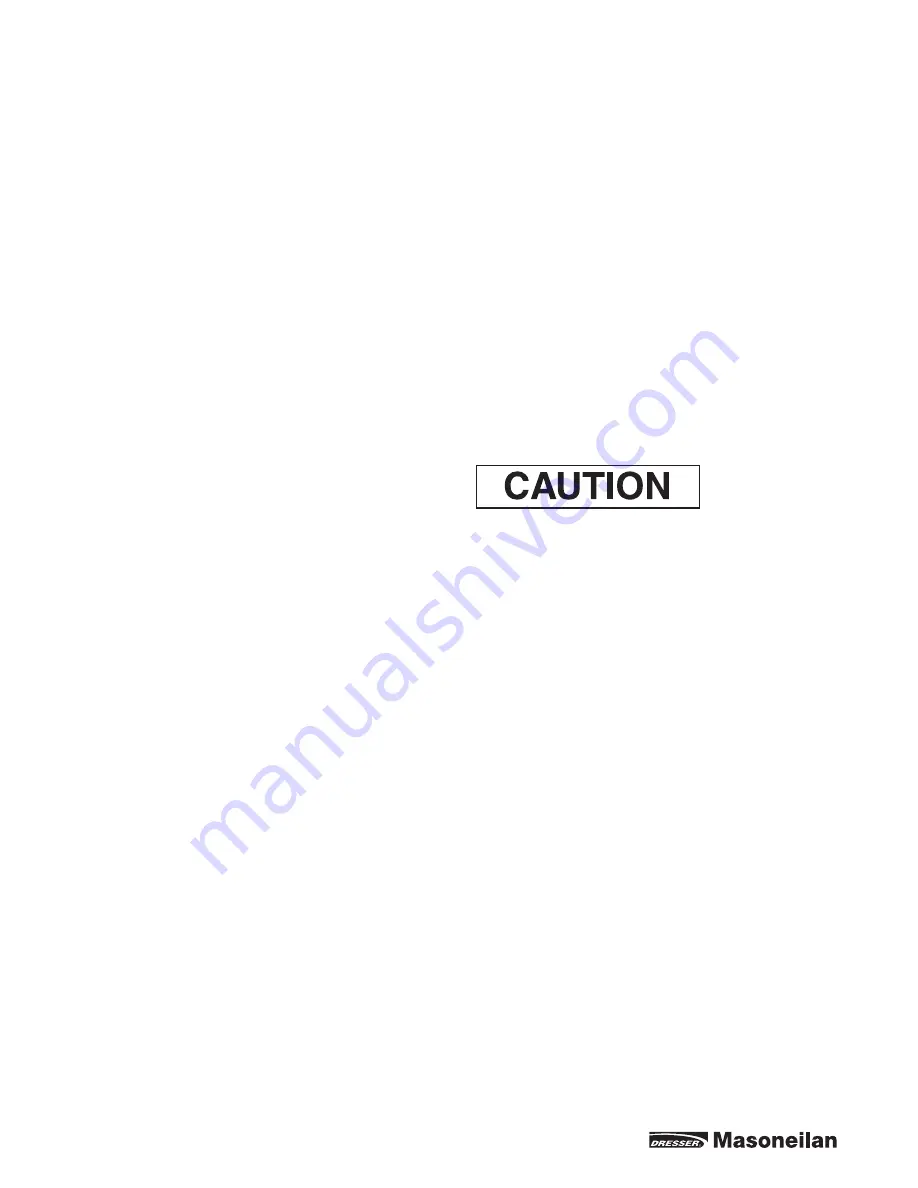
5
3.4 Maintenance
The required maintenance interval will vary depending on
application. The user must establish a suitable maintenance
depending on the operating conditions. Prior to disassembly
remove all system pressure from the regulator.
3.4.2 Disassembly
(see Figs.1-2-3-4-5).
