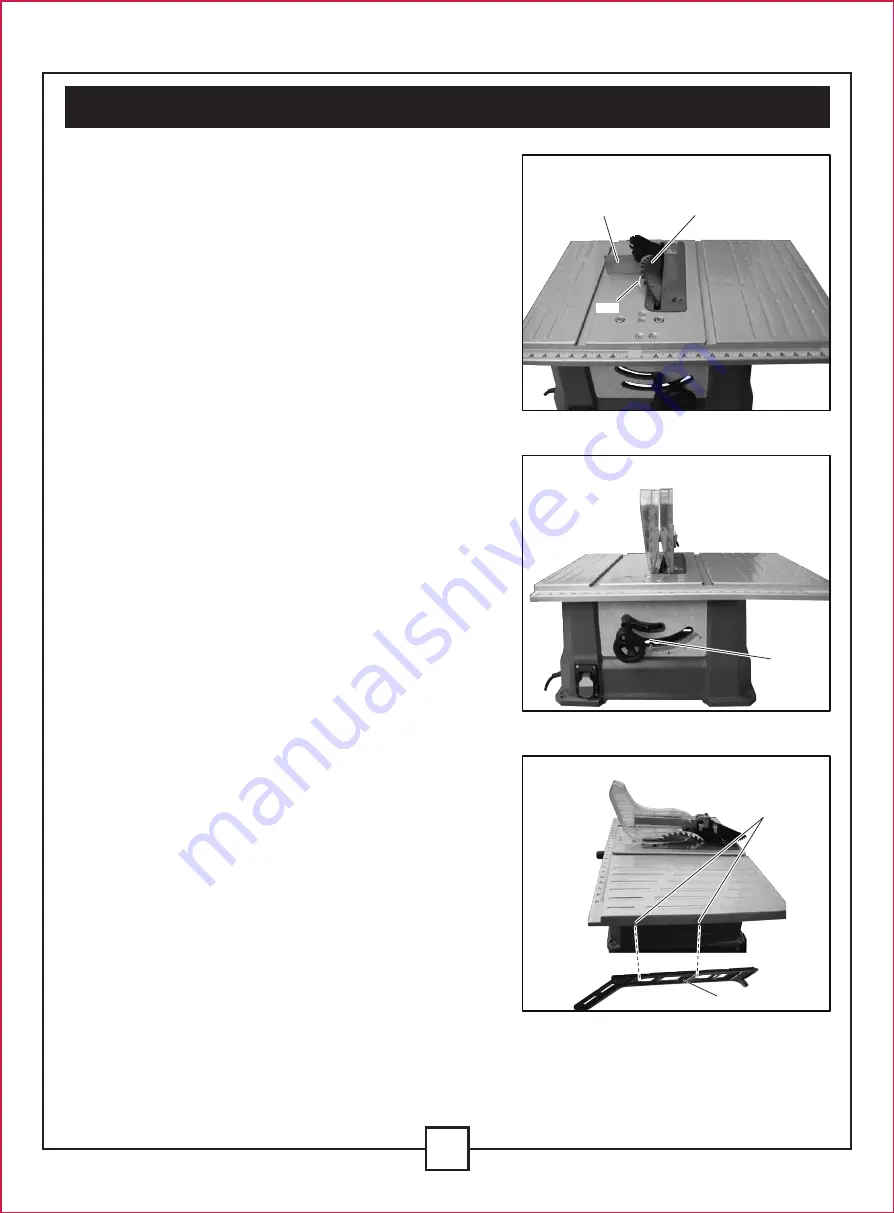
TO ADJUST THE BEVEL INDICATOR
(Fig. 28)
If the bevel indicator is not at zero when the saw blade
is at 90
o
, adjust the indicator by loosening the screw
and setting it at 0
o
on the bevel scale. Retighten the
screw.
Fig. 28
PUSH STICK STORAGE (Fig. 29)
• Insert the push stick storage screws from the loose
parts bag into the holes on the side of the saw table.
Use a screwdriver to tighten screws securely.
• Place the slots in the push stick over the screws and
slide the push stick towards the back of the saw.
Fig. 29
• Make a test cut.
Fig. 27
18
V. Assembly and adjustments (continued)
Combination square
Blade
Screw
Push stick
Push stick
storage screws
45
o