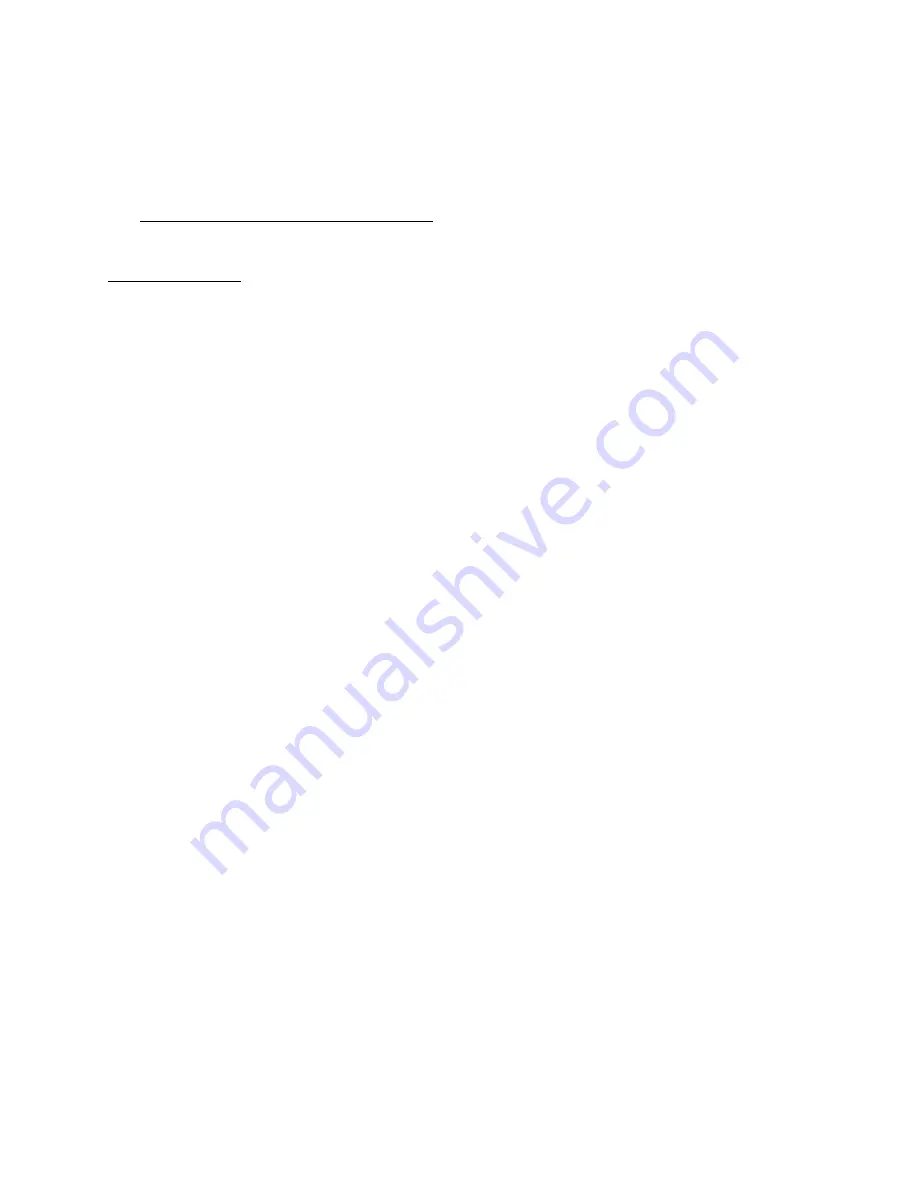
INSTALLATION AND OPERATION MANUAL AND PARTS,
ELECTRIC CONVECTION STEAMERS, MODELS: ST-7-TE, ST-10-TE
PART NUMBER 10175R2
13
2006-01-19
4.0 SUGGESTED COOKING GUIDELINES
COOKING HINTS
Your steamer efficiently cooks vegetables or other foods for immediate serving. Steam cooking
should be carefully time controlled. Keep hot food holding-time to a minimum to produce the
most appetizing results. Prepare small batches, cook only enough to start serving, then cook
additional amounts to meet demand.
Preparation
Prepare vegetables, fruits, meats, seafood, and poultry normally by cleaning, separating,
cutting, removing stems, etc. Cook root vegetables in a perforated pan. Other vegetables may
be cooked in a perforated pan unless juices are being saved. Liquids can be collected in a
solid pan placed under a perforated pan.
Perforated pans are used for frankfurters, wieners, and similar items when juices do not need to
be preserved. Solid pans are good for cooking puddings, rice and hot breakfast cereals.
Vegetables and fruits are cooked in solid pans in their own juice. Meats and poultry are cooked
in solid pans to preserve their juice or return broth.
Canned foods can be heated in their opened cans (cans placed in solid pans), or the contents
may be poured into solid pans. DO NOT place unopened cans in the steamer.
Frozen Food Items
Separate frozen foods into smaller pieces to allow more efficient cooking.
Use a pan cover for precooked frozen dishes that cannot be cooked in the covered containers
in which they are packed if they require more than 15 minutes of cooking time. When a cover
is used, approximately one-third additional cooking time is necessary. Cooking time for frozen
foods depends on the amount of defrosting required. If time permits, allow frozen foods to
partially thaw overnight in a refrigerator. This will reduce their cooking time.