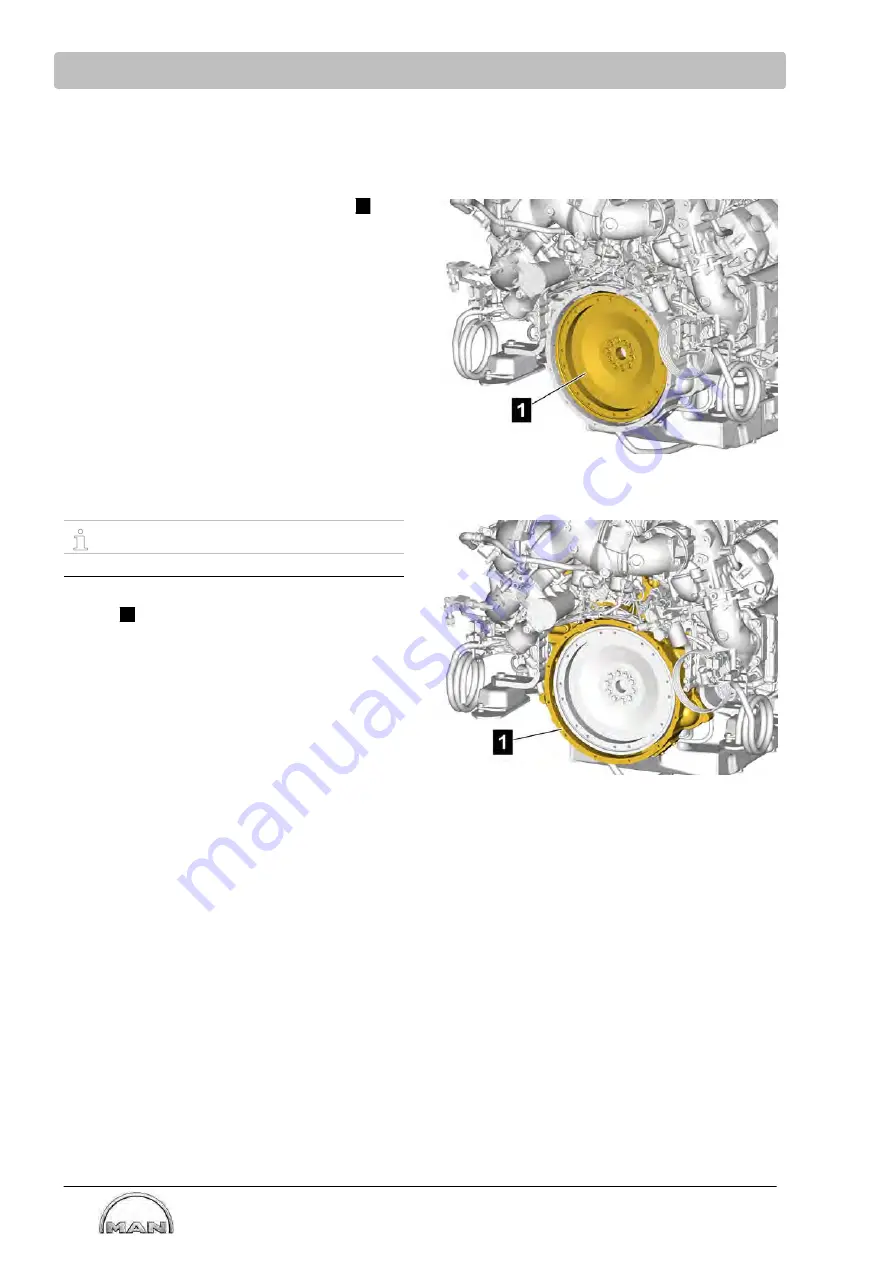
Installation and commissioning
MAN marine diesel engines D2868 LE4.. / D2862 LE4..
46
Carefully read through the Operating Instructions before starting any work!
This particularly applies to the General Safety Instructions section
and the safety instructions in the various chapters.
6.3.2
Mounting a gearbox on the flywheel housing
Flywheel
The connection dimensions for the flywheel
1
are
indicated on the installation drawing.
S
Remove oil, grease and preservative from the
flywheel.
Flywheel housing
User tip
For bolt tightening torques, see page 56.
Details of the dimensions for the flywheel
housing
1
and the type of threaded connections
for mounting the gearbox are included on the in
stallation drawing.