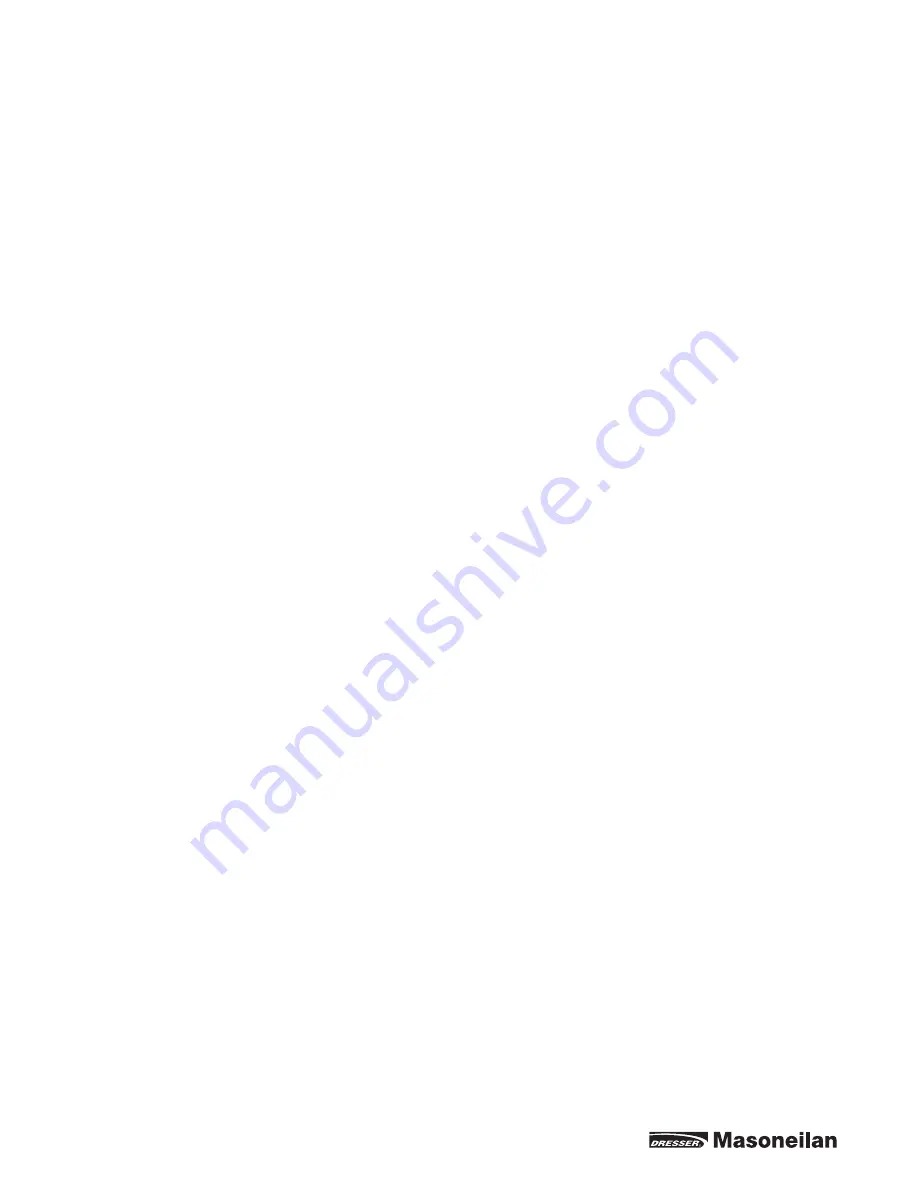
8
4.4.5
Please bear in mind that the regulated pressure sens-
ing port is located inside the regulator, therefore the pressure
drops in the inter-connecting piping between the regulator and
the point of use will affect the accuracy of the maintained set
pressure. This pressure drop must be considered when calcu-
lating the size of the connection piping.
4.4.6
When it is essential to avoid pressure variations at the
point of use, the regulators are fitted with an external sensing
line connection, as shown in Figure 9. The 1/8" female thread-
ed port must be connected to a nipple as near as possible to
the point of use.
