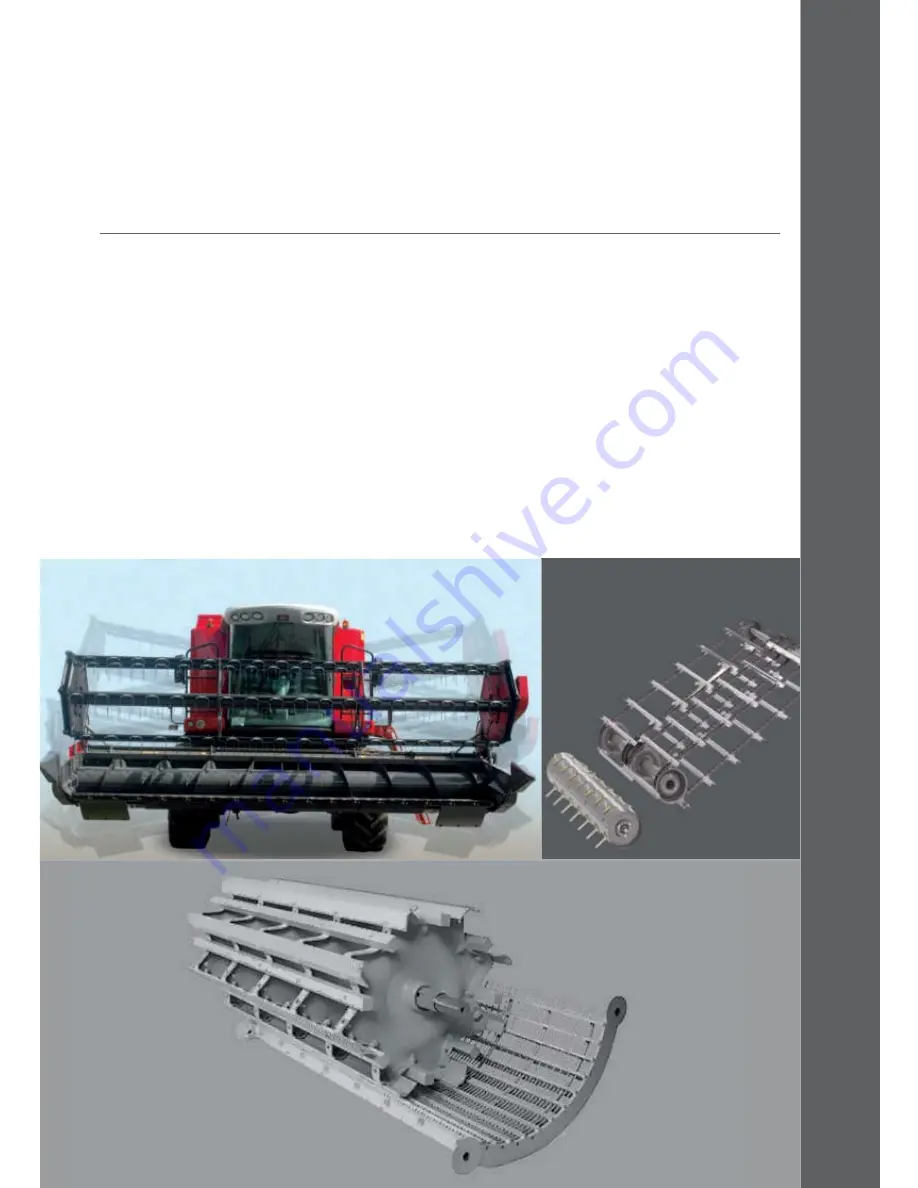
04
05
06
05
01
PowerFlow table.
02
The immensely str
ong
Fr
eeFlow header frame.
03
Schumacher knife system.
04
MF BET
A combines ar
e fi
tted
with
an Auto Level table as standar
d.
05
Power Feed Roller is located at the
fr
ont of the main cr
op elavator
.
06
Heavy duty cylinder with ballast bars
and dif
fer
ential wir
e spacing on concave.
of the concave has half as many
wires as the front section. This
principle provides the optimum
balance between high threshing
capacity and good grain fl ow
through the concave.
Independent adjustment of the
front and rear of the concave is via
electric controls in the cab. This
makes it possible for the operator
to set the concave to the optimum
position to suit the conditions. For
example, using the concave in the
parallel position allows output to
be maximised and straw damage
minimised.
The Power Feed Roller at the front
of the main crop elevator gives a
consistent crop fl ow from the table
into the main crop elevator. As a
result of the more even crop fl ow,
less power is needed to thresh
the crop. The crop is distributed
across the full width of the
elevator by the Power Feed Roller
to maximise the potential of the
threshing unit.
In addition, as the crop is readily
prepared for optimum threshing,
both power requirement and more
importantly fuel consumption
is reduced.
The key to performance!
Equipped with a robust, high-
inertia cylinder and a heavy-duty
concave, these machines are able
to effectively thresh the majority of
crops with ease.
The threshing drum has added
weight in the form of ballast bars
to increase the weight around the
cylinder as they thresh the heads.
This reduces load on the drives,
power requirement and
fuel consumption.
The concave has differentiated
wire spacing, i.e. the rear section
Summary of Contents for 7200 BETA - 275-335
Page 17: ...17...