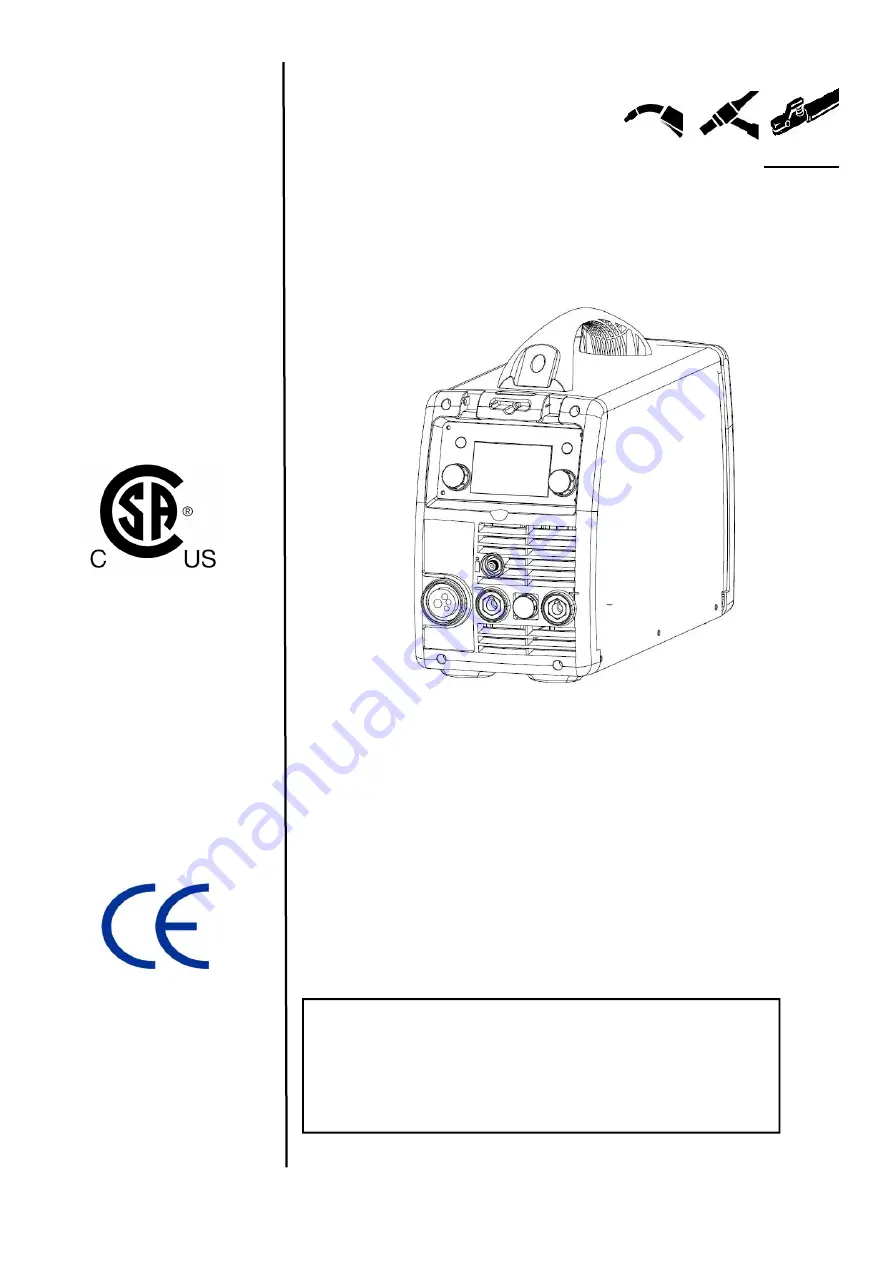
Processes
MIG (GMAW)
TIG (GTAW)
STICK (SMAW)
OPERATORS’ MANUAL
INVERTER MULTMIG WELDER
MM200 LCD
IMPORTANT:
Read this Owner’s Manual Completely
before attempting to use this
equipment. Save this manual and keep it handy for quick reference. Pay particular
attention to the safety instructions we have provided for your protection. Contact your
distributor if you do not fully understand this manual.