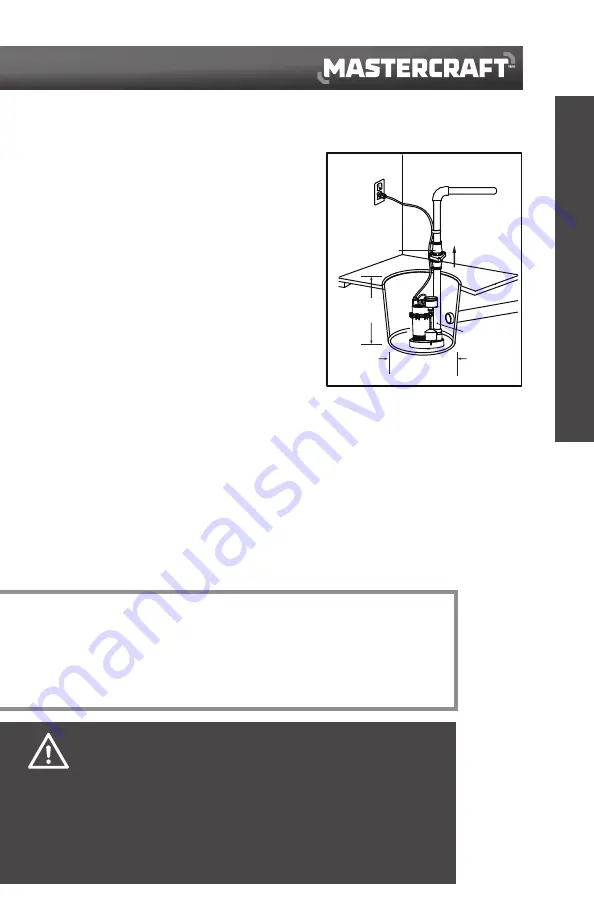
13
ASSEMBLY INSTRUCTIONS
Minimum
10" (25.4 cm)
width
1/8" (3 mm)
anti-airlock
hole
• Install the pump in sump pit with minimum diameter of
10" (25.4 cm). The sump depth should be 14" (35.6 cm).
Construct the sump pit of tile, concrete, steel or plastic.
Check local codes for approved materials and for proper
installation.
• Install the pump in a pit so that the switch operating
mechanism has maximum possible clearance.
• The pump should not be installed on clay, earth or sand
surfaces. Clean the sump pit of small stones and gravel
which could clog the pump. Keep the pump inlet screen
clear.
• Install discharge plumbing. Use rigid plastic pipe and
wrap threads with PTFE pipe thread sealant tape. Screw
pipe into the pump hand tight plus 1 1/2 turns.
• To reduce motor noise and vibrations, a short length of
rubber hose
[
1 7/8" (47.6 mm) I.D., e.g., radiator hose
]
can be connected into the discharge line near the pump using suitable clamps.
• Install an in-line check valve or an in-pump check valve to prevent flow backwards through the pump
when the pump shuts off.
• Power Supply: Pump is designed for 115 V, 60 Hz, operation and requires a minimum 15 A individual
branch circuit. Plug the power plug into a 115 V GFCI power outlet.
• If the pump discharge line is exposed to outside subfreezing atmosphere, a portion of the line
exposed must be installed so any water remaining in the pipe will drain to the outfall by gravity.
Failure to do this can cause water trapped in the discharge to freeze which could result in damage to
the pump.
• After the piping and check valve have been installed, the unit is ready for operation.
• Check the pump operation by filling the sump with water and observing pump operation through one
complete cycle.
INSTALLATION
NOTE:
Do not use ordinary pipe joint compound on plastic pipe. Pipe joint compound can
damage plastics.
If your check valve is not equipped with an air bleed hole to prevent an airlock in the
pump, drill a 1/8" (3 mm) hole in the discharge pipe just above where the discharge
pipe screws into the pump discharge. Be sure the hole is below the waterline and the
check valve to prevent airlocks.
• Risk of flooding. Can cause personal injury and/or property damage. If a flexible discharge
hose is used, make sure the pump is secured in the sump to prevent movement. Failure
to secure the pump may allow pump movement, switch interference and prevent the pump
from starting or stopping.
• Risk of flooding. Can cause personal injury and/or property damage. Failure to make an
operational check may lead to improper operation, premature failure, and flooding.
• Risk of electric shock, fire or serious injury and/or death. Pump should always be electrically
grounded to a suitable electrical ground such as a grounded water pipe or a properly-grounded
metallic raceway, or ground wire system. Do not cut off the round ground pin.
CAUTION!
DANGER!
check valve
Minimum
14" (35.6 cm)
depth
Summary of Contents for 062-3535-2
Page 2: ......