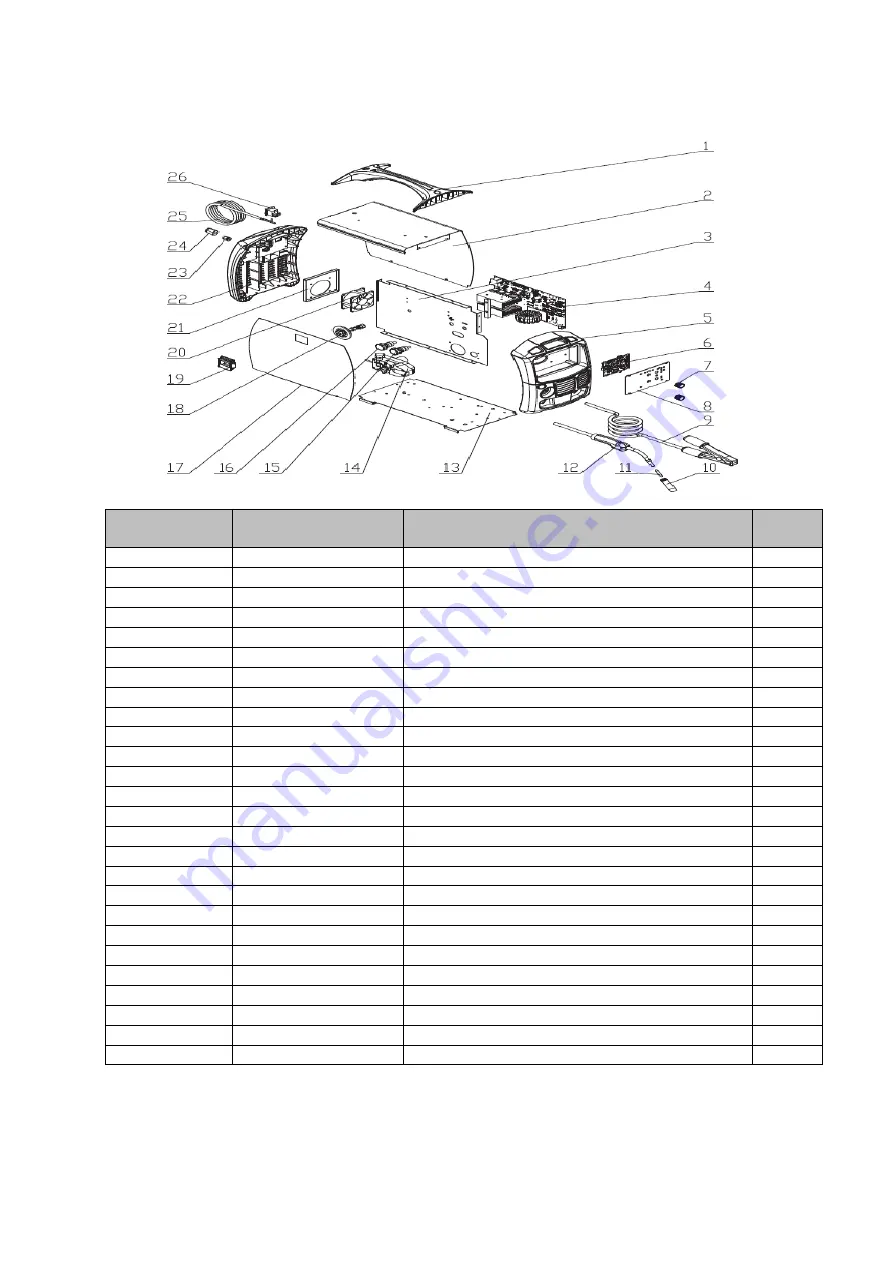
Page 19 of 20
1910308-12
DIAGRAM & PARTS LIST
REFERENCE
PART NUMBER
DESCRIPTION
QTY
1
165200032
HANDLE
1
2
165200026
ENCLOSURE
1
3
165200049
MIDDLE BOARD
1
4
165200050
MAIN CONTROL BOARD
1
5
165200002
FRONT PLASTIC PANEL
1
6
105200448
CONTROL PC BOARD
1
7
105200063
POTENTIOMETER KNOB
2
8
155200087
SUPPORT BOARD
1
9
105200199
GROUND CABLE
1
10
105200063
NOZZLE
1
11
105200043
CONTACT TIP
1
12
105200237
MIG TORCH
1
13
105200054
BASE PLATE
1
14
105200198
WIRE FEEDER
1
15
105200241
BINDING POST (BLACK)
1
16
105200242
BINDING POST (RED)
1
17
165200027
DOOR
1
18
105200009
SPOOL HOLDER ASSEMBLY
1
19
105200080
LATCH
1
20
125200077
FAN
1
21
165200051
FAN SUPPORT
1
22
165200016
BACK PLASTIC PANEL
1
23
105200441
GAS CONNECTOR
1
24
105200266
GAS HOLDER
1
25
105800002
POWER CORD
1
26
105200046
SWITCH
1
Replacement parts can be ordered through your Matco Tools Distributor
For technical questions, call
855-920-2399
.