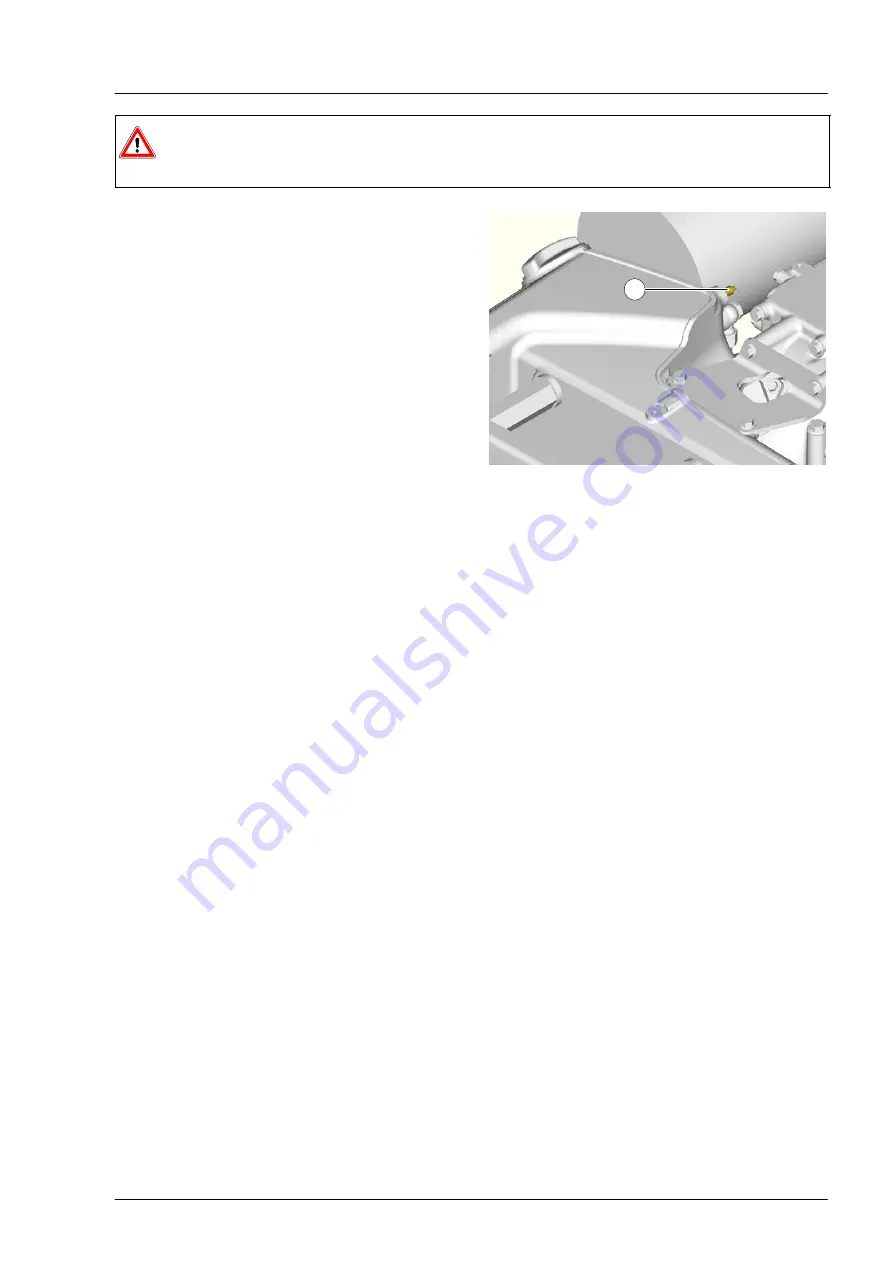
First commissioning − Cooling system
75
Danger:
If in an
exceptional case
the coolant level has to be checked with the engine still hot from
operation, first carefully loosen the locking cap − relieve the pressure − then open carefully.
If the cooling system is opened with the engine hot
from operation, this will cause a loss of pressure in
the cooling system.
On continuing engine operation, this may lead to
the engine monitoring system MMDS triggering the
Pressure in expansion tank" alarm. The
consequence of this alarm is a reduction in engine
power.
There must be a pre−start up pressure of 0.7 bar in
the cooling system in order to be able to operate
the hot engine again, without the alarm, after
opening the locking cap.
To achieve this, a pressure valve
À
is mounted on
the expansion tank, to which a normal
commercially−available air pump can be
connected. The pump can be used to pump the
system pressure up to 0.7 bar.
1
Summary of Contents for V12-1800
Page 1: ......
Page 2: ......
Page 12: ...Planning of engine installation 10 V12 1800 1 2 3 4 5 V8 1200 6 7 8 9 4 10 11...
Page 78: ...Notes 76...
Page 79: ...77 Appendix...
Page 80: ......
Page 91: ......
Page 92: ......