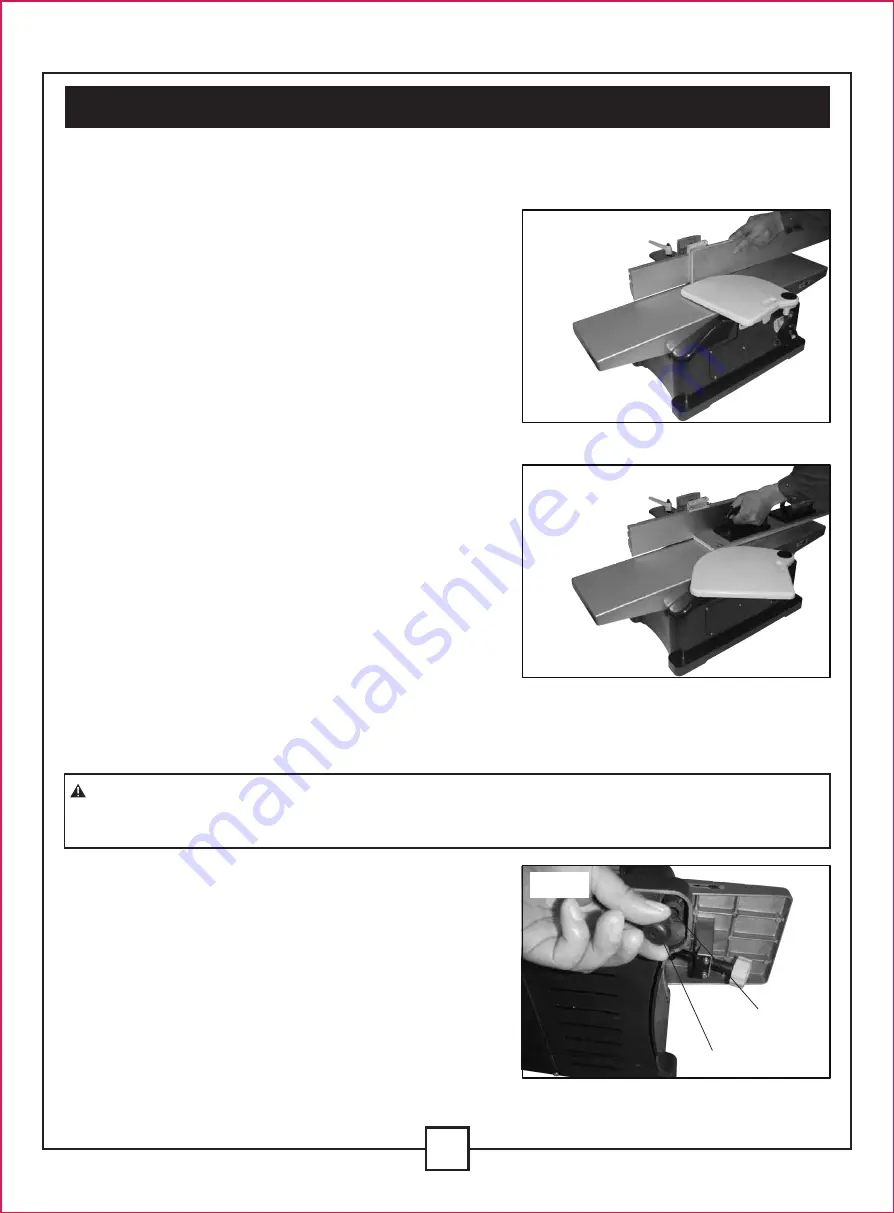
12
FUNCTIONAL DESCRIPTION
JOINTING OPERATION
Jointing cuts or edge jointing are made to square an
edge of a workpiece. The workpiece is positioned on
the jointer with the narrow edge of the workpiece on
the infeed table and the major flat surface of the
workpiece against the fence, as shown in Fig. 1. The
workpiece is moved from the infeed table, across the
cutterhead to the outfeed table.
PLANING OPERATIONS
Planing or surfacing is identical to the jointing
operation except for the position of the workpiece.
For planing, the major flat surface of the workpiece is
placed on the infeed table of the jointer with the
narrow edge of the workpiece against the fence, as
shown in Fig. 2. The workpiece is moved from the
infeed table, across the cutterhead to the outfeed
table. Use push blocks when performing planing
operations whenever possible.
V. Assembly and adjustments (continued)
Fig. 1
Fig. 2
INSTALLATION OF RUBBER FEET
- Insert the rubber feet (A) into the 4 holes (B) in the
base as shown Fig. 3.
ASSEMBLY
WARNING:
For your own safety, do not connect the machine to the power source until
the machine is completely assembled and you have read and understand the entire instruction
manual.
B
A
Fig. 3