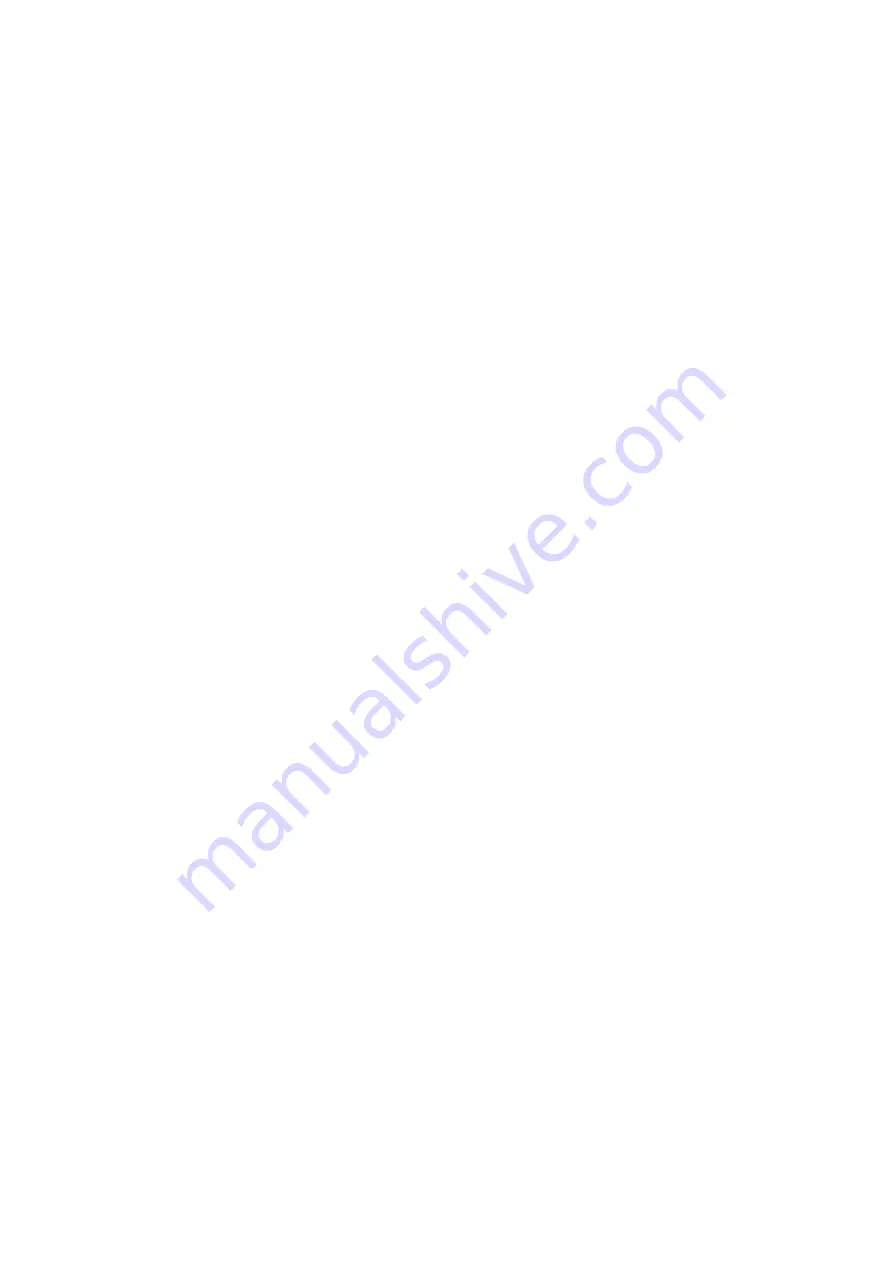
4)
THE HYDRAULIC MOTOR AND ITS ADAPTER
Do not separate the motor from its adapter.
Insert the lower drive coupling onto the leg drive shaft (lightly grease the shaft before doing this).
Position the red plastic coupling (piece n° 10 on “Spare Part Diagram”) onto the lower coupling.
Before tightening the 2 x 6 mm Allen fixing screws of the lower coupling, make sure that coupling
is pushed all the way down on drive leg shaft.
Then position the motor and tighten the 4 x 10 mm to 40Nm.
IMPORTANT: Please note that the above coupling might need to be adjusted if any other tunnel
than a Max Power tunnel (thickness 9mm) is used.
The top and bottom coupling pieces should fit tightly together to ensure maximum
gripping between them.
Check that the propellers turn freely and that there is no tight spot. A certain amount of
resistance is normal from the motor. When all is assembled recheck the tightness of all the motor
bolts.
NOTE: The coupling on the motor side is in place when delivered, do not touch this.
5) PROPELLERS
Check the tightness of the oil drain screw (8 mm Allen Key) and the anode (a 10 mm key).
IMPORTANT: To prevent limestone deposits from forming (causing damage to the joints), we
highly recommend applying silicone grease to the shaft and the joints before
assembling the propellers.
Fit the fixing pins and propellers
NOTE: Position the propeller blades opposed and not in line with one another.
Make sure that the propellers turn freely. A certain amount of resistance from the motor is normal.
Tighten the 24 mm nuts on each propeller to 27 Nm.
Ensure correct protection of hands against the propellers blades.
6) PROTECTION
GRILLS
With a shallow tunnel installation, we recommend that you protect the propellers by fitting
horizontal protection grills. These grills will however modify thruster performance.
7)
HYDRAULIC (general remarks)
A typical installation of the hydraulic power thruster requires the following elements:
oil reservoir/tank
hydraulic pump
directional control valve
hydraulic motor
circuit piping
oil cooler (depending on type of installation)
4
Manual Max Power CT300 HYD Last update:December 2013