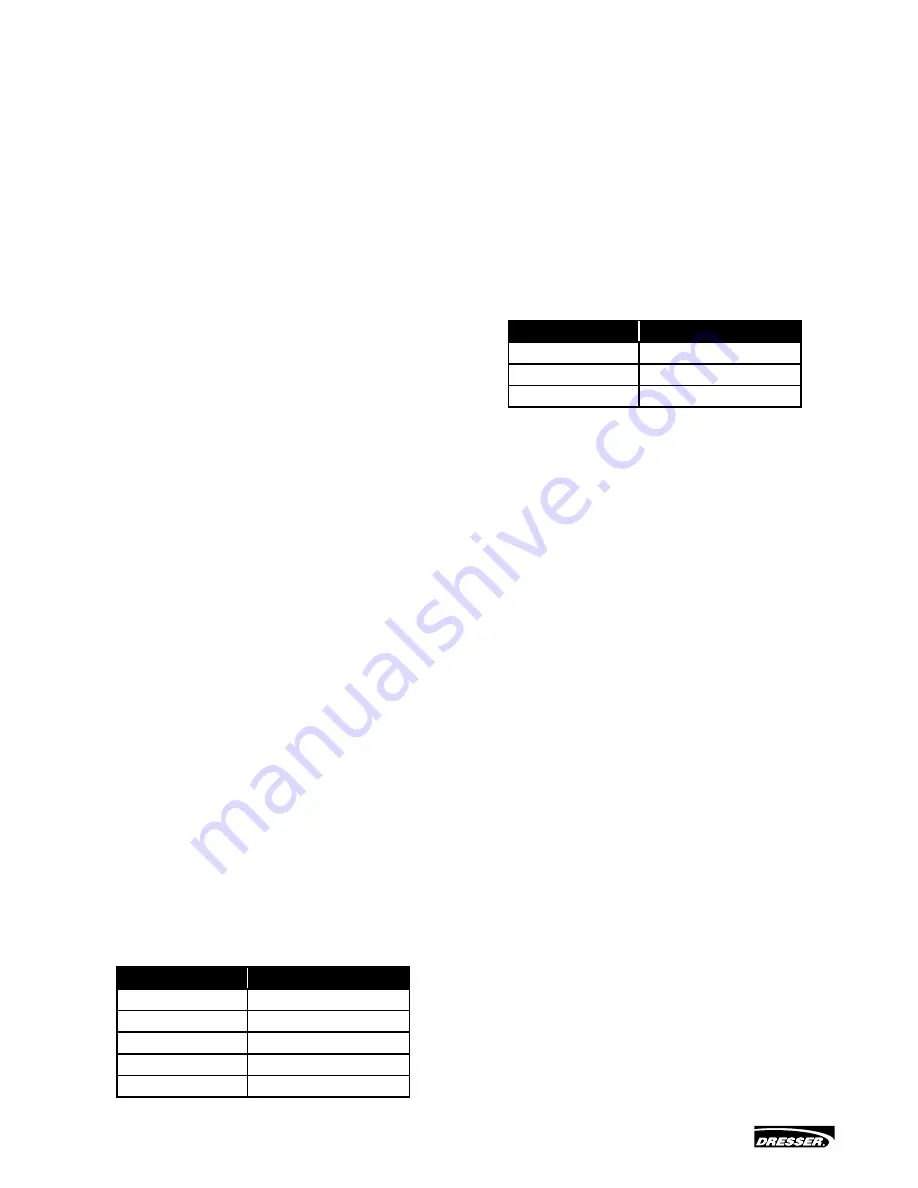
11
11
Instructions EM39003 - 05/10
39003 Series High Performance butterfly Valves
ANSI Class 600 3" – 14"
Lug Valves
Wafer
Valves
Bolt Engagement in Valve*
Studs & Nuts
Machine Bolts
Studs & Nuts
Valve
Size
Valve
Series
Thread
Size
Qty
A
Length
A
Qty
B
Length
B
Qty
C
Length
C
Qty
D
Length
D
Qty
F
Length
F
Qty
G
Length
G
Qty
E
Length
E
3"
g
¾-10
8
1.034
8
1.026
8
3.50
8
3.50
8
2.25
8
2.38
8
7.00
4"
g
7
/
8
-9
8
1.274
8
1.165
8
3.50
8
3.25
8
2.75
8
2.75
8
7.75
6"
g
1-8
12
1.274
12
1.306
12
4.75
12
4.75
12
3.25
12
3.25
12
9.50
8"
g
1
1
/
8
-8
12
1.794
12
1.795
12
5.75
12
5.75
12
4.12
12
4.12
12
11.50
10"
H
1¼-8
12
2.495
12
2.000
12
6.75
12
6.25
12
5.00
12
4.50
12
13.00
H
1¼-8 4**
1.375
4**
2.000
4**
5.50
4**
6.25
4**
3.88
4**
4.50
8**
6.25
12"
H
1¼-8
16
2.683
16
2.697
16
7.00
16
7.00
16
5.38
16
5.38
16
14.00
H
1¼-8
4**
1.325
4**
1.765
4**
5.25
4**
6.00
4**
4.00
4**
4.38
8**
6.00
14"
H
1
3
/
8
-8
16
2.994
16
2.996
16
7.50
16
7.50
16
CF
16
CF
16
15.00
H
1
3
/
8
-8
4**
1.506
4**
1.869
4**
6.00
4**
6.50
4**
CF
4**
CF
8**
6.50
Maintenance Instructions
3.1 Safety Precautions
before removing the valve from the line or loosening any bolts,
it is important to verify the following conditions:
1.
