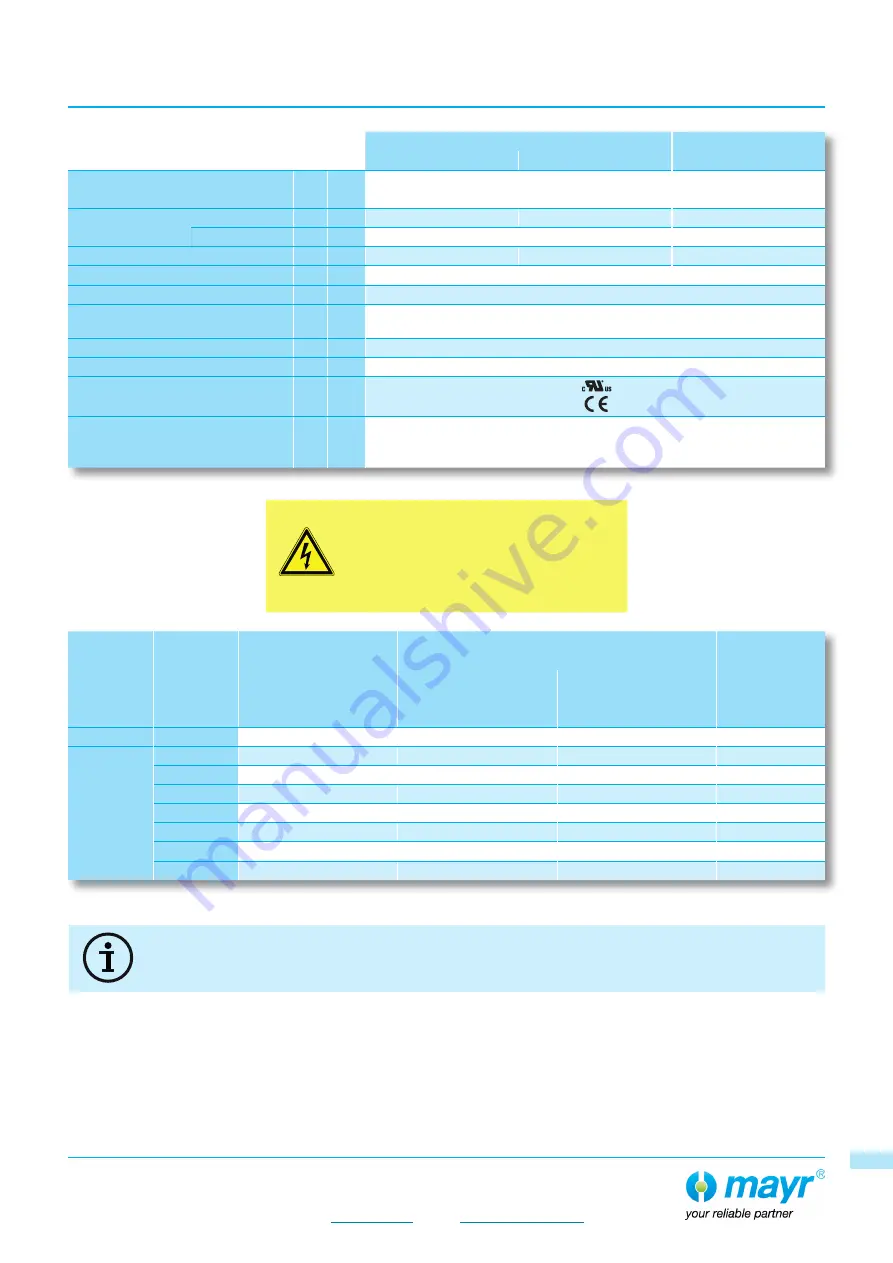
Installation and Operating Instructions for
ROBA
®
-multiswitch Type 019._00.2
(B.019+002.EN)
29/03/2022 GC/TH/MA/SU
Page 3 of 6
Chr. Mayr GmbH + Co. KG
Eichenstraße 1, D-87665 Mauerstetten, Germany
Tel.: +49 8341 804-0, Fax: +49 8341 804-421
www.mayr.com
, E-Mail:
Technical Data
Type 019.100.2
Type 019.200.2
Size 10
Size 20
Size 20
Frequency
Input
voltage
[Hz]
50 – 60
50 – 60
50 – 60
Output current
at ≤ 45 °C
I
RMS
[A]
2.0
2.0
4.5
at max. 70 °C
I
RMS
[A]
1.0
1.0
2.25
Fitted protective varistors
U
RMS
[V]
300
550
550
Device fuses
T 5 A (H) 5 x 20 mm
T 5 A (H) 6.3 x 32 mm
T 10 A (H) 6.3 x 32 mm
Protection
IP65 components / IP20 terminals / IP20 DIP switch
Terminals
Nominal cross-section 1.5 mm
2
(AWG 22-14),
screws M3, max. tightening torque 0.5 Nm
Ambient temperature
[°C]
-25 to +70
Storage temperature
[°C]
-40 to +70
Conformity markings
Installation conditions
The installation position can be user-defined.
Please ensure sufficient heat dissipation and air convection!
Do not install near to sources of intense heat!
Special designs with other input and output voltages as well as longer overexcitation times are available on
request!
* On special designs, deviating values are possible. The values stated on the Type tag are decisive.
DANGER
Danger of death! Do not touch voltage-
carrying lines and components.
No mains separation!
Voltage control through phase angle
control system
Sizes
Type
Input voltage *
± 10 % acc. EN 50160
Output voltage *
± 10 %
Article number
Overexcitation voltage
Holding voltage
U
O
U
H
[VAC]
[VDC]
[VDC]
10
019.100.2
100 – 275
90
52
8186586
20
019.100.2
200 – 500
180
104
8185591
019.200.2
200 – 500
180
104
8242954
019.100.2
230
207
30
8225580
019.200.2
230
207
30
8237887
019.200.2
230
207
40
7078520
019.200.2
230
207
-
7075719
019.100.2
300 – 500
240
52
8220914
33