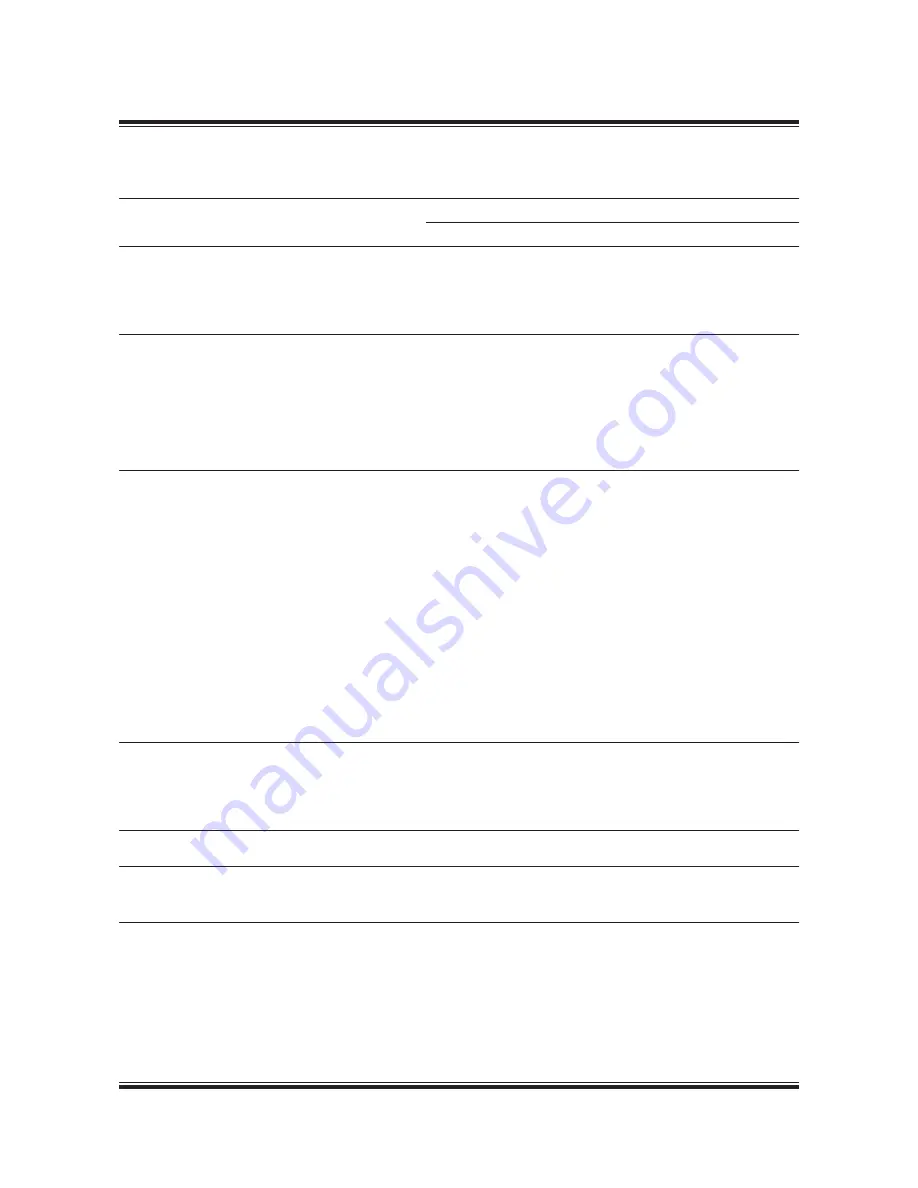
MAN Diesel
4.08
Page 3 of 3
MAN Diesel
198 42 078.5
MAN B&W S80MC/MC-C/ME-C, K80MC-C/ME-C, S70MC/MC-C/ME-C/ME-GI,
L70MC-C/ME-C, S65ME-C/ME-GI, S60MC/MC-C/ME-C/ME-GI/ME-B,
L60MC-C/ME-C, S50MC/MC-C/ME-C/ME-B, S46MC-C/ME-B, S42MC,
S40MC-C/ME-B, S35MC/MC-C/ME-B, L35MC, S26MC
Fig. 4.08.02b: List of capacities for L23/30H, 900 rpm, IMO Tier I.
L23/30H GenSet Data
Cyl.
