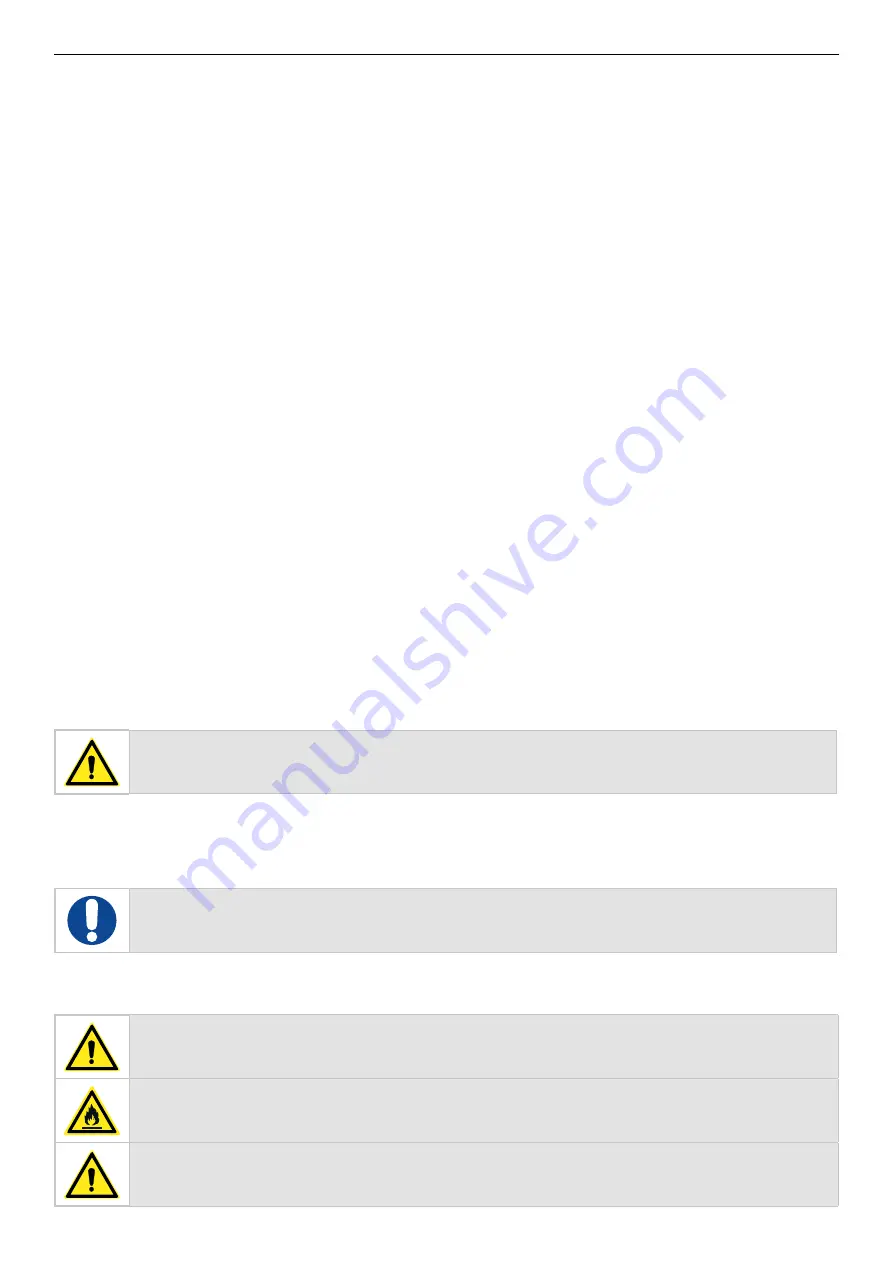
i-32V5
Air/water inverter heat pumps with axial fansi
11
4.5
SPECIFIC R32 GAS WARNINGS
The R32 refrigerant gas:
•
is odourless;
•
is flammable, but only if there are naked flames;
•
it may cause an explosion, but only if a given concentration in air is reached.
It is good practice to follow these guidelines:
•
do not smoke near the unit;
•
affix a no smoking sign near the unit;
•
keep the room where the unit is installed well ventilated;
•
do not drill or burn the unit;
•
do not place the unit near sources of ignition, such as open flames, electric heaters, etc;
•
every extraordinary maintenance or repair on the unit must be performed by skilled technicians or qualified personnel;
•
a gas leak test must be performed after installation.
4.6
R32 GAS CHARGE
The procedures described below may only be performed by skilled technicians or qualified personnel:
•
ensure the R32 is not contaminated by any other types of refrigerant;
•
keep the gas cylinder in an upright position when charging;
•
apply the appropriate label on the unit after charging;
•
do not charge more refrigerant gas than needed;
•
when charging is completed, perform leak tests before the operating test;
•
once all the above operations have been completed, a second leak test should be performed.
4.7
R32 GAS DISPOSAL
The procedures described below may only be performed by skilled technicians or qualified personnel:
•
Do not discharge the gas in area where there is a risk of explosive mixtures forming with air. The gas should be disposed of in a suitable flare
with flashback arrestor. Contact the supplier if operating instructions are considered necessary.
4.8
SAFETY RULES FOR R32 GAS TRANSPORT AND STORAGE
Before opening the unit’s packaging, ensure there are no gas leaks in the environment with an appropriate gas detector. Check that there are
no ignition sources near the unit.
