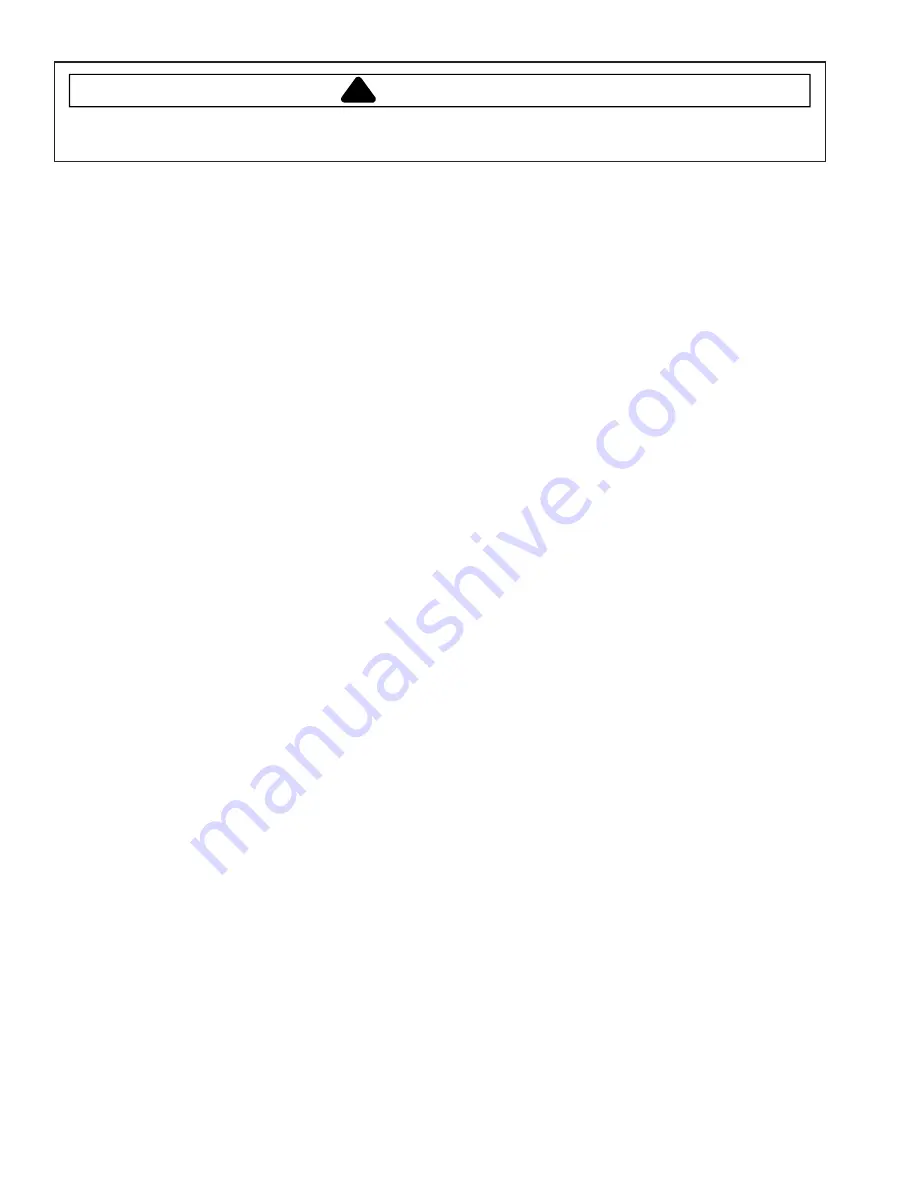
4
16026312
©2006 Maytag Services
Product Design
To avoid risk of electrical shock, personal injury, or death, disconnect electrical power source to unit, unless test
procedures require power to be connected. Discharge capacitor through a resistor before attempting to service.
Ensure all ground wires are connected before certifying unit as repaired and/or operational.
!
WARNING
Refrigeration System
Compressor forces high temperature vapor into fan
cooled tube and wire condenser where vapor is cooled
and condensed into high pressure liquid by circulation
of air across condenser coil. (See Refrigerant Flow
Diagram, page 18)
High pressure liquid passes into post-condenser loop
which helps to prevent condensation around freezer
compartment opening and through molecular sieve drier
and into capillary tube. Small inside diameter of
capillary offers resistance, decreasing pressure and
temperature of liquid discharged into evaporator.
Capillary diameter and length is carefully sized for each
system.
Capillary enters evaporator at top front. Combined liquid
and saturated gas flows through front to bottom of coil
and into suction line. Aluminium tube evaporator coil is
located in freezer compartment where circulating
evaporator fan moves air through coil and into fresh food
compartment.
Large surface of evaporator allows heat to be absorbed
from both fresh food and freezer compartments by
airflow over evaporator coil causing some of the liquid to
evaporate. Temperature of evaporator tubing near end of
running cycle may vary from -13°F to -25°F.
Saturated gas is drawn off through suction line where
superheated gas enters compressor. To raise
temperature of gas, suction line is placed in heat
exchange with capillary.
Temperature Controls
Freezer compartment temperature is regulated by air
sensing thermistor at top front of freezer compartment
which actuates compressor. Control should be set to
maintain freezer temperature between 0°F to -2°F.
Fresh food compartment temperature is regulated by an
air damper control governing amount of refrigerated air
entering fresh food compartment from freezer. Fresh
food compartment temperature should be between 38°F
and 40°F.
Evaporator and Ice Box Fans are multiple speed low
voltage fans that change speeds depending on
conditions changing in refrigerator.
Defrost System
Fully Electronic Defrost System
The Control Board adapts the compressor run time
between defrosts
to achieve optimum defrost intervals
by monitoring the length of time the defrost heater is
on.
After initial power up, defrost interval is 4 hours
compressor run time. Defrost occurs immediately after
the 4 hours.
Note:
Once unit is ready to defrost there is a 4 minute
wait time prior to the beginning of the defrost
cycle.