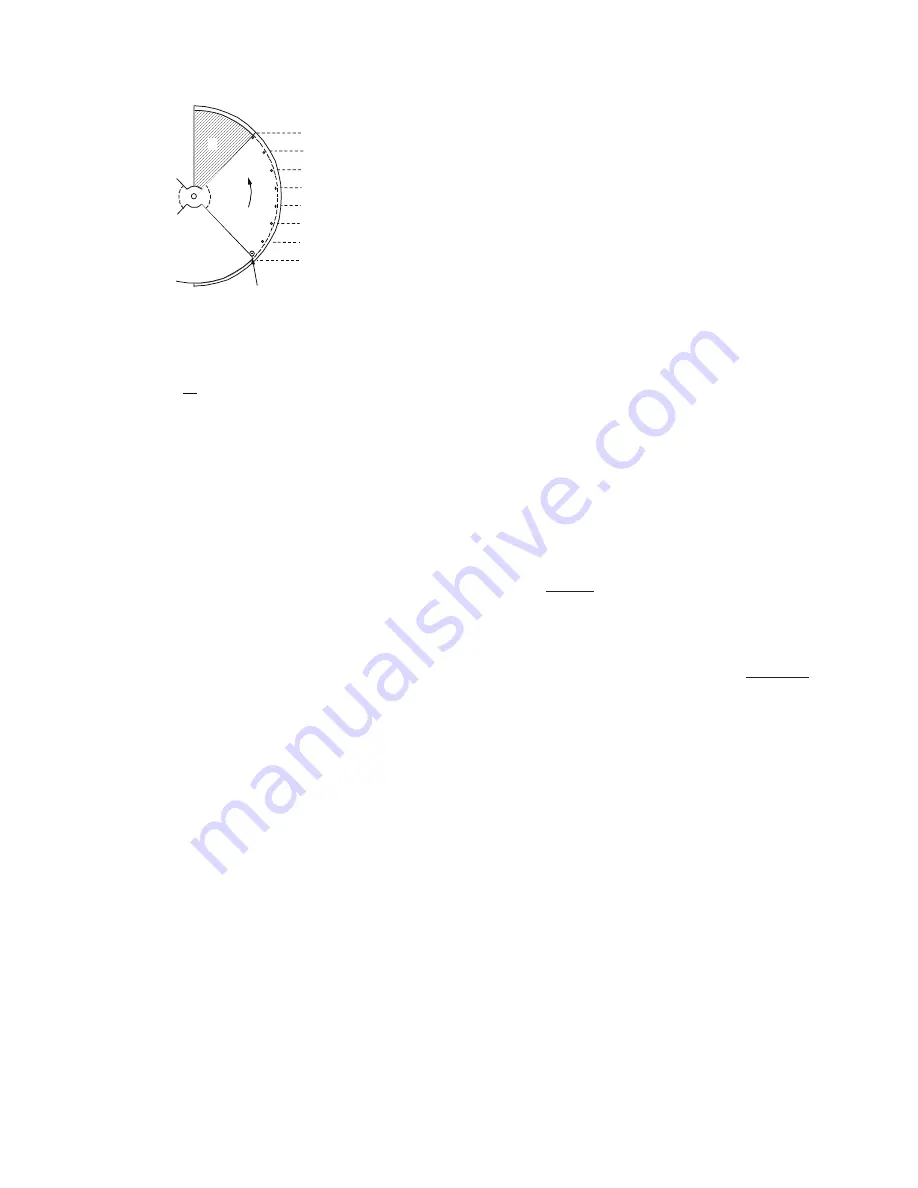
25
Marvair Scholar III™ VAISA I&S Manual 03/2019 Rev. 8
C. GreenWheel
®
ERV. Using best industry standards and practices, measure the fresh
air that is being brought into the classroom. For units with one speed controller (std.),
adjust the speed of the intake and exhaust blowers by inserting a slotted screw
driver into the opening on the controller. The speed controller is located in the control
box. Measure the intake air again and adjust the speed of the blowers. Repeat as
necessary to meet the fresh air requirements.
D. GreenWheel
®
ERV with optional controller for exhaust air and all GreenCube ERV.
First measure the air being introduced into the classroom using best industry
standards and practices. Adjust the speed of the intake air blower until the required
outside air is being brought into the classroom. The speed controller is located in the
control box. Measure the intake air again and adjust the speed of the blower. Repeat
as necessary to meet the fresh air requirement.
Now measure the exhaust air from the classroom. Adjust the speed of the exhaust
air fan until the required air is being exhausted from the classroom. The exhaust air
controller is in the control box. It is usual practice to pressurize the classroom by
exhausting slightly less air than is being brought into the classroom.
1.13 CONTROL ADJUSTMENTS
A.
Scholar III™ Heat Pump and Air Conditioner PLC (Programmable Logic
Controller) Microprocessor
. Essential to the operation of the Scholar III heat pump
and air conditioner is a factory installed PLC microprocessor. The PLC controller
improves reliability due to a reduction of components and simplification of the control
panel wiring. The PLC is able to:
• Provide various control functions
• Show operational status through LED’s
• Assist in troubleshooting
• Perform extensive self diagnosis and indicate a fault
• Store statistical operational data
• Be programmed remotely or with a removable program storage device
The PLC is factory wired and tested and typically no adjustments or changes are
required to the PLC when the Scholar III™ heat pump or air conditioner is installed.
Figure 11. Motorized and PowerVent System Calibration Procedure
Inside the lower section, locate the circular calibration plates
as noted above in the drawing (“A” is fixed, “B” is movable).
Remove the screw shown by the arrow from “motorized settings.”
Reinsert the screw into the hole in plate B adjacent to the
desired air flow rate, in CFM, and firmly drive the screw in until
it bottoms out at the screw head.
Note: Motor drives plate B open to setting
when control relay (VMR) is energized.
Motor drives plate B to the closed position
when control relay (VMR) is deenergized.
Operation is the same for the "Motorized"
and "PowerVent" systems.
A
B
Motorized Settings
(shown in closed position)
20 - 50 CFM
160 CFM
230 CFM
285 CFM
325 CFM
355 CFM
380 CFM
FULL OPEN
420-450 CFM