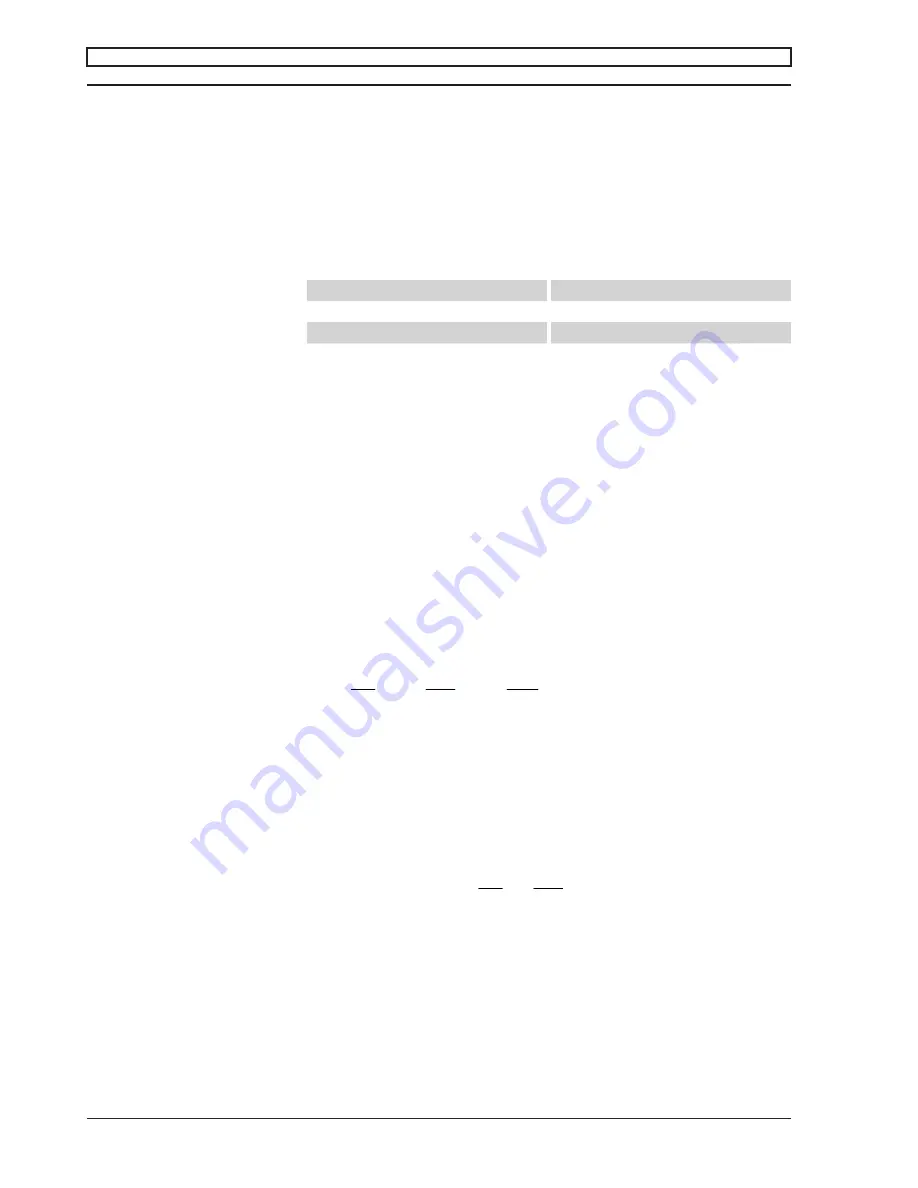
maxon motor
6
maxon motor control
1-Q-EC Amplifier DEC Module 50/5
Operating Instructions
April 2015 Edition / document number 1094861_PDF_E - 05 / subject to change
4 Commissioning Instructions
4.1 Power supply layout
Any available power supply can be used, as long as it meets the minimum
requirements shown below.
During commissioning and adjustment phases, we recommend to mechani-
cally separate the motor from the machine to prevent damage due to uncon-
trolled motion!
Power supply requirements
Nominal output voltage
6 VDC < V
CC
< 50 VDC
Absolute minimum output voltage
6 VDC
Absolute maximum output voltage
55 VDC
Output current
depending on load, continuous max. 5 A
acceleration, short-time max. 10 A
The required supply voltage can be calculated as follows:
Known values
Ö
Operating torque M
B
[mNm]
Ö
Operating speed n
B
[rpm]
Ö
Nominal motor voltage U
N
[V]
Ö
Motor no-load speed at U
N
, n
0
[rpm]
Ö
Speed/torque gradient of the motor
D
n/
D
M [rpm/mNm]
Sought value
Ö
Supply voltage V
CC
[V]
Solution
V
M
M
n
n
n
U
V
B
B
o
N
cc
3
.
0
95
.
0
1
¸
¹
·
¨
©
§
'
'
Select a power supply capable of supplying this calculated voltage under
load. The formula takes into account a maximum PWM duty cycle of 95%
and a 0.3 V maximum voltage drop (at maximum output current) of the power
stage.
What speed can be reached with a given power supply:
»¼
º
«¬
ª
'
'
»
¼
º
«
¬
ª
B
N
cc
B
M
M
n
U
n
V
V
n
0
3
.
0
95
.
0
Note
Ö
During controlled deceleration, the power supply must be able to buffer
the back-fed energy e.g. in a capacitor.
Ö
The under voltage protection switches off the DEC Module 50/5, as soon
as the supply voltage V
CC
drops below 6 V. Therefore, at low supply vol-
tage V
CC
attention has to be payed to the voltage drop over the supplying
cables.