4.5 Start-Up and Calibration
4.5.1
This operation is similar for both groups. The sensing
line connection regulator and the upstream and downstream
isolation valves must be closed. Slightly open the downstream
valve and then the upstream valve together with the sensing
line connection, making sure that the pressure difference read
on the pressure gauges is correct. If necessary, to decrease
it, turn the adjustment screw (18) clockwise to increase differ-
ential pressure or counterclockwise to decrease it.
When the required value is reached, fully open all the valves.
When the downstream system is working at full power,
calibrate by adjusting the screw (18).
4.6 Maintenance
4.6.1
The required maintenance interval will vary depend-
ing on application. The user must establish a suitable
maintenance depending on the operating conditions. Prior to
disassembly remove all system pressure from the regulator.
4.6.2 Disassembly
Disassembling and reassembly operations for all types
of 172-50 regulators as long as the different diaphragm
configurations are considered. These are:
- 1 single elastomer diaphragm for 172-50 Single Diaphragm
- 2 elastomer diaphragms (one per side) for 172-50 Double
Diaphragm Version.
4.6.3 Actuator disassembly
Remove spring compression by unscrewing the adjust-
ment screw (counter-clockwise) after loosening the lock nut.
The position of the locknut should be noted to allow closer
preliminary adjustment when reassembling. If the regulator is
equipped with a sealed cap (Fig.4), first remove the cap (30)
and gasket.
Remove the spring housing (9) by loosening the nuts (20).
Note; it is not necessary to remove the housings on actuator
sizes 220 and 360.
Remove the spring. Unscrew the nut (17).
Remove:
- the diaphragm with the relative washers for regulators
172-50 Single Diaphragm.
- the assembly comprising the two diaphragms, washers,
servomotor ring and intermediate plate for regulators 172-50
Double Diaphragm Versions.
The 172-50 regulators comprise two groups of regulators:
Group 1:
All the group 1 regulators have just one diaphragm; one of
the controlled pressures acts under the diaphragm through an
internal sensing line connection while the other acts over the
diaphragm through a sensing line connection on the spring
housing. The plug is kept open by the spring. The following
types belong to this group:
172-50 Single Diaphragm (see Fig. 10);
Group 2:
All the group 2 regulators have two diaphragms separated
by a chamber communicating with the outside; the controlled
pressures act under the lower diaphragm (through an internal
sensing connection) and over the upper diaphragm (through
a sensing line connection on the spring housing). The plug
is kept open by the spring. The following types belong to this
group:
172-50 Double Diaphragm (see Fig. 11)
4.3 Installation
4.3.1
All 172-50 regulators must be installed with the actuator
facing upwards and the diaphragm horizontal.
4.4 Installation Diagrams
In most cases the flow crosses the regulator as shown by the
arrow in Figs. 10-11. The installation diagrams are therefore
as follows:
Group 1 regulators: Fig. 12
Group 2 regulators: Fig. 13
4.4.1
Install an isolation valve upstream, downstream and
on the sensing and discharge line connecting piping, in order
to allow for servicing of the regulator (if necessary) while the
plant is operating. Install one filter or pressure gauge down-
stream from the regulator and another one on the sensing line,
as shown in the diagrams, in order to calibrate the differential
pressure and keep it constantly under control.
4.4.2
Before installing the regulator in the piping, make sure
the insides of the pipes are clean and free of any debris
(machining cuttings, weld slag, etc., especially the upstream
section; blow down the piping if possible to eliminate any
remaining dirt: small drops of weld slag may seriously damage
the regulator.
4.4.3
In group 2 regulators, the chamber between the two
diaphragms must be connected to piping taking the discharge
to a suitable place, safely and constantly at atmospheric
pressure. This hole can be closed with a plug or pressure
gauge with an electrical contact for the remote signaling that
the diaphragm has failed, as long as the downstream piping is
protected as described in section 4.4.4 below.
4.4.4
If there is the slightest possibility of the pressure
downstream from the regulator exceeding the maximum
allowable pressure for the downstream piping or equipment,
a safety valve must be installed, without any isolation valve in
between, capable of discharging the entire flow.
Instructions
EY0171-0172 – 10/08
171 and 172 Series
Self-Operating Pressure Regulators
DV-215-171_172 series Inst-v13.indd 8
11/5/08 12:13:40 PM