6
7
8
Max. continuous rating at
900 RPM
kW
960
1,120
1,280
Engine-driven Pumps:
Fuel oil feed pump
(5.5-7.5 bar) m
3
/h
1.3
1.3
1.3
L.T. cooling water pump
(1-2.5 bar) m
3
/h
69
69
69
H.T. cooling water pump
(1-2.5 bar) m
3
/h
45
45
45
Lub. oil main pump
(3.5-5 bar) m
3
/h
20
20
20
Separate Pumps:
Diesel oil pump
(4 bar at fuel oil inlet A1) m³/h
0.69
0.81
0.92
Fuel oil supply pump***
(4 bar discharge pressure) m
3
/h
0.34
0.40
0.45
Fuel oil circulating pump
(8 bar at fuel oil inlet A1) m³/h
0.70
0.82
0.94
L.T. cooling water pump*
(1-2.5 bar) m
3
/h
52
61
70
L.T. cooling water pump**
(1-2.5 bar) m
3
/h
63
71
85
H.T. cooling water pump
(1-2.5 bar) m
3
/h
30
35
40
Lub. oil stand-by pump
(3.5-5 bar) m
3
/h
17
18
19
Cooling Capacities:
Lubricating Oil:
Heat dissipation
kW
117
137
158
L.T. cooling water quantity*
m
3
/h
7.5
8.8
10.1
SW L.T. cooling water quantity**
m
3
/h
18
18
25
Lub. oil temp. inlet cooler
°C
67
67
67
L.T. cooling water temp. inlet cooler
°C
36
36
36
Charge Air:
Heat dissipation
kW
369
428
487
L.T. cooling water quantity
m
3
/h
46
53
61
L.T. cooling water inlet cooler
°C
36
36
36
Jacket Cooling:
Heat dissipation
kW
239
281
323
H.T. cooling water quantity
m
3
/h
30
35
40
H.T. cooling water temp. inlet cooler
°C
77
77
77
Gas Data:
Exhaust gas flow
kg/h
8,370
9,770
11,160
Exhaust gas temp.
°C
325
325
325
Max. allowable back. press.
bar
0.025
0.025
0.025
Air consumption
kg/s
2.25
2.62
3.00
Startiang Air System:
Air consumption per start
Nm
3
2.0
2.0
2.0
Haeat Radiation:
Engine
kW
32
37
42
Generator
kW
(See separat data from generator maker)
If L.T. cooling are sea water, the L.T. inlet is 32° C instead of 36° C.
Based on tropical conditions, except for exhaust flow and air consumption which are based on ISO conditions.
* Only valid for engines equipped with internal basic cooling water system nos. 1 and 2.
** Only valid for engines equipped with combined coolers, internal basic cooling water system no. 3.
*** To compensate for built on pumps, ambient condition, calorific value and adequate circulations flow. The ISO fuel oil consumption is
multiplied by 1.45.
Summary of Contents for B&W S50MC-C8-TII
Page 4: ......
Page 10: ......
Page 18: ......
Page 19: ...MAN B W MAN Diesel Engine Design 1 ...
Page 20: ......
Page 35: ...MAN B W MAN Diesel Engine Layout and Load Diagrams SFOC 2 ...
Page 36: ......
Page 52: ......
Page 64: ......
Page 65: ...MAN B W MAN Diesel Turbocharger Selection Exhaust Gas By pass 3 ...
Page 66: ......
Page 72: ......
Page 73: ...MAN B W MAN Diesel Electricity Production 4 ...
Page 74: ......
Page 106: ......
Page 107: ...MAN B W MAN Diesel Installation Aspects 5 ...
Page 108: ......
Page 146: ......
Page 170: ......
Page 171: ...MAN B W MAN Diesel List of Capacities Pumps Coolers Exhaust Gas 6 ...
Page 172: ......
Page 192: ......
Page 193: ...MAN B W MAN Diesel Fuel 7 ...
Page 194: ......
Page 208: ......
Page 209: ...MAN B W MAN Diesel Lubricating Oil 8 ...
Page 210: ......
Page 223: ...MAN B W MAN Diesel Cylinder Lubrication 9 ...
Page 224: ......
Page 233: ...MAN B W MAN Diesel Piston Rod Stuffing Box Drain Oil 10 ...
Page 234: ......
Page 236: ......
Page 237: ...MAN B W MAN Diesel Central Cooling Water System 11 ...
Page 238: ......
Page 243: ...MAN B W MAN Diesel Seawater Cooling System 12 ...
Page 244: ......
Page 254: ......
Page 255: ...MAN B W MAN Diesel Starting and Control Air 13 ...
Page 256: ......
Page 262: ......
Page 263: ...MAN B W MAN Diesel Scavenge Air 14 ...
Page 264: ......
Page 276: ......
Page 277: ...MAN B W MAN Diesel Exhaust Gas 15 ...
Page 278: ......
Page 292: ......
Page 293: ...MAN B W MAN Diesel Engine Control System 16 ...
Page 294: ......
Page 309: ...MAN B W MAN Diesel Vibration Aspects 17 ...
Page 310: ......
Page 324: ......
Page 325: ...MAN B W MAN Diesel Monitoring Systems and Instrumentation 18 ...
Page 326: ......
Page 348: ......
Page 349: ...MAN B W MAN Diesel Dispatch Pattern Testing Spares and Tools 19 ...
Page 350: ......
Page 388: ......
Page 389: ...MAN B W MAN Diesel Project Suppport and Documentation 20 ...
Page 390: ......
Page 399: ...MAN B W MAN Diesel Appendix A ...
Page 400: ......