3.4.2.1 Actuator
:
Remove spring compression by unscrewing the adjustment
screw (counter-clockwise) after loosening the lock nut. The
position of the locknut should be noted to allow closer pre-
liminary adjustment when reassembling. If the regulator is
equipped with a sealed cap (Fig.4), first remove the cap (30)
and gasket.
Remove the spring case (13) by loosening the nuts (20). Note;
it is not necessary to remove the housings on actuator sizes
220 and 360.
Remove the spring. Unscrew the nut (17).
Remove the diaphragm and washers.
3.4.2.2 Body removal:
Unscrew the nuts (27c) and remove the blindhead (1). Unscrew
the nuts (27a) Fig.1 (flanged regulator) or the screws (29)
Fig. 2 (threaded regulators). Remove the high pressure insert
(4) keeping the plug in position; remove the plug.
3.4.2.3 Parts inspection
All the components are now ready to be inspected. Replace
any worn items. Clean all parts.
Pay particular attention to the condition of the disc and plug,
both elastomeric and metal, and the seat area of the high-
pressure body.
If the seat is worn, it may be able to restore it by lapping using
a metal disk and abrasive paste.
If preferred, the regulator may be returned to an authorized
Masoneilan repair center to be reconditioned.
The diaphragm should be replaced if it shows any damage. The
same applies to Teflon diaphragm protector (if equipped).
Gaskets should not be re-used.
3.4.2.4 Reassembly
Carry out the disassembly operations in reverse order.
Push the plug stem into the guide, replace gaskets (2a) and
put the high pressure insert into position. Tighten the nuts or
screws. Replace the small retention ring (10) after thoroughly
cleaning its seat. Install the diaphragm, taking care to install
the Teflon diaphragm protector (if equipped), towards the
regulator body, lying on the lower diaphragm plate (21).
Replace the diaphragm and spring guide. Tighten the nut
(17), positioning the diaphragm so that when the diaphragm-
bracket assembly is fully rotated to the right and left, each hole
rotates by the same angle as the matching hole on the actuator
flange. This means that the bracket is at right-angles to the
high pressure insert. Match the holes of the diaphragm with
the holes in the actuator flange and install the spring, spring
button and spring case. Install the blindhead (1). Return the
Instructions
EY0171-0172 – 10/08
171 and 172 Series
Self-Operating Pressure Regulators
screw (15) to the position marked by the nut (14) or the posi-
tion you noted down (see 3.4.2.1). Exact calibration must then
be checked when the regulator starts working again.
3.4.3 Replacing the diaphragm
The diaphragm may require replacement without having
to make other repairs. If the regulator is easy to access and
isolate, it can be replaced while leaving the regulator installed
in the piping provided it can be isolated. In this case, isolate
the regulator and vent all pressure. Ensure isolation valves
are locked to prevent accidental pressurization will working on
the regulator. Remove the actuator following the instructions
in section 3.4.2.1.
Replace and install the diaphragm and reassemble the actua-
tor as shown in section 3.4.2.4. Check calibration once more
when the regulator starts working again.
3.5 171 & 172 Versions with
Balancing Spring (Fig.5)
Some versions of the 171 & 172 Series regulators are
equipped with a balancing spring which is mounted on the
blindhead (1) (Fig.1). Note the existence of this spring during
operations involving disassembly and reassembly of the
blindhead (1) (see paragraph 3.4.2.2 - 3.4.2.4).
When welding piping, do not attach the ground to the regulator
as this may damage important sliding parts.
3.5.1 Model 171 with cast iron body
The Model 171 is identical to the 172 in the versions with
threaded ends (Fig.2), except for the following:
- the body is made from cast iron.
The body is closed by means of a threaded disc screwed onto
the body, instead of being attached with screws and nuts.
The inlet and outlet connections are always threaded. There
are therefore no substantial differences with respect to
installation, start-up and calibration, and maintenance.
It should only be remembered that the blindhead is threaded
and screwed to the body. The instructions for the Model 172
in the previous sections also apply to these versions. Remove
the blindhead (1) with a 46 mm hex wrench.
DV-215-171_172 series Inst-v13.indd 5
11/5/08 12:13:38 PM