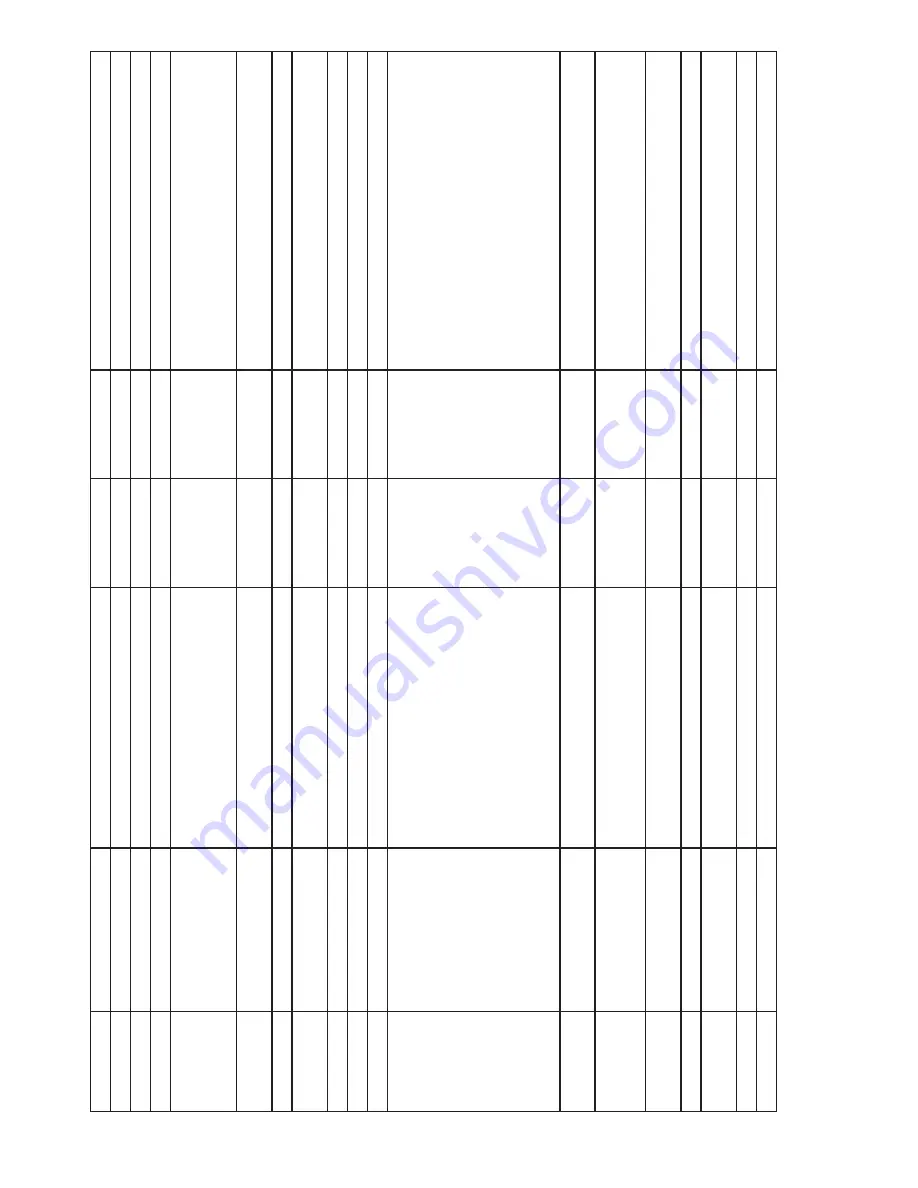
20
User men
u
Submen
u 1
Submen
u 2
Submen
u 3
Submen
u 4
Notes
1.
HEA
TING
Heating user settings
1.
CH temperatur
e/O
TC set
Set the CH temperatur
es and O
TC cur
ves parameters
1.
CH setpoint
Adjust setpoint of CH cir
cuit
2.
Outside temperatur
e f
or CH off
Set the external temperatur
e at which heat demand is
remo
ved.
If set OFF
, heat demand will ne
ver be r
emo
ved
by contr
oller (onl
y b
y r
emo
ving R
T or bridge betw
een
terminal strip C2:1,2)
2.
Eco setpoint r
eduction
Set the temperatur
e that will be subtracted fr
om the actual
setpoint when ECO mode is activated
3.
Scheduler set
In
vok
e scheduler men
u
1.
Enable/disable on boar
d scheduler
Based on selection is possible to enable/disable on boar
d
scheduler
Enable
Enable on boar
d scheduler
Disable
Disable on boar
d scheduler
2.
Scheduler set
Select to set scheduler
1 Monda
y
2 T
uesda
y
3 W
ednesda
y
4 Thursda
y
5 Frida
y
6 Satur
da
y
7 Sunda
y
8 Monda
y-Frida
y
9 Monda
y-Sunda
y
10 Satur
da
y-
Sunda
y
Used to pr
ogram on boar
d scheduler (On,
Off,
Eco)
2.
DOMESTIC
HO
T W
A
TER
Domestic hot water user settings
1 DHW set point
Set the DHW temperatur
e (in case of a DHW with sensor
this is the actual DHW temperatur
e,
in case of DHW with
thermostat this is the base boiler flo
w temperatur
e).
2.
ECO set point r
eduction
Set the temperatur
e that will be substracted fr
om the
actual setpoint when ECO mode is activated.
3.
Scheduler set
In
vok
e scheduler men
u
1.
Enable/disable on boar
d scheduler
Based on selection possible to enable/disable DHW on boar
d scheduler
Enable
Enable on boar
d scheduler
Disable
Disable on boar
d scheduler
Summary of Contents for MEGAFLEX
Page 1: ...EN 1 Technical manual MARK MEGAFLEX 0660440 ...
Page 11: ...EN 11 3 DIMENSIONS ...
Page 46: ...46 ...
Page 54: ...54 ...
Page 56: ...56 ...