be sure the line is depressurized and drained.
2.
be sure of the pipeline media. Proper care should be taken
for protection against toxic and/or flammable fluids.
3.
never install the valve without an Operator (Manual or
Automatic) already attached to the valve shaft.
4.
never remove the Operator from the valve while the valve is in
the pipeline under pressure. The eccentric valve design may
allow line pressure to open the valve if the handle/actuator is
not in place while the valve is under pressure.
5.
Always be sure that the disc is in the full closed position
before removing or installing the valve.
6.
Take care in handling the valve. Personal injury or property
damage may result if the valve is damaged or mishandled
during maintenance operations.
3.2 General Maintenance
normal maintenance for a Masoneilan HPbV is limited to
adjustment of the shaft packing by tightening down evenly
on the gland flange using the gland flange studs and nuts.
Overtightening of the gland should be avoided since this will
shorten the life of the packing. During commissioning, it is
common for dirt and foreign objects to be left in the pipeline
during construction. This debris can damage the HPbV seat or
disc edge which will prevent the valve from providing tight shut-
off. In such cases seat replacement may be necessary.
3.3 Packing Replacement
1.
Remove the handle or actuator and the mounting hardware
from the valve.
2.
Remove the gland flange nuts and lockwashers.
3.
Remove the gland flange and gland.
4.
Replace the old packing with new packing. Correct
packing selection is important. On larger valves it may be
necessary to compress each stem seal into the stuffing box
before adding the next one.
5.
Reinstall gland, gland flange, lockwashers and nuts.
6.
Tighten the gland flange nuts evenly to torque specified in
Table 1.
7.
Operate the disc several times.
8.
Reinstall the handle or actuator and mounting hardware.
9.
Set the actuator stops.
Table 1
Valve Size (in.)
Torque (in.-lb.)
2 to 8
25
10 to 12
35
14 to 20
50
24 to 30
75
36 to 48
100
3.4 End Cap Seal Replacement
(where applicable)
1.
Remove the end cap bolts and lockwashers.
2.
Rotate the end cap to break the seal, then pull the cap out.
3.
Remove the old seal.
4.
Clean the body and end cap prior to installing the new seal.
5.
Slide the new seal into place, then guide the end cap into
the body.
6.
Align the bolt holes and reinstall the lockwashers and bolts.
7.
Tighten the bolts evenly to the torque specified in Table 2.
Table 2
Valve Size (in.)
Torque (in.-lb.)
2 to 8
50
10 to 12
80
14 to 30
100
3.5 Standard Soft Seat Replacement
1.
Place the valve on a bench with the seat retainer facing up.
Use blocks to elevate the valve above the work surface to
provide enough clearance to prevent the disc from being
damaged when the valve is opened.
2. A. Cap Screw Retainer:
Remove the cap screws and lift the seat retainer out of
the valve.
B. Wedge Ring Retainer:
Unlock the retainer by removing the set screws. If
difficulty is experienced in removing the retainer, open
the disc approximately 20 degrees and then tap the
retainer with a non metallic hammer. Lift the retainer
from the body.
3.
Remove the old seat from the seat retainer and discard.
4.
Thoroughly clean the seat cavity in the body and the seat
retainer prior to installing a new seat.
5.
Carefully clean and polish the disc sealing surface with a
soft cloth. The disc sealing surface should be free of all
grooves and scratches.
6.
Place the seat retainer on a flat surface with the seat
locating area facing up.
7.
Place the new preformed seat assembly (Seat and O-ring)
on the seat retainer with the marked (tape) side facing
down.
8.
Using the balls of each thumb, press down on the seat
engaging the shoulder of the seat behind the lip in the
seat retainer. Stretch the seat into place by sliding each
thumb around the circumference of the seat maintaining
downward pressure and forcing the seat shoulder over the
seat retainer lip.