No smoking near the unit.
Transport and storage must be performed in accordance with the national regulations in force. Specifically, according to ADR provisions, the total
maximum quantity by transport unit in terms of net mass for flammable gases is 333 kg.
5. INSTALLATION
CAUTION: All the operation described below must be done by QUALIFIED PERSONNEL ONLY. Before any operation on the
unit, make sure that power supply is disconnected. Also ensure, that the power supply cannot be accidentaly switched back
on until all the operations are over, by means of appropriate locks.
5.1
GENERAL
When installing or intervening on the chiller unit, it is necessary to strictly follow the rules listed in this manual, to observe all the indications on
the unit and however to take all possible precautions. Failure to comply with the rules reported on this manual can create dangerous situations.
After receiving the unit, immediately check its integrity. The unit left the factory in perfect condition; any damage must be
immediately reported to the carrier and recorded on the Delivery Note before signing it.
The company must be informed, within 8 days, of the extent of the damage. The Customer should prepare a written statement of any severe
damage.
CAUTION:The units are designed for outdoor installation. The outside temperature must never exceed 46°C. Beyond this
value, the unit is no longer covered by the current regulations in the field of safety of pressure equipment.
CAUTION: The installation place must be without any fire risks. Therefore, all the necessary measures should be adopted
in order to prevent the risk of fire at the installation place. The appliance must not be placed near naked flames and heat
sources. The wall of the buildings near the unit must have an adequate fire resistance class, in order to contain any fire that
may develop inside the rooms. However, it is recommended to place a fire extinguisher near the unit.
CAUTION: The unit must be installed so as to allow free movement for repair and maintenance operations. The warranty
does not cover costs for platforms or other lifting equipment needed for any interventions.
Name:
R32
HAZARDS IDENTIFICATION
Main hazards:
Asphyxia� on.
Specifi c hazards:
Quick evapora� on could cause it to freeze.
FIRST AID MEASURES
General informa� on:
Do not administer to people who are unconscious.
Inhala� on:
Immediately remove to fresh air.
Use oxygen or ar� fi cial respira� on as required.
The use of adrenaline or similar drugs should be avoided.
Eye contact:
Carefully rinse with plenty of water for at least 15 minutes and get medical a� en� on.
Skin contact:
Wash immediately with plenty of water for at least 15 minutes. Apply a sterile gauze.
Immediately remove contaminated clothing.
FIRE FIGHTING MEASURES
Ex� nguishing media:
Water spray, dry powder.
Specifi c hazards:
Breakage or explosion of vessel.
Specifi c methods:
Cool down the containers with a water spray from a safe posi� on. Stop the product leakage if possible. Use water spray,
if possible, to abate the fumes. Move the vessels away from the area of the fi re if this can be done without posing any
risks.
ACCIDENTAL RELEASE MEASURES
Personal precau� ons:
Try to stop the leak.
Evacuate personnel to safety areas.
Ven� late appropriately.
Eliminate the igni� on sources.
Use personal protec� ve equipment.
Environmental precau� ons:
Try to stop the leak.
Cleaning methods:
Ven� late the area
HANDLING AND STORAGE
Handling:
technical measures/precau� ons:
Allow effi cient air exchange and/or suc� on the work environments.
Advice for safe use:
Do not breath in fumes or aerosol.
Storage:
Close carefully and store in a cool, dry and well ven� lated area.
Keep in original containers. Incompa� ble products: explosive, fl ammable materials, organic peroxide
EXPOSURE CONTROLS/PERSONAL PROTECTION
Control parameters:
OEL – data not available.
DNEL: Derived no eff ect level (workers)
long-term – systemic eff ects, inhala� on = 7035 mg/m3.
PNEC: Predicted no-eff ect concentra� on
water (fresh water) = 0,142 mg/l
aqua� c, intermi� ent releases = 1,42 mg/l
sediment, fresh water = 0,534 mg/kg dry weight
Respiratory protec� on:
Not required.
Eye protec� on:
Safety goggles.
Hand protec� on:
Latex gloves
Hygienic measures:
No smoking
PHYSICAL AND CHIMICAL PROPERTIES
Colour:
Colourless.
Odour:
Ethereal. Hard to perceive at low concentra� ons.
Boiling point:
-51,7 °C at atm press
Flash point:
648 °C
Rela� ve gas density (air=1)
Rela� ve liquid density (water=1)
1,8
1,1
Solubility in water:
280000 mg/l.
STABILITY AND REACTIVITY
Stability:
Stable under normal condi� ons.
Materials to avoid:
Decomposi� on products
hazardous:
Air, oxidizing agents, humidity.
Under normal storage and use condi� ons, hazardous decomposi� on products should not be generated..
TOXICOLOGICAL INFORMATION
Acute toxicity:
Local eff ects:
Long term toxicity:
LD/LC50/inHALATION/4 hours/on rat = 1107000 mg/m3.
No known eff ect.
No kown eff ect.
ENVIRONMENTAL INFORMATION
Global warming poten� al
GWP (R744=1):
675
Ozone Deple� on Poten� al ODP
(R11=1):
0
Disposal considera� on:
Refer to the supplier’s gas retrieval program. Avoid direct release into the atmosphere.