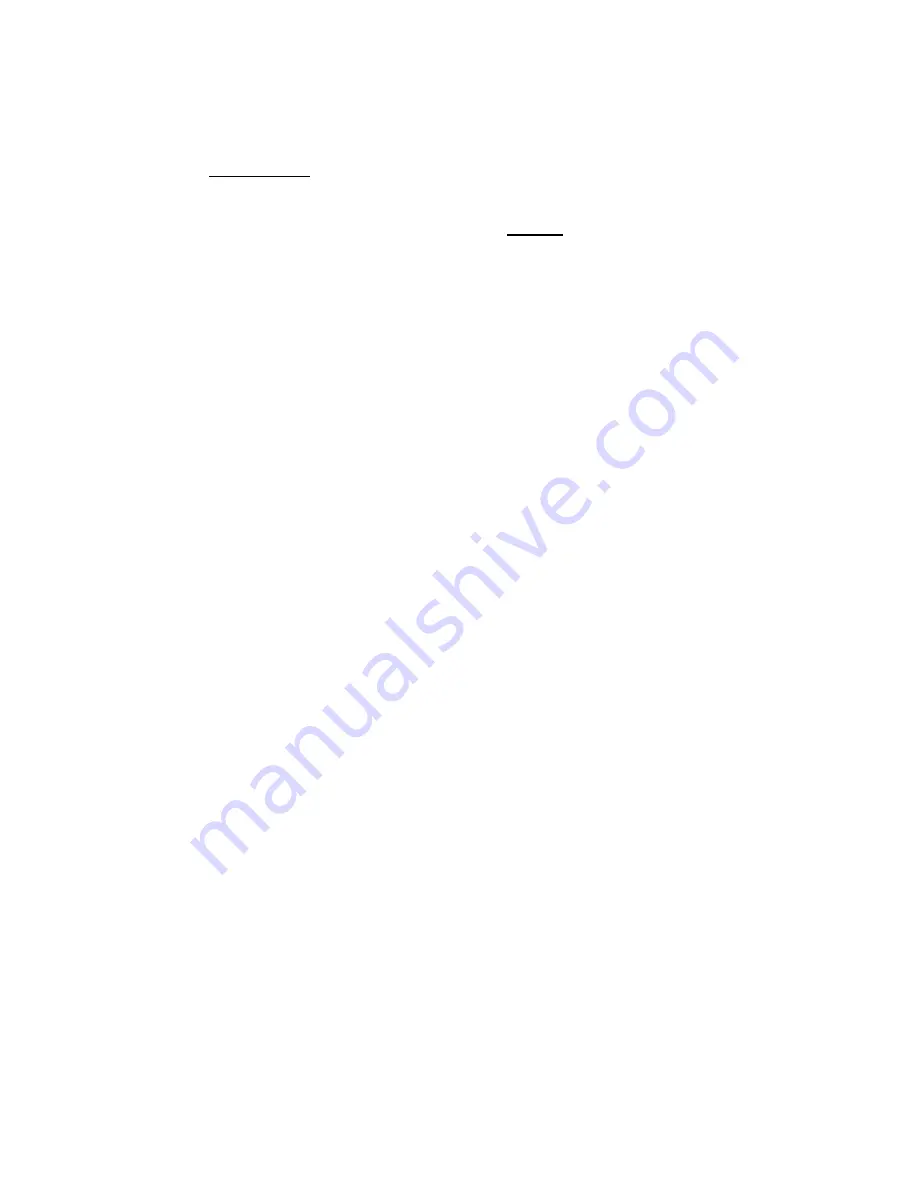
MAULE AEROSPACE TECHNOLOGY, INC.
MAINTENANCE MANUAL
FOR
MX-7-420
28
Rev. A
C. ASSEMBLY
1.
Grease pack roller bearings (A5) and lock pin (13AB) with wheel bearing grease.
Grease the parts adjacent to lock pin. Do Not grease friction washer (72B-4) or
the parts adjacent to it.
2.
Place the roller bearings (A5) in their races, the felt seals (78B-2) on the bearings,
and the three (3) springs (76B) in the three deeper holes in bracket (71B). Place
friction ring assembly (72B-3) over the springs with the pin in the shallow hole in
bracket (71B). Grease may be used to hold the foregoing parts in place. Do not
allow any grease on the friction washer surface of the friction ring assembly (72B-
3).
3.
Place shim(s) (83B) on lower shoulder of the spindle on fork (69B). Place the fric-
tion washer (72B-4) on the large diameter friction surface of the fork.
4.
Carefully slide the fork spindle through the friction ring and bearings until the fric-
tion washer is bottomed against the springs. Make sure that all parts stay in
place.