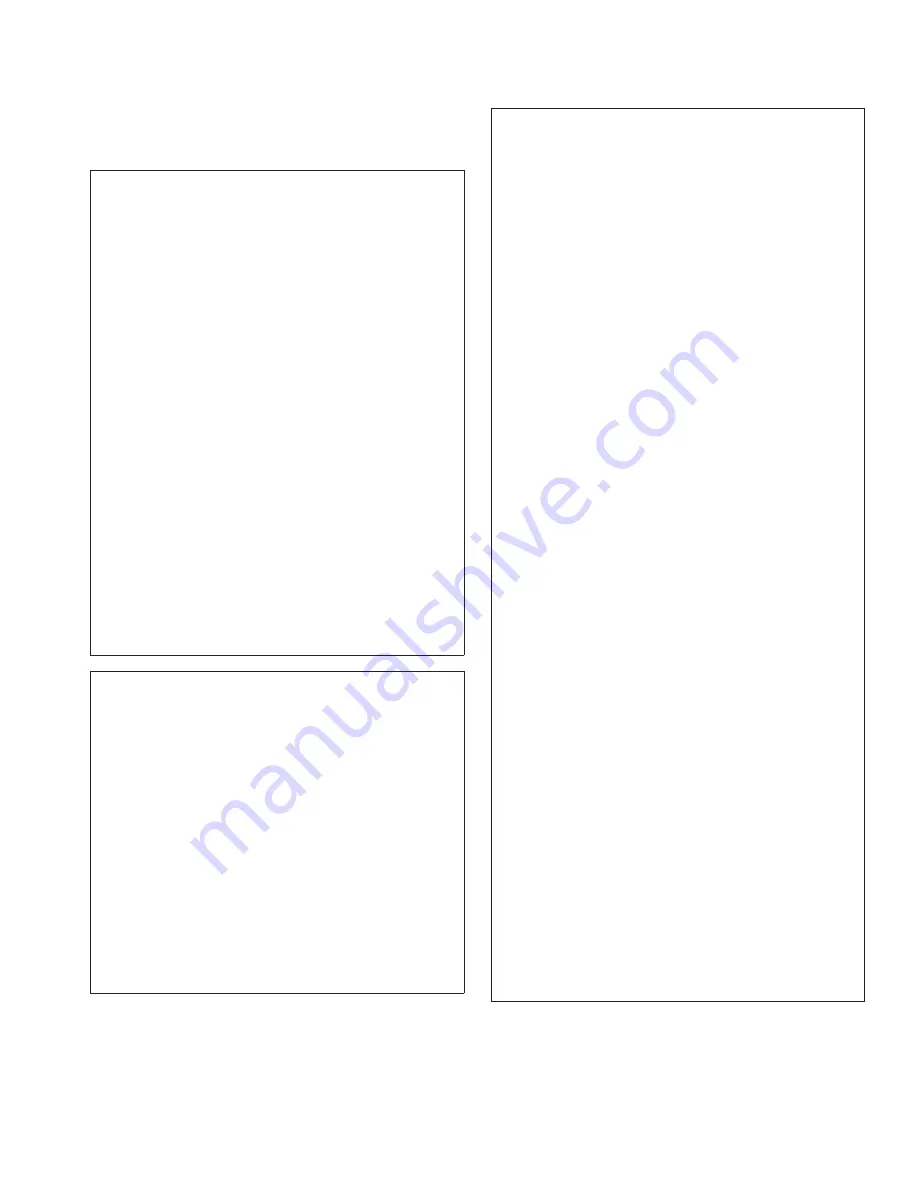
Safety Notices
Safety Notices
Read these precautions to prevent personal injury:
• Read this manual thoroughly before operating,
installing or performing maintenance on the
equipment. Failure to follow instructions in this
manual can cause property damage, injury or death.
• Routine adjustments and maintenance procedures
outlined in this manual are not covered by the
warranty.
• Proper installation, care and maintenance are essential
for maximum performance and trouble-free operation
of your equipment.
Visit our website www.manitowocice.com for manual
updates, translations, or contact information for
service agents in your area.
• This equipment contains high voltage electricity and
refrigerant charge. Installation and repairs are to be
performed by properly trained technicians aware of
the dangers of dealing with high voltage electricity
and refrigerant under pressure. The technician must
also be certified in proper refrigerant handling
and servicing procedures. All lockout and tag out
procedures must be followed when working on this
equipment.
• This equipment is intended for indoor use only. Do
not install or operate this equipment in outdoor areas.
n
Warning
Follow these electrical requirements during
installation of this equipment.
• All field wiring must conform to all applicable
codes of the authority having jurisdiction. It is
the responsibility of the end user to provide the
disconnect means to satisfy local codes. Refer to rating
plate for proper voltage.
• This appliance must be grounded.
• This equipment must be positioned so that the plug is
accessible unless other means for disconnection from
the power supply (e.g., circuit breaker or disconnect
switch) is provided.
• Check all wiring connections, including factory
terminals, before operation. Connections can become
loose during shipment and installation.
n
Warning
Follow these precautions to prevent personal injury
during installation of this equipment:
• Installation must comply with all applicable
equipment fire and health codes with the authority
having jurisdiction.
• To avoid instability the installation area must be
capable of supporting the combined weight of the
equipment and product. Additionally the equipment
must be level side to side and front to back.
• Ice machines require a deflector when installed on
an ice storage bin. Prior to using a non-OEM ice
storage system with this ice machine, contact the
bin manufacturer to assure their ice deflector is
compatible.
• Remove all removable panels before lifting and
installing and use appropriate safety equipment
during installation and servicing. Two or more people
are required to lift or move this appliance to prevent
tipping and/or injury.
• Do not damage the refrigeration circuit when
installing, maintaining or servicing the unit.
• Connect to a potable water supply only.
• This equipment contains refrigerant charge.
Installation of the line sets must be performed by
a properly trained and EPA certified refrigeration
technician aware of the dangers of dealing with
refrigerant charged equipment.
• Legs or casters must be installed and the legs/casters
must be screwed in completely. When casters are
installed the mass of this unit will allow it to move
uncontrolled on an inclined surface. These units must
be tethered/secured to comply with all applicable
codes. Swivel casters must be mounted on the front
and rigid casters must be mounted on the rear. Lock
the front casters after installation is complete.
• Some 50 Hz models may contain up to 150 grams
of R290 (propane) refrigerant. R290 (propane)
is flammable in concentrations of air between
approximately 2.1% and 9.5% by volume (LEL lower
explosion limit and UEL upper explosion limit). An
ignition source at a temperature higher than 470°C is
needed for a combustion to occur. Refer to nameplate
to identify the type of refrigerant in your equipment.
Only trained and qualified personnel aware of the
dangers are allowed to work on the equipment.
Summary of Contents for Manitowoc NEO U0140 Series
Page 2: ......
Page 16: ...16 Part Number 040005890 Rev 04 02 19 Operation Section 3 THIS PAGE INTENTIONALLY LEFT BLANK ...
Page 23: ......