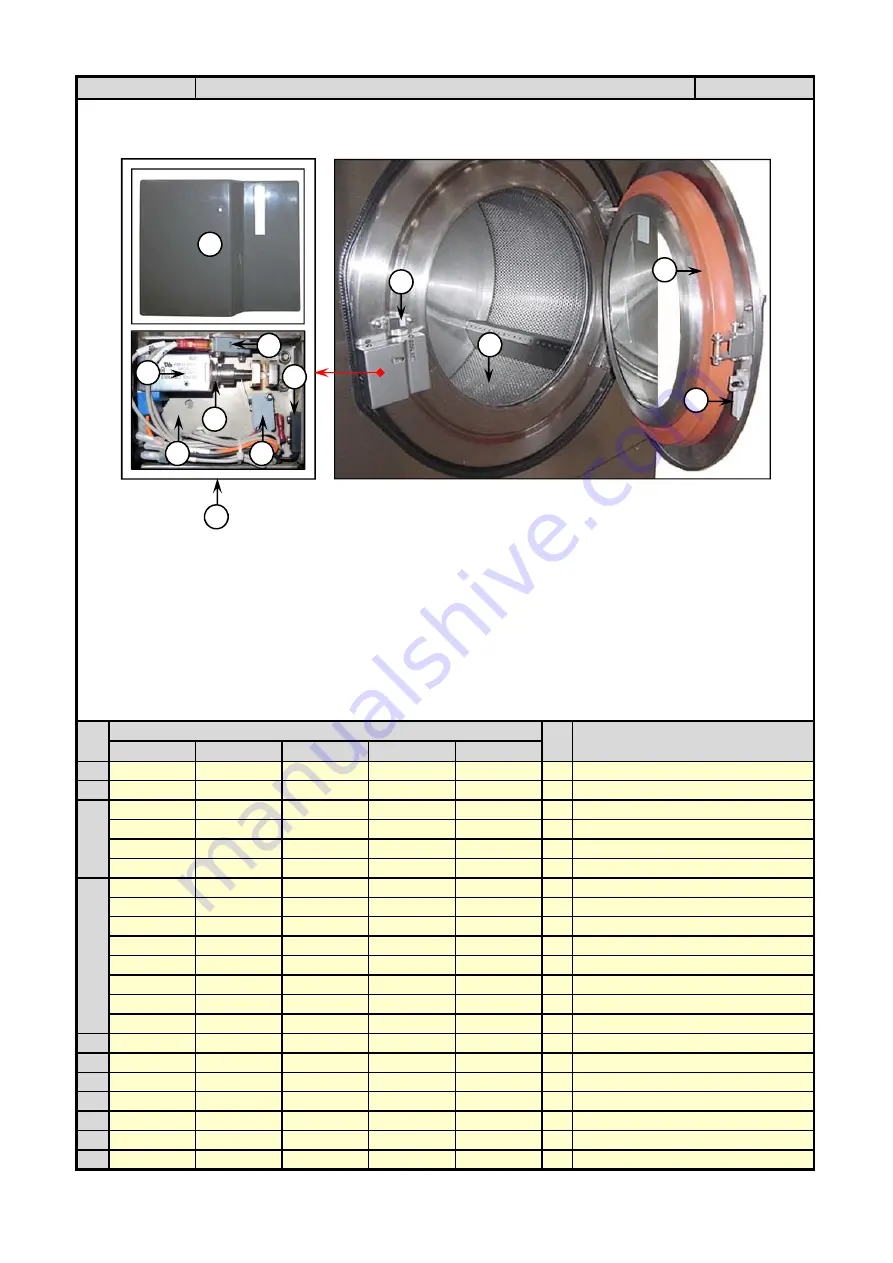
20 lb.
30 lb.
40 lb.
60 lb.
80 lb.
1
A1-ST00-002
A1-ST00-002
A1-ST00-002
A1-ST00-002
A1-ST00-002
1 Set
Door lock assembly complete set
2
A0-A237-001
A0-A237-001
A0-A237-001
A0-A237-001
A0-A237-001
1
Door lock cover Plastic
A0-A001-079
-
-
-
-
1
Gasket Door, Silicone L=990mm.
A0-A001-011
A0-A001-011
-
-
1
Door Gasket Silicone Orange, Length 44.1"
-
-
-
A0-A001-012
-
1
Door Gasket Silicone Orange, Length 54"
-
-
-
-
A0-A001-014
1
Door Gasket Silicone Orange, Length 60.6"
A1-S204-010
-
-
-
-
1
Basket stainless steel
-
A1-S302-018
-
-
-
1
Basket stainless steel
-
-
A1-S402-018
-
-
1
Basket stainless steel
-
-
-
A1-S602-018
-
1
Basket stainless steel
-
-
-
-
A1-S802-018
1
Basket stainless steel
A0-A005-104
A0-A005-104
-
-
-
1
Seal, V-Ring (STD)
-
-
A0-A005-105
A0-A005-105
-
1
Seal, V-Ring (STD)
-
-
A0-A005-337
-
-
1
Seal, V-Ring (Option)
5
A0-A013-009
A0-A013-009
A0-A013-009
A0-A013-009
A0-A013-009
1
Door lock block
6
A0-A036-001
A0-A036-001
A0-A036-001
A0-A036-001
A0-A036-001
1
Magnet actuator for magnetic reed Switch (White)
7
A0-A008-120
A0-A008-120
A0-A008-120
A0-A008-120
A0-A008-120
1
Spring, Solenoid lock
8
A0-E015-018
A0-E015-018
A0-E015-018
A0-E015-018
A0-E015-018
1
Solenoid Door Lock Magnetic , Latching 1 Coil 24VDC. + Pin
9
A0-E014-015
A0-E014-015
A0-E014-015
A0-E014-015
A0-E014-015
2
Micro switch
10
A0-E014-007
A0-E014-007
A0-E014-007
A0-E014-007
A0-E014-007
1
Switch, Magnet reed
11
A1-ST00-002-01
A1-ST00-002-01
A1-ST00-002-01
A1-ST00-002-01
A1-ST00-002-01
1
Base box with Guides
Qty.
Description
Section 8
4
Part List : Door Lock Assembly
Page 6
3
Item
Part No.
1
2
3
4
5
6
7
8
9
9
10
11
Summary of Contents for MWHE20
Page 1: ......
Page 12: ...SPECIFICATION COMPONENT IDENTIFICATION 2 3 C B ...