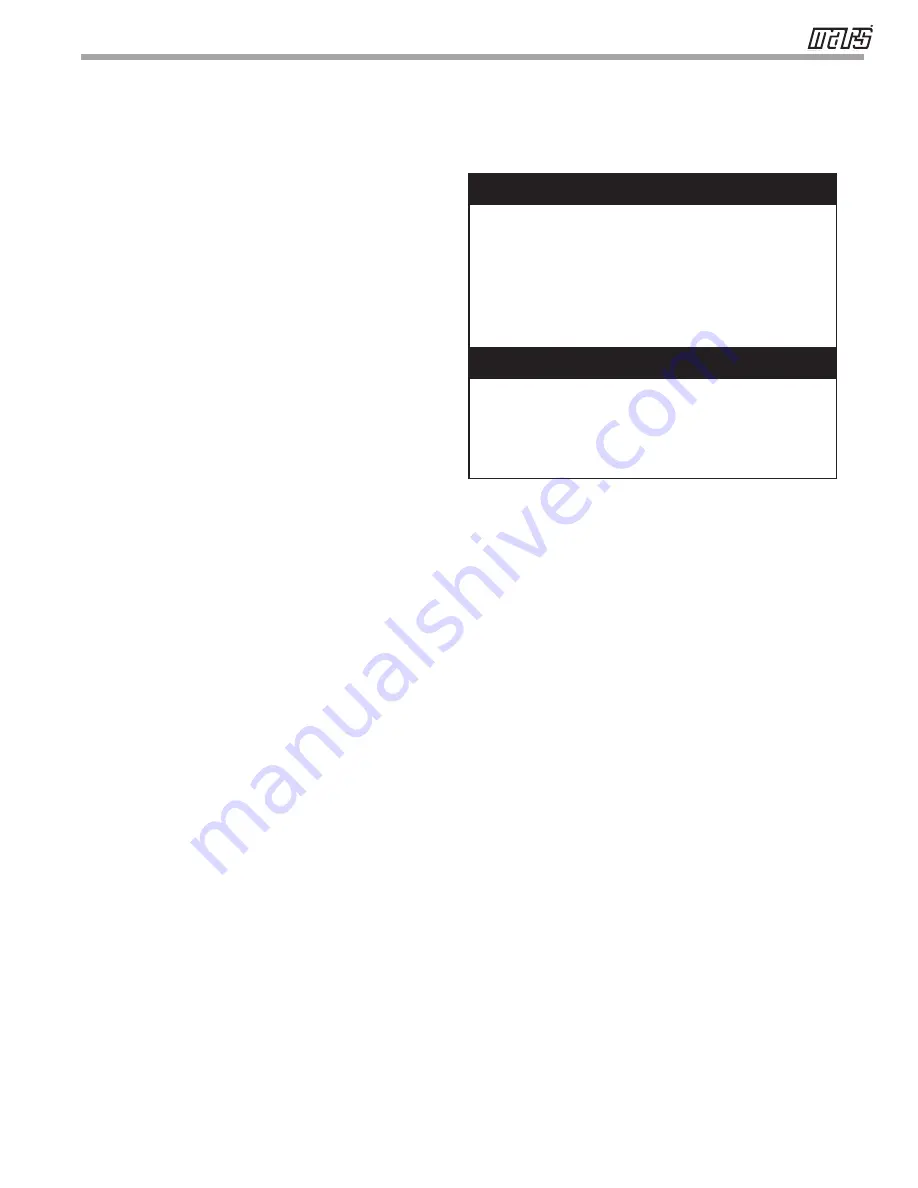
Installation, Operation & Maintenance - HNW Series
General Information
�
CAUTION!
�
�
CAUTION!
�
CAUTION!
DO NOT store or install units in corrosive
environments or in locations subject to temperature or
humidity extremes (e.g., attics, garages, rooftops, etc.).
Corrosive conditions and high temperature or humidity
can significantly reduce performance, reliability, and
service life. Always move and store units in an upright
position. Tilting units on their sides may cause equipment
damage.
CAUTION!
CUT HAZARD - Failure to follow this caution
may result in personal injury. Sheet metal parts may have
sharp edges or burrs. Use care and wear appropriate
protective clothing, safety glasses and gloves when
handling parts and servicing heat pumps.
5
Inspection
Upon receipt of the equipment, carefully check the shipment
against the bill of lading. Make sure all units have been
received. Inspect the carton or crating of each unit, and
inspect each unit for damage. Assure the carrier makes
proper notation of any shortages or damage on all copies of
the freight bill and completes a common carrier inspection
report. Concealed damage not discovered during unloading
must be reported to the carrier within 15 days of receipt of
shipment.
If not filed within 15 days, the freight company
can deny the claim without recourse. Note: It is the
responsibility of the purchaser to file all necessary claims
with the carrier.
Storage
Equipment should be stored in its original packaging in a
clean, dry area. Store units in an upright position at all times.
The stack limit for HNW036, 060 and 120 is three.
Unit Protection
Cover units on the job site with either shipping packaging,
vinyl film, or an equivalent protective covering. Cap the open
ends of pipes stored on the job site. In areas where painting,
plastering, and/or spraying has not been completed, all
due precautions must be taken to avoid physical damage
to the units and contamination by foreign material. Physical
damage and contamination may prevent proper start-up and
may result in costly equipment clean-up.
Examine all pipes, fittings, and valves before installing any of
the system components. Remove any dirt or trash found in
or on these components.
Pre-Installation
Installation, Operation, and Maintenance instructions are
provided with each unit.. The installation site chosen should
include adequate service clearance around the unit. Before
unit start-up, read all manuals and become familiar with the
unit and its operation. Thoroughly check the system before
operation.
Prepare units for installation as follows:
1. Compare the electrical data on the unit nameplate with
ordering and shipping information to verify that the
correct unit has been shipped.
2. Keep the cabinet covered with the shipping packaging
until installation is complete and all plastering, painting,
etc. is finished.
3. Verify refrigerant tubing is free of kinks or dents and that
it does not touch other unit components.
4. Inspect all electrical connections. Connections must be
clean and tight at